Where is HyperX Software used?
Scroll down to see where HyperX has been used in the past.
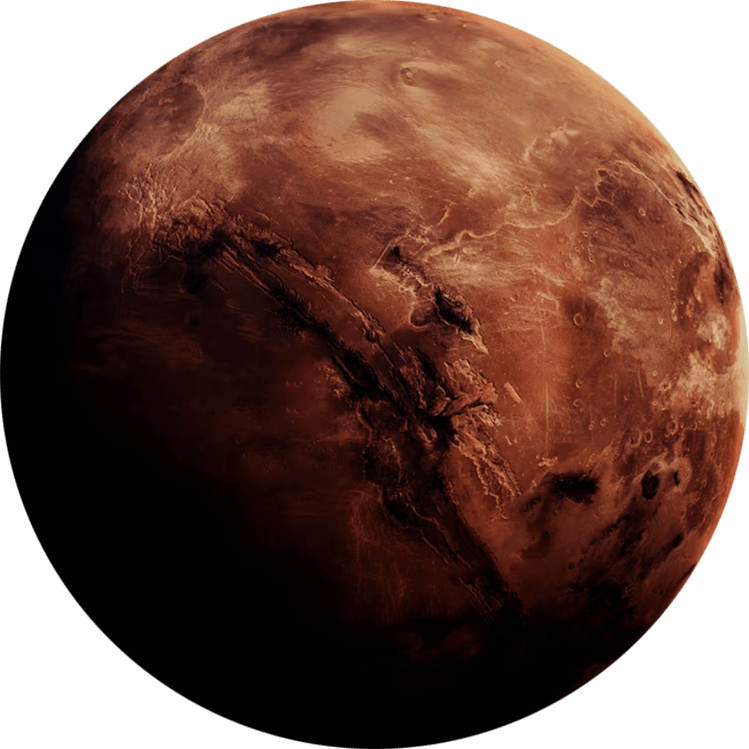
190,000,000
Altitude: Miles
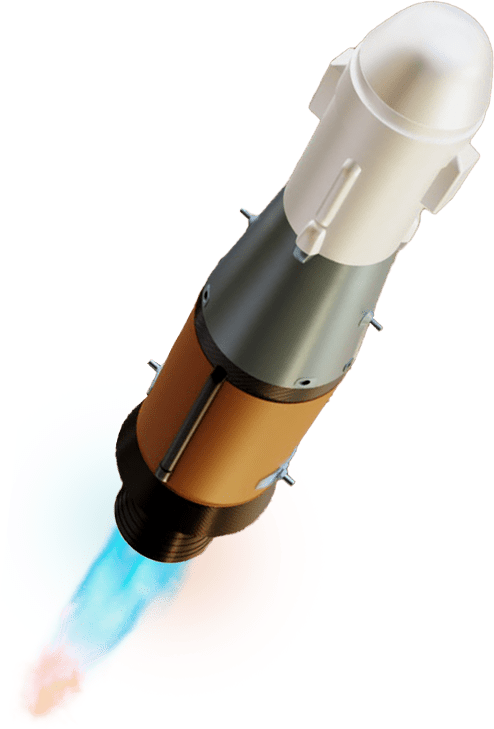
Mars Sample Return Capsule
NASA and the European Space Agency (ESA) are planning ways to bring the first samples of Mars material back to Earth for detailed study.
Collier Research Engineers using HyperSizer have been designing and analyzing the secure containment capsule for safe delivery to Earth.
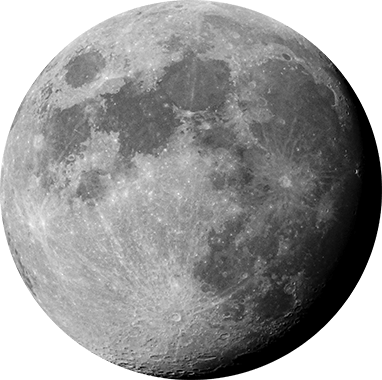
239,000
Altitude: Miles
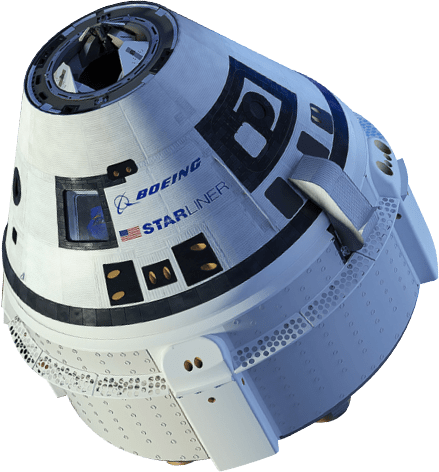
Boeing CST 100 Commercial Crew Module
HyperSizer was used extensively by Boeing for design and analysis of their CST 100 astronaut crew module to support NASA manned missions to the moon. Boeing flew the Orbital Flight Test 2 on May 19, 2022
Blue Origin Moon Lander
Blue Origin will design, develop, test, and verify its Blue Moon lander to meet NASA’s human landing system requirements for recurring astronaut expeditions to the lunar surface, including docking to a space station where crew transfer in lunar orbit.
The total award value of the Artemis V mission firm-fixed price contract is $3.4 billion. HyperX is currently being used on this project.
239,000
Altitude: Miles
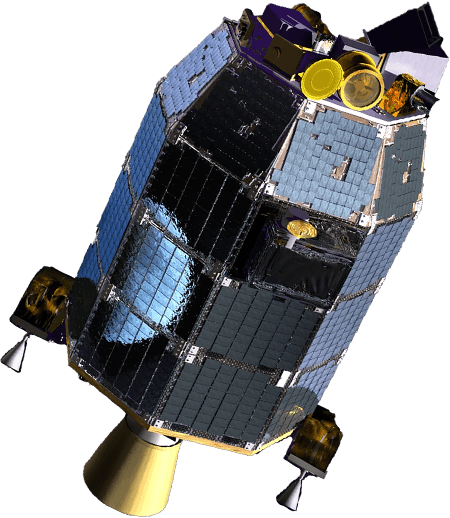
NASA Ames Lunar Atmosphere Dust and Environment Explorer (LADEE) Satellite
LADEE circled the moon for 100 days in 2014.
HyperX was used to resolve negative margins and get weight out for new load cycles.
“In all, the software calculated 1 billion structural margins and organized the data into detailed illustrations of critical loads and failure modes.” See News Article: Machine Design – Software Lets Spacecraft Carry Heavier Load
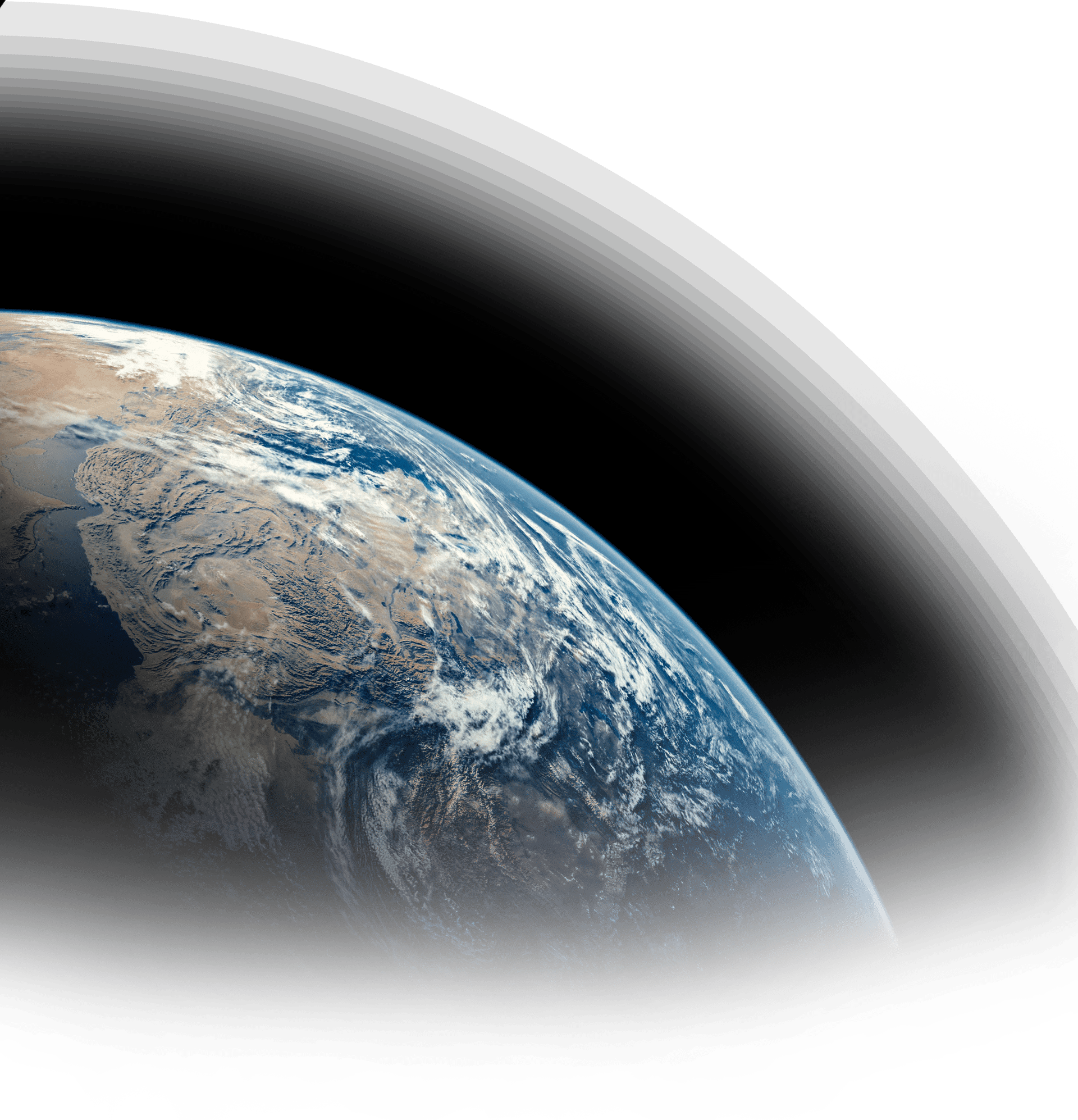
310
Altitude: Miles
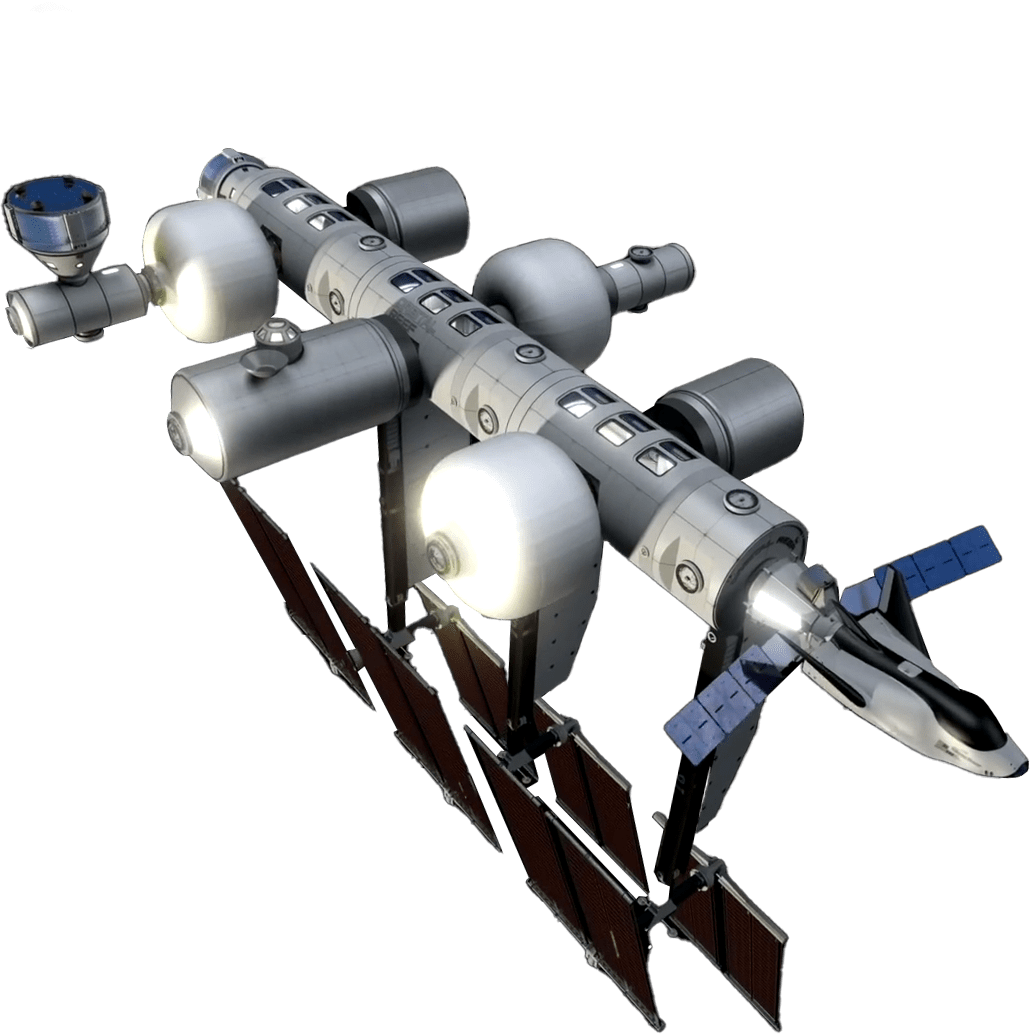
Blue Origin’s Orbital Reef Space Station
Orbital Reef will be a space station in low Earth orbit for commerce, research, and tourism by the end of this decade.
Commercially developed and owned, the Orbital Reef team has been awarded NASA funding.
HyperX is being used by Blue Origin and by Collier Engineers for its design and analysis.
Sierra Space Dream Chaser Space Vehicle
The First-Ever Winged Commercial Spaceplane. After returning from space, can land like conventional aircraft on runway landings.
“The software’s suite of industry-standard failure criteria was extremely valuable for our team, enabling us to quickly size the Dream Chaser structure and perform architectural trade studies,” says Andy Kim, Senior Structural Engineer for SNC.
“The software’s rapid sizing capability gave us more time to interrogate our results and gain insights into the sensitivity of the structural weight to various design features and stiffener cross sections.”
Net Composites – HyperSizer Aids Design of Dream Chaser Spacecraft
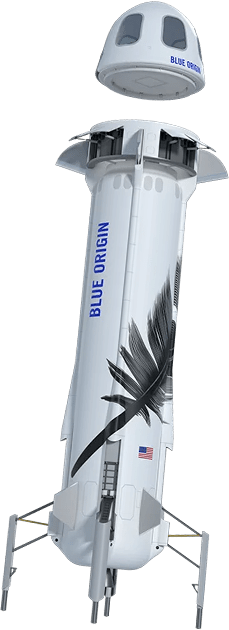
Blue Origin’s New Shepard Rocket and Space Capsule
A reusable suborbital rocket system designed to take astronauts past the Kármán line. The crew capsule carries six passengers with the large windows for viewing space.
HyperX is being used by Blue Origin and by Collier Engineers for its design and analysis.
62
Altitude: Miles
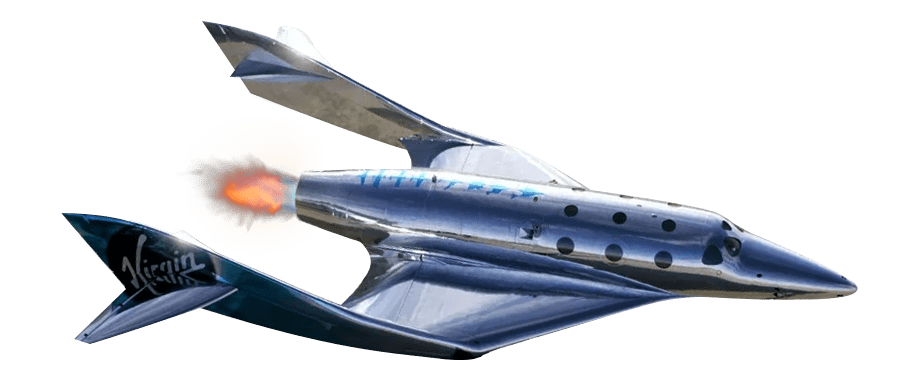
Scaled Composites SpaceShipTwo
is an air-launched suborbital spaceplane designed for space tourism. It is carried to its launch altitude by a Scaled Composites White Knight Two, before being released to fly on into the upper atmosphere powered by its rocket engine. It then glides back to Earth and performs a conventional runway landing.
HyperSizer was used by Scaled for its design and analysis.
Bell Textron is designing and manufacturing the feather system of the next Delta Class spaceships. Bell is using HyperX for design and analysis.
54
Altitude: Miles
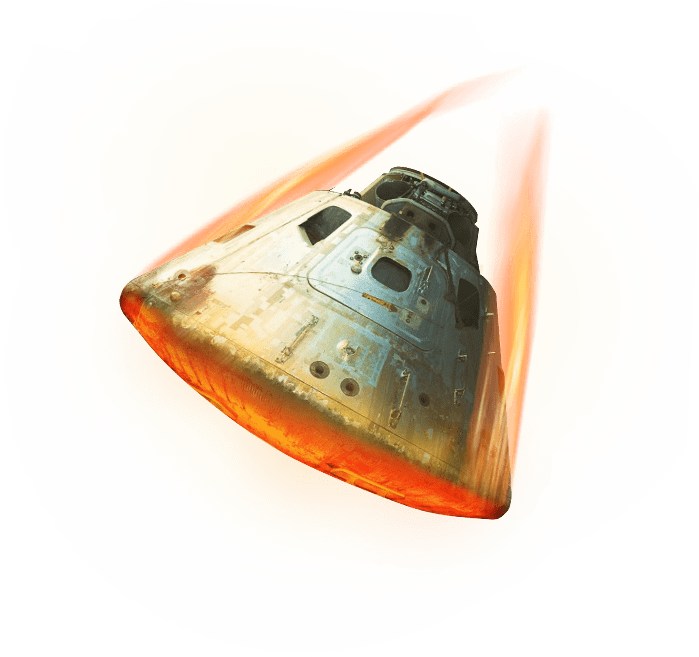
Orion Crew Module Heat Shield
Orion Crew Module Heat Shield illustrated at peak heating altitude.
Lightweighting is especially important for these structure, and the structural design is a combined structural thermal protection design challenge.
“We needed to come up with a lighter structure that could withstand the aerodynamic pressure of the Earth’s atmosphere re-entry, and support the thermal protection heat shield,” said Mike Kirsch of NASA Langley
HyperSizer evaluated different structural concepts for the heat shield carrier structure. The baseline composite skin with Titanium I stringers (left, bottom) was evaluated against alternate metallic grid stiffened designs (right, top and bottom).
36
Altitude: Miles
60,000
Altitude: Feet
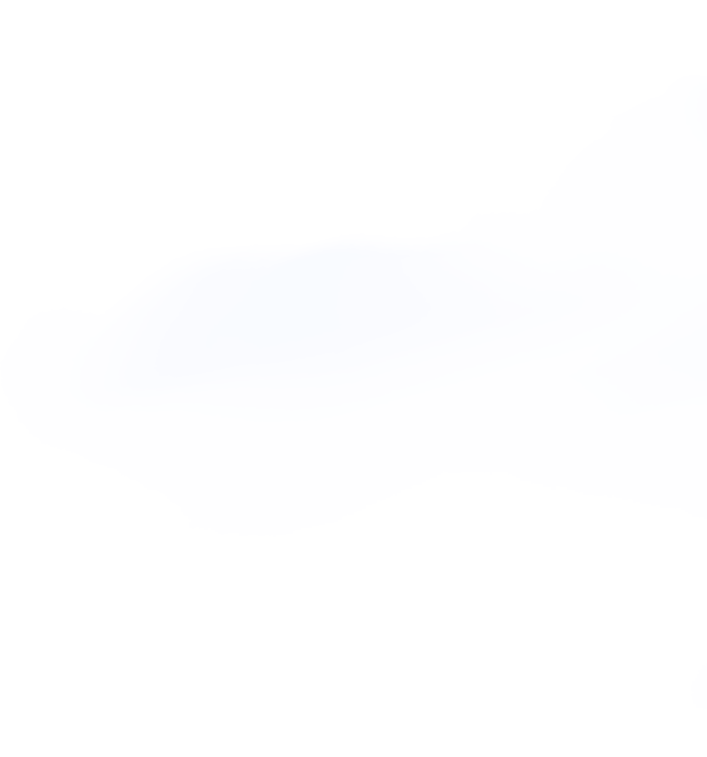
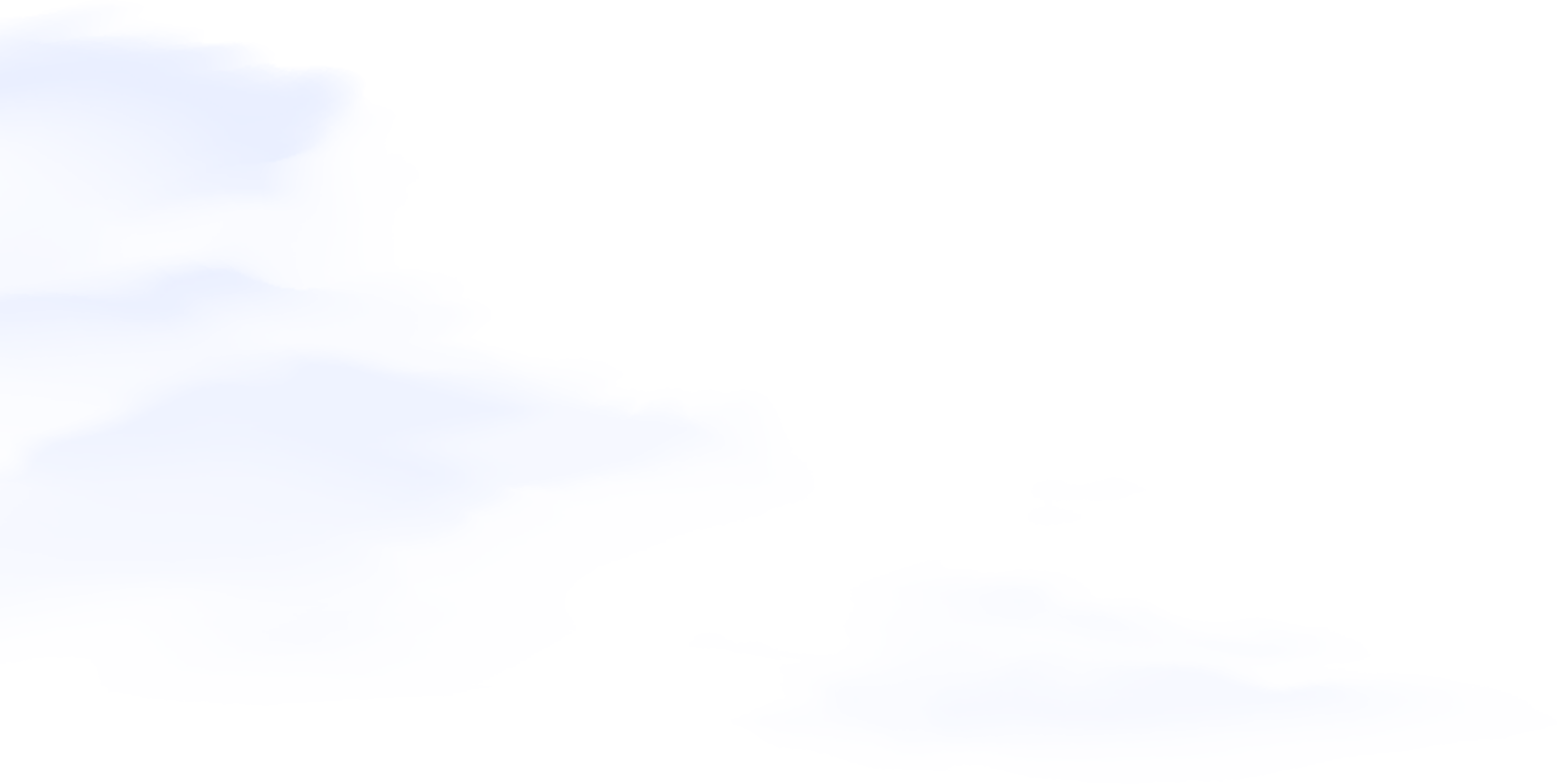
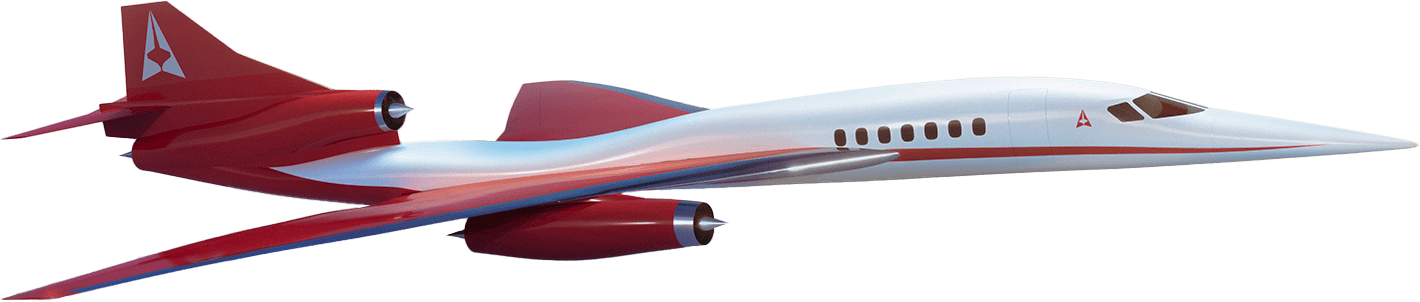
Aerion AS2 supersonic business jet
In April 2020, Aerion Corporation unveiled an updated design for the 12 passenger jet, reaching Mach 1.4 in supercruise with nonafterburning engines, over 5,000 nmi (9,300 km).
After 17 years of development, in May 2021 Aerion shutdown for business and the AS2 was never built. However its composite stiffened panel wing was highly optimized with HyperSizer by Aerion and Collier Aerospace employees.
41,000
Altitude: Feet
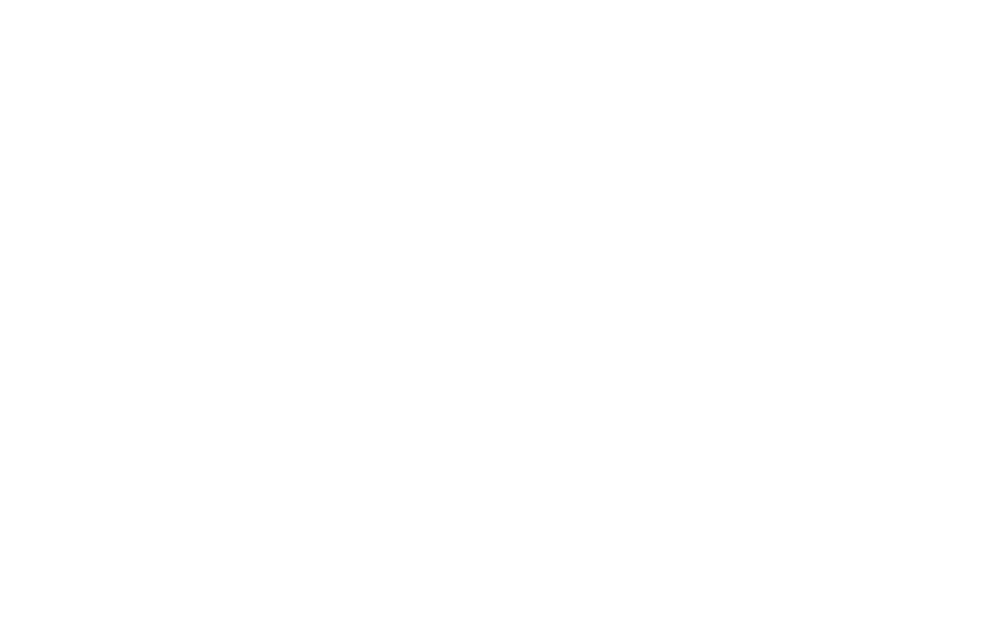
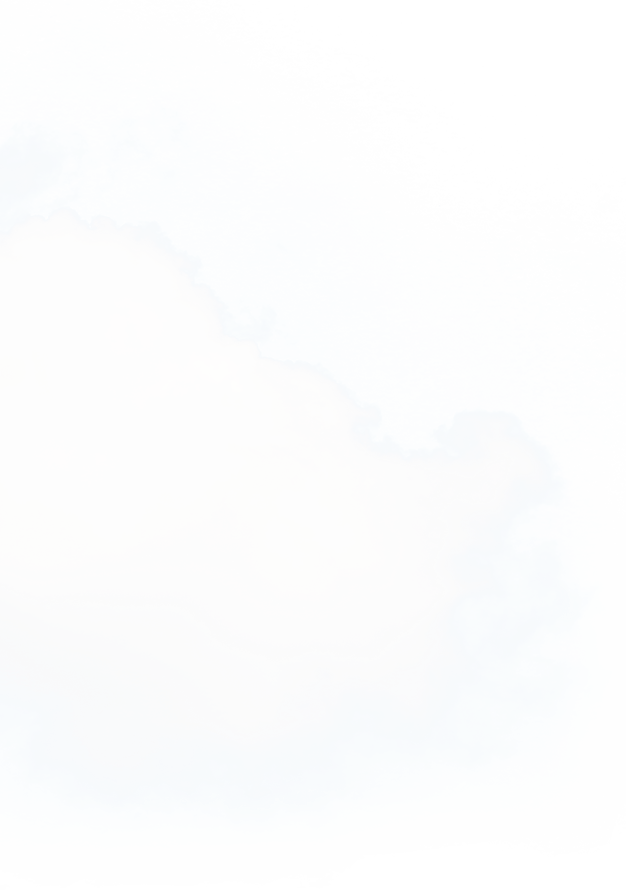
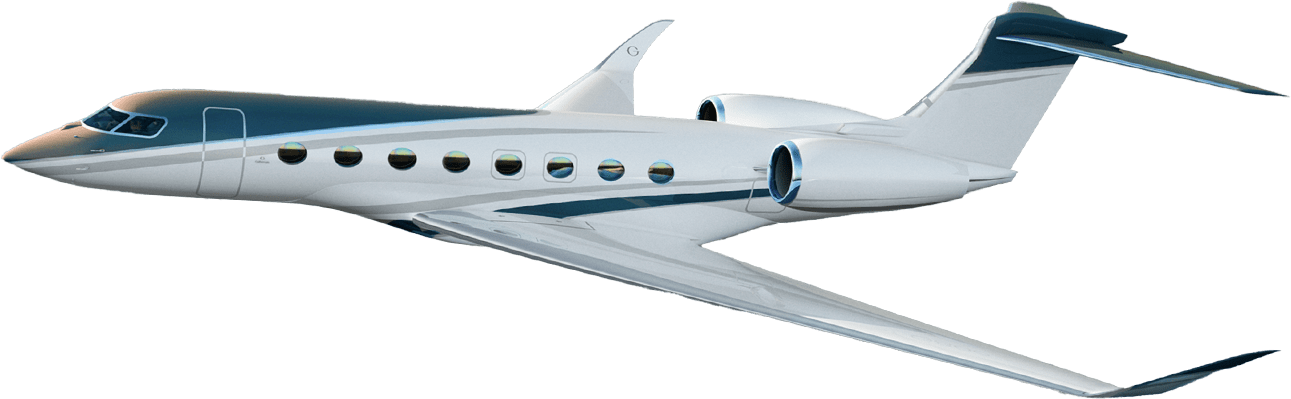
Business Jets
Are generally designed for faster air travel and more personal comfort than commercial aircraft. Efficiently designed and manufactured with traditional Aluminum metal, these aircraft require unique analysis methods to account for their thin sheet skins that are mechanically fastened to stringers.
HyperX has specialized analysis equations specifically for these airframes, many of which are based on NACA and early NASA research, such as incomplete diagonal tension buckling, complicated lateral-torsional buckling concurrently with skin postbuckling, and stressing the material past yield strength.
A common construction technique still used today is the Zee stiffened fastener panel. The HyperX design property form shown inthe image is taken from the published reference.
Verification and Refinement of an Aircraft Structural Design and Optimization Tool, ATLASS, Brenden A. Autry
Copyright © 2020. Published by the American Institute of Aeronautics and Astronautics, Inc., with permission.
34,000
Altitude: Feet
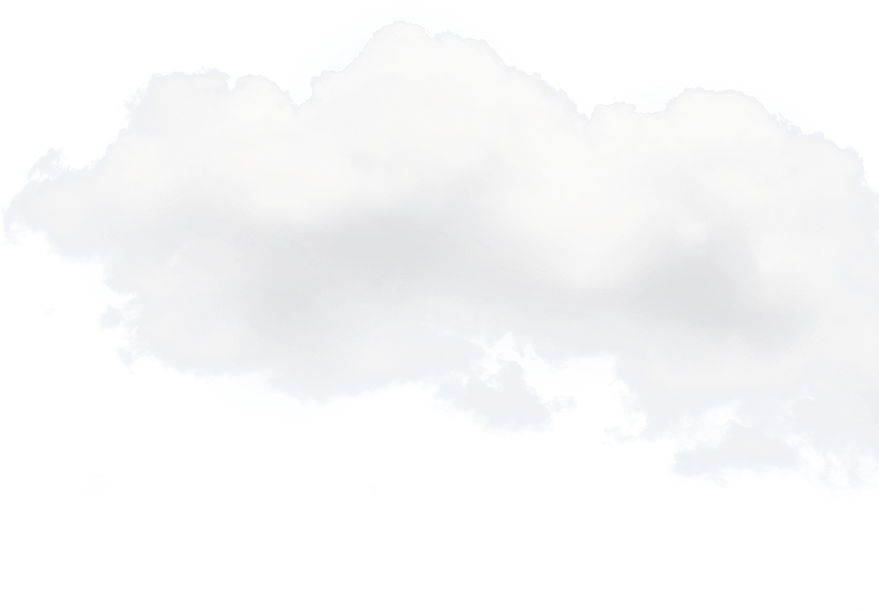
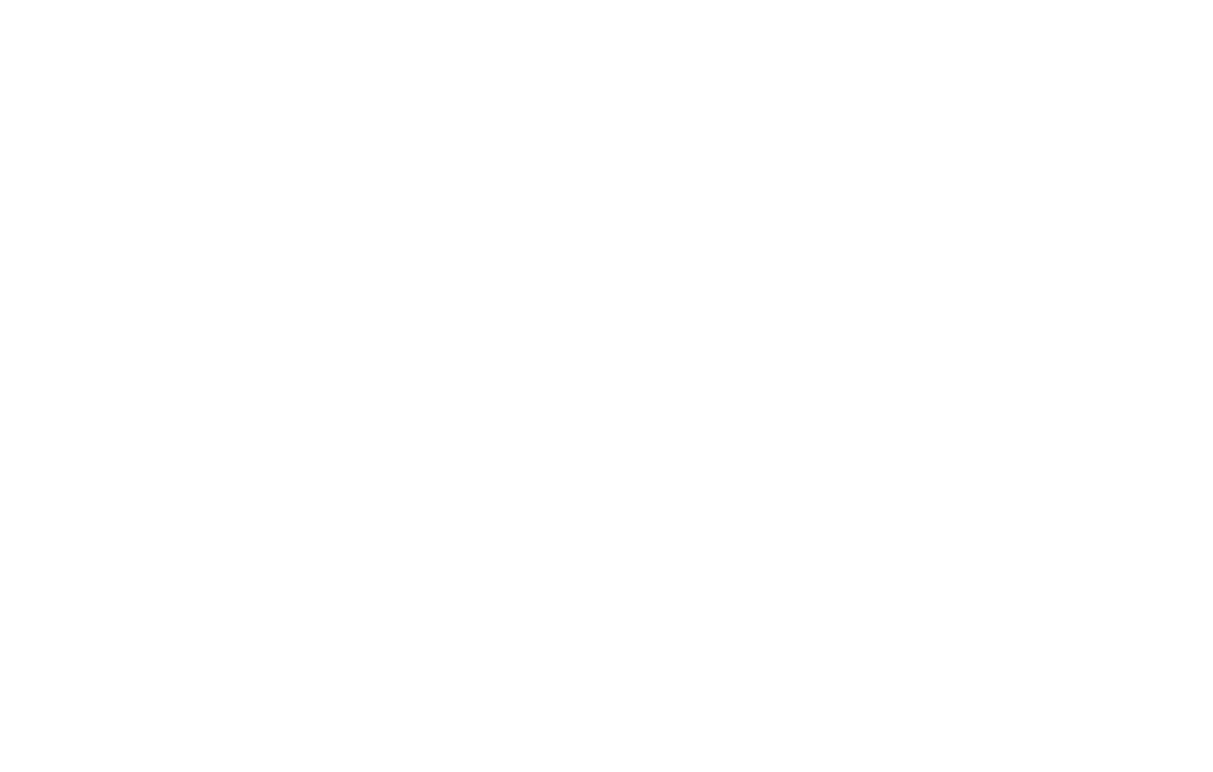
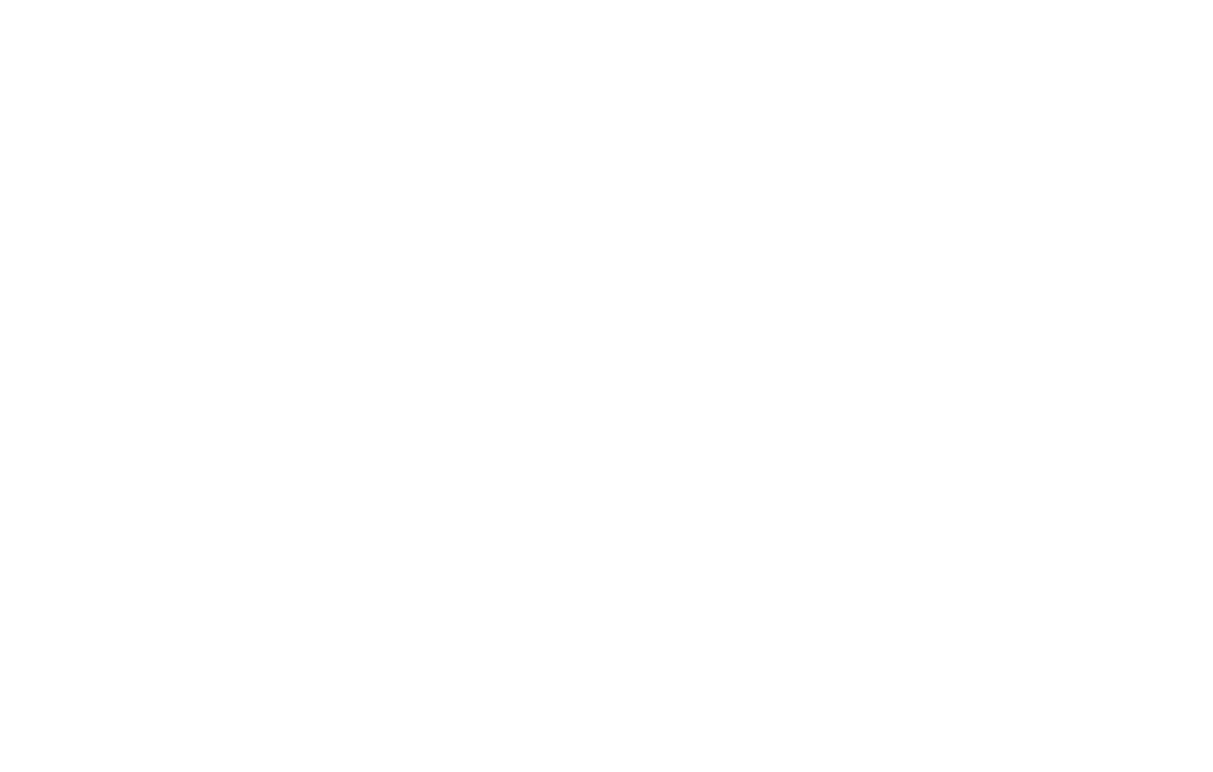
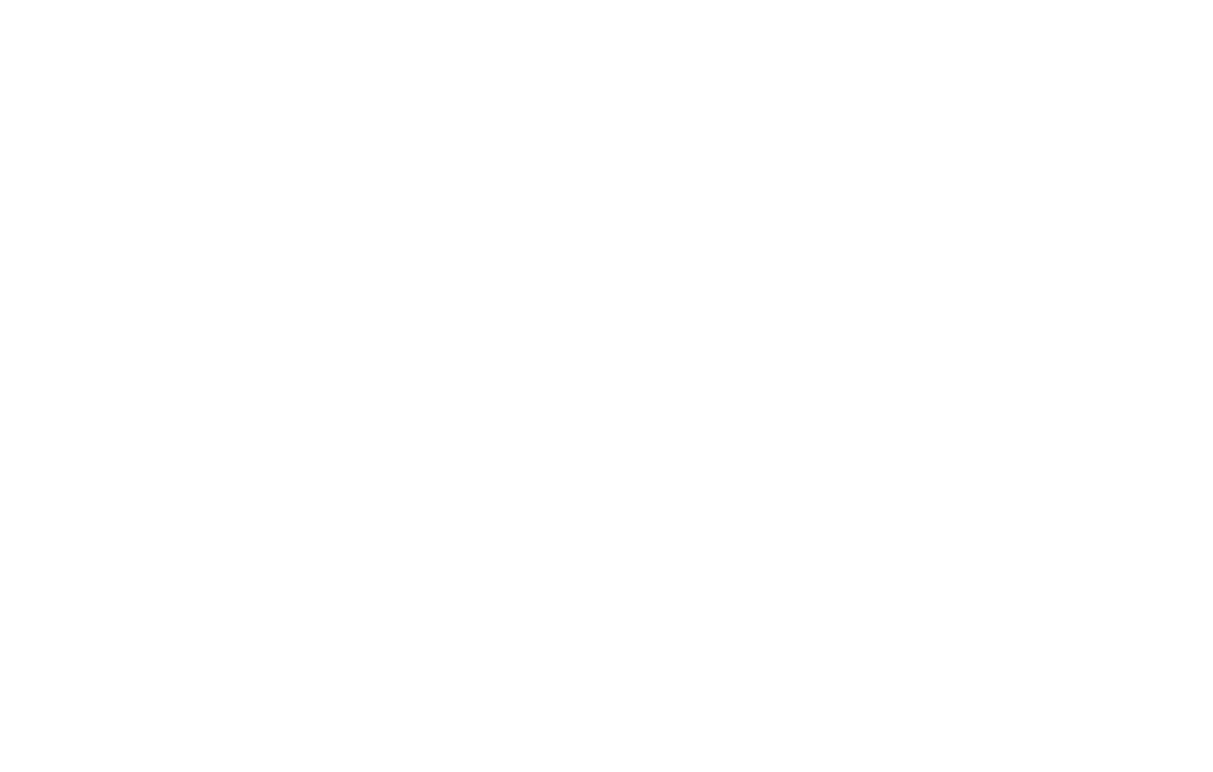
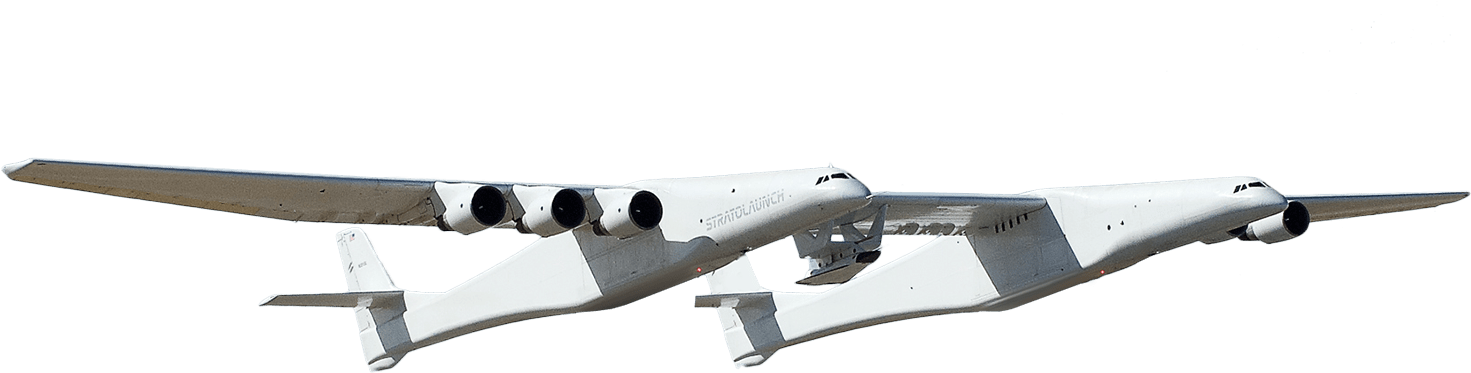
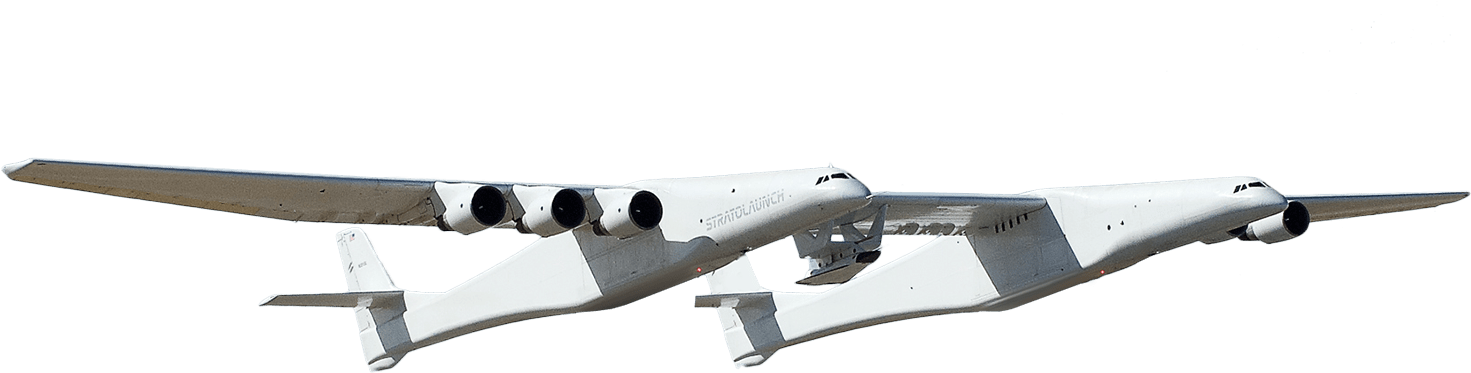
The Biggest Airplane in the World!
Scaled Composites Stratolaunch
Designed and built by Scaled Composites, Stratolaunch is the largest composite-structure aircraft ever made.
HyperSizer was used in design of the carbon-fiber structure of Stratolaunch’s 385-ft.-span airborne-launch mothership.
Aurora is currently designing the Virgin Galactic Dawn airframe for the next generation airborne-launch mothership. HyperX is heavily being used on this project.
34,000
Altitude: Feet
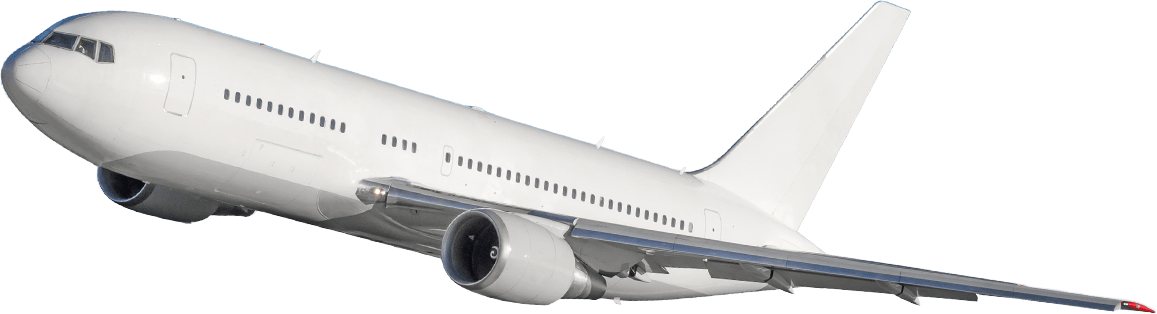
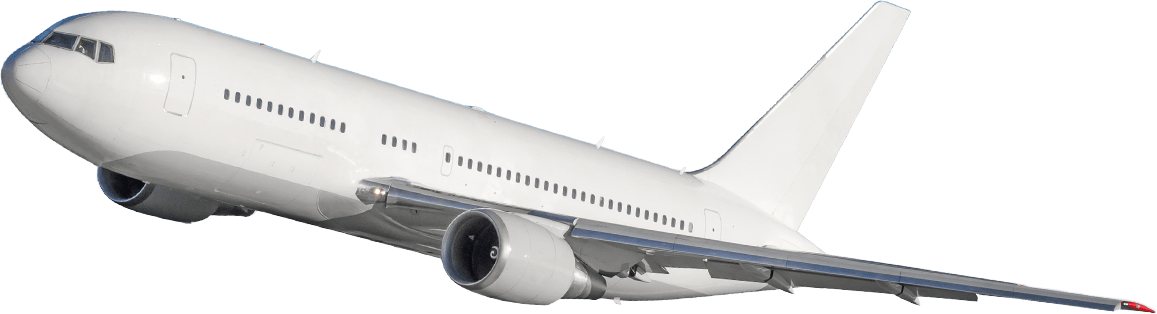
Commercial Aircraft
NASA’s previous Advanced Composites Program (ACP) and the current High Speed Composites Manufacturing Program (HiCAM) are both intended to bolster the commercial airframe industry in America.
Research with industry partners include Boeing, Spirit Aero, Collins Aerospace, Lockheed, Northrop Grumman, NIAR, FAA and our company Collier Research. The total investment for both research programs totals $493 Million.
The ACP’s purpose to reduce time to certify composite structures, and the HiCAM’s purpose to enable high-rate production of up to 80 aircraft per month.
Our company provides the HyperX software airframe stress analysis and sizing software to the industry team members to quantify Weight Key Performance parameters (KPPs) for wing and fuselage structures with three material systems:
- Next generation thermosets
- Thermoplastic
- Resin Infusion
In addition to native HyperX analysis methods the software serves as a stress framework to plugin commercial aircraft OEM proprietary methods such as the large damage, two bay crack analysis.
Our company performs research and development for design for Manufacturing (DFM) with Automated Fiber Placement (AFP) fiber paths, avoiding defects such as laps and gaps.
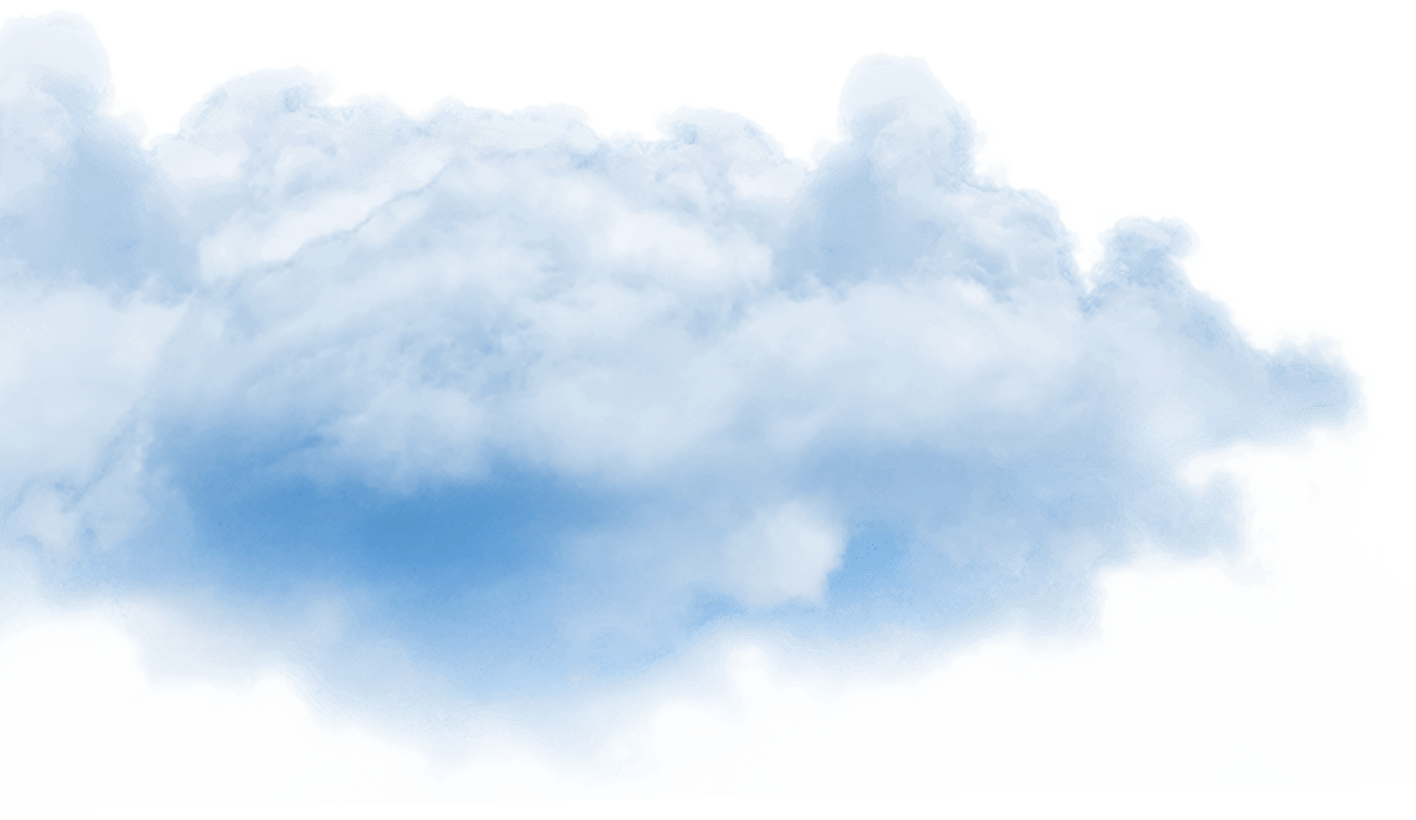
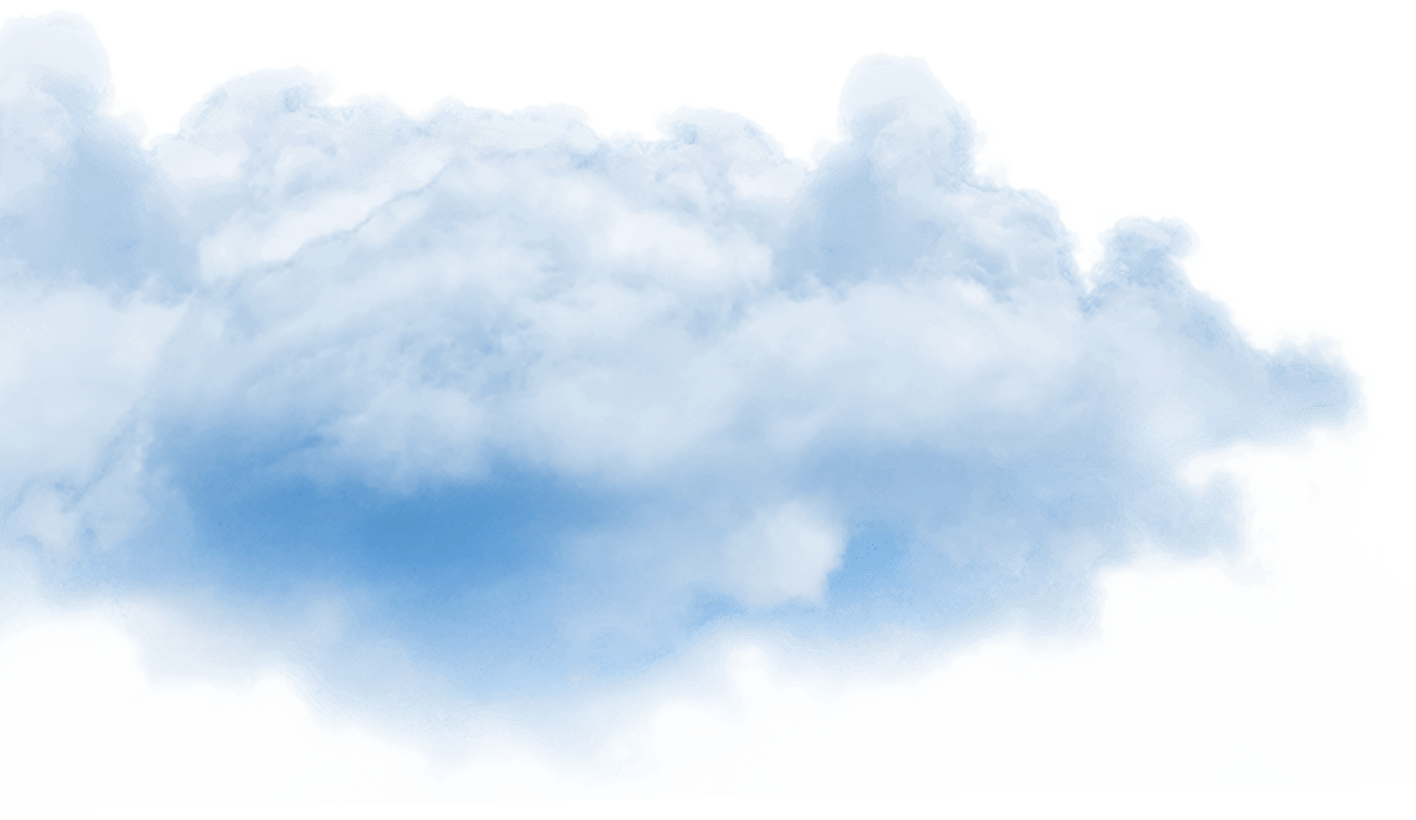
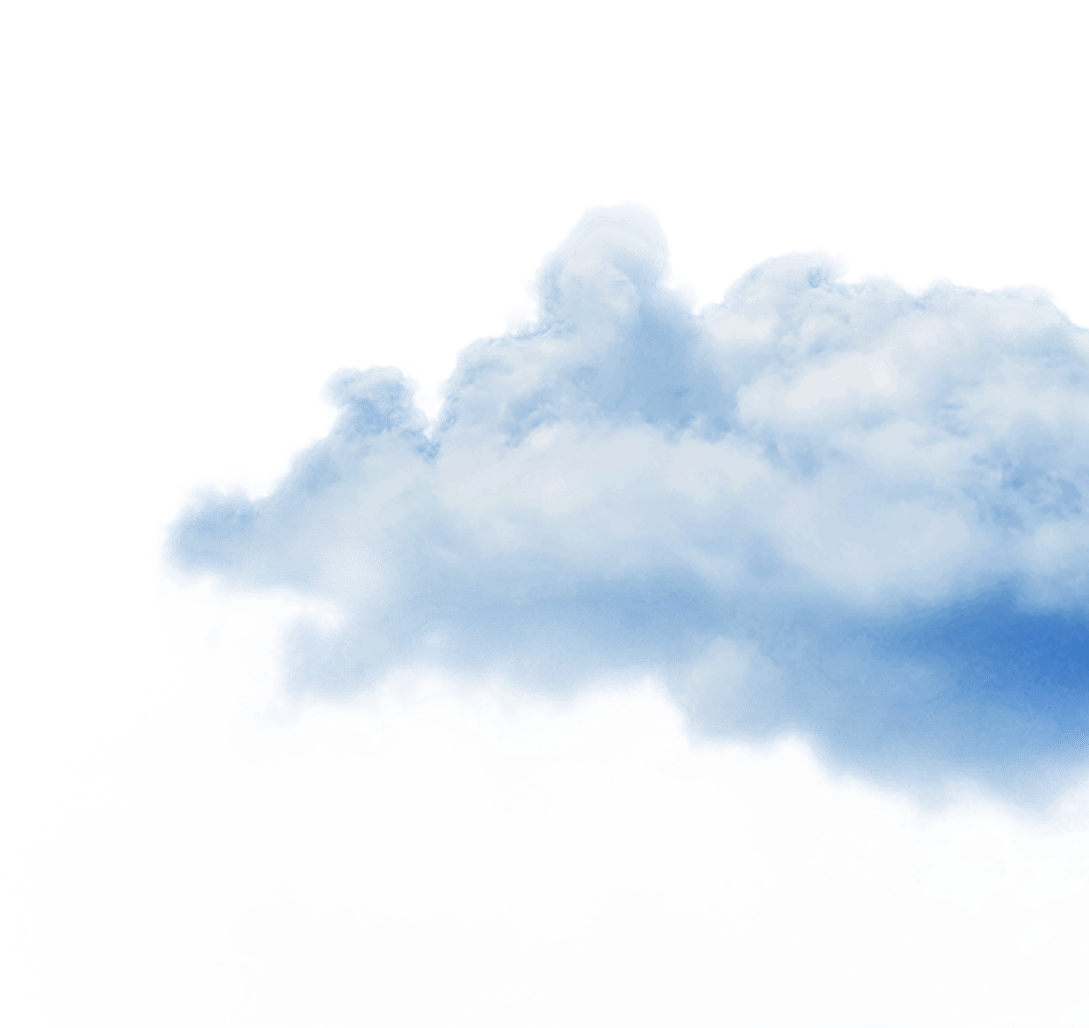
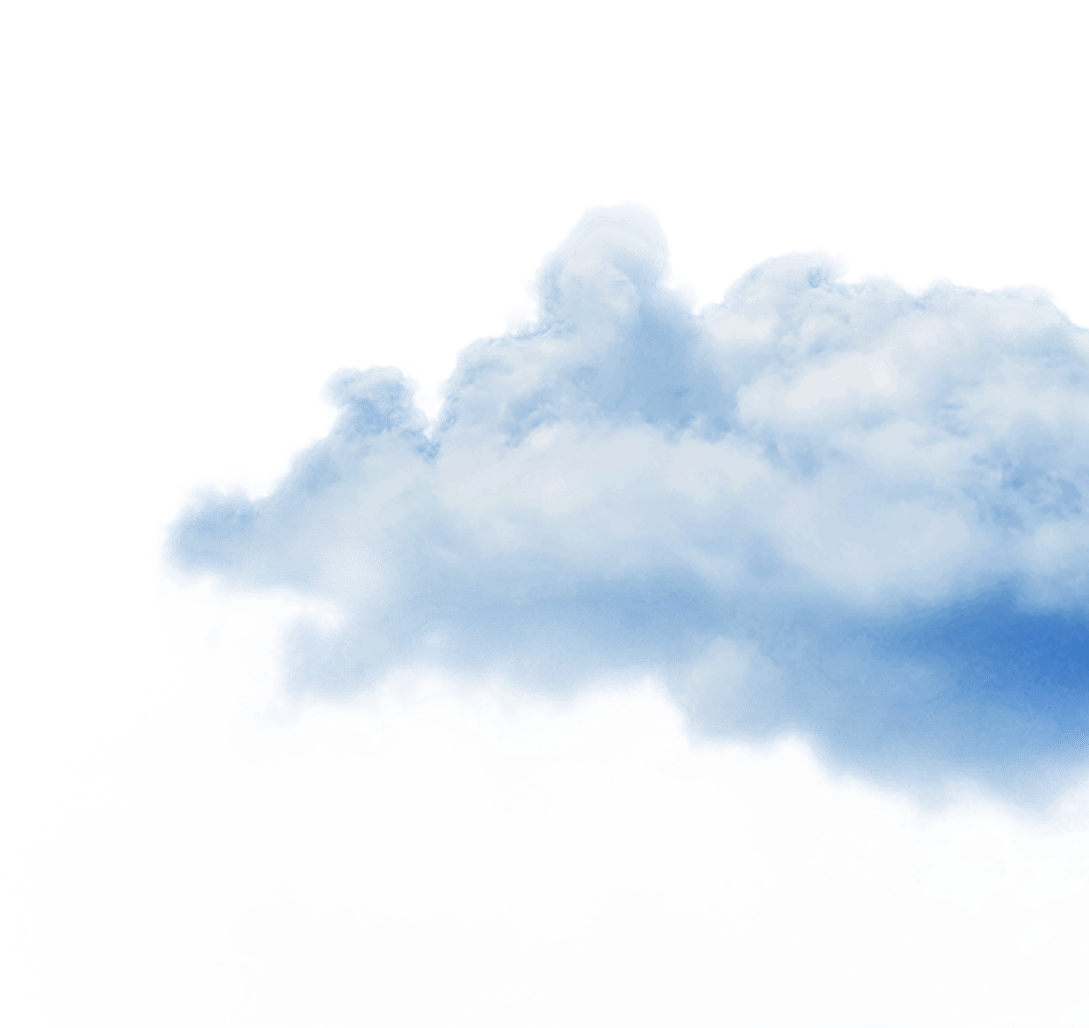
1500
Altitude: Feet
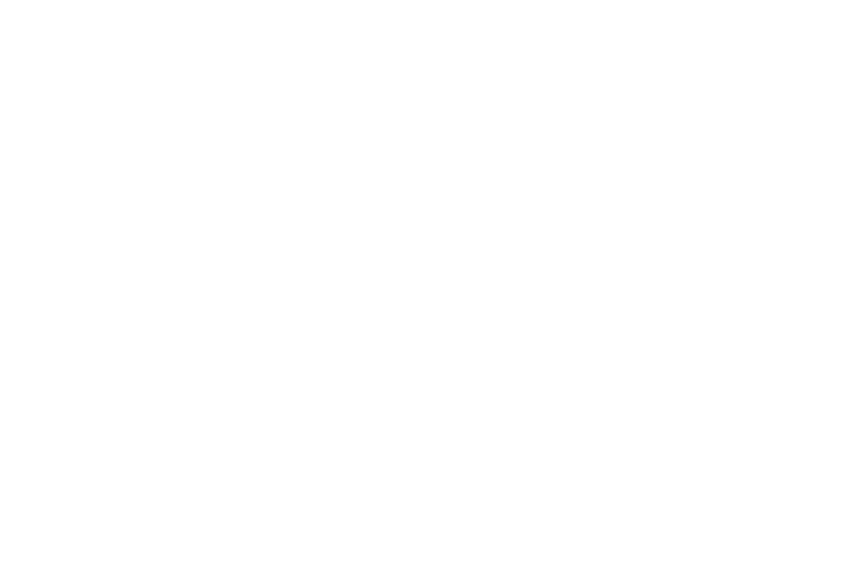
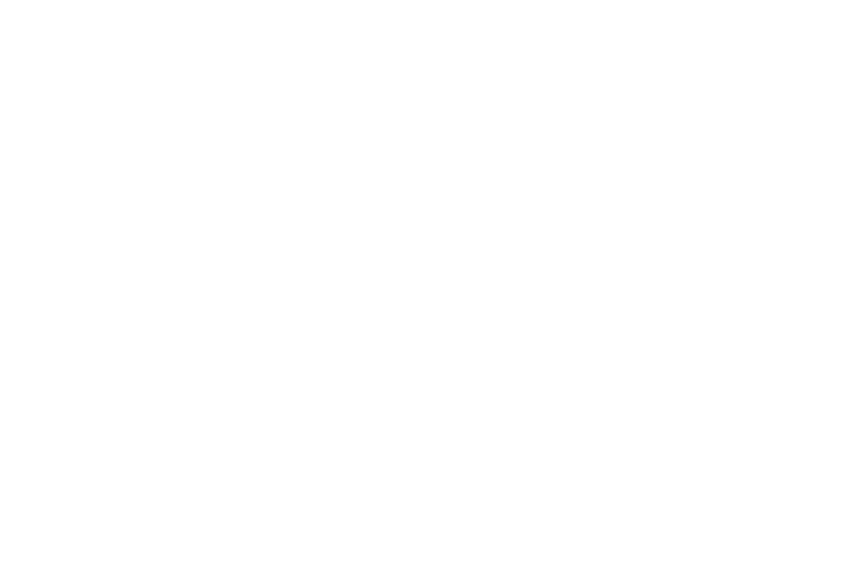
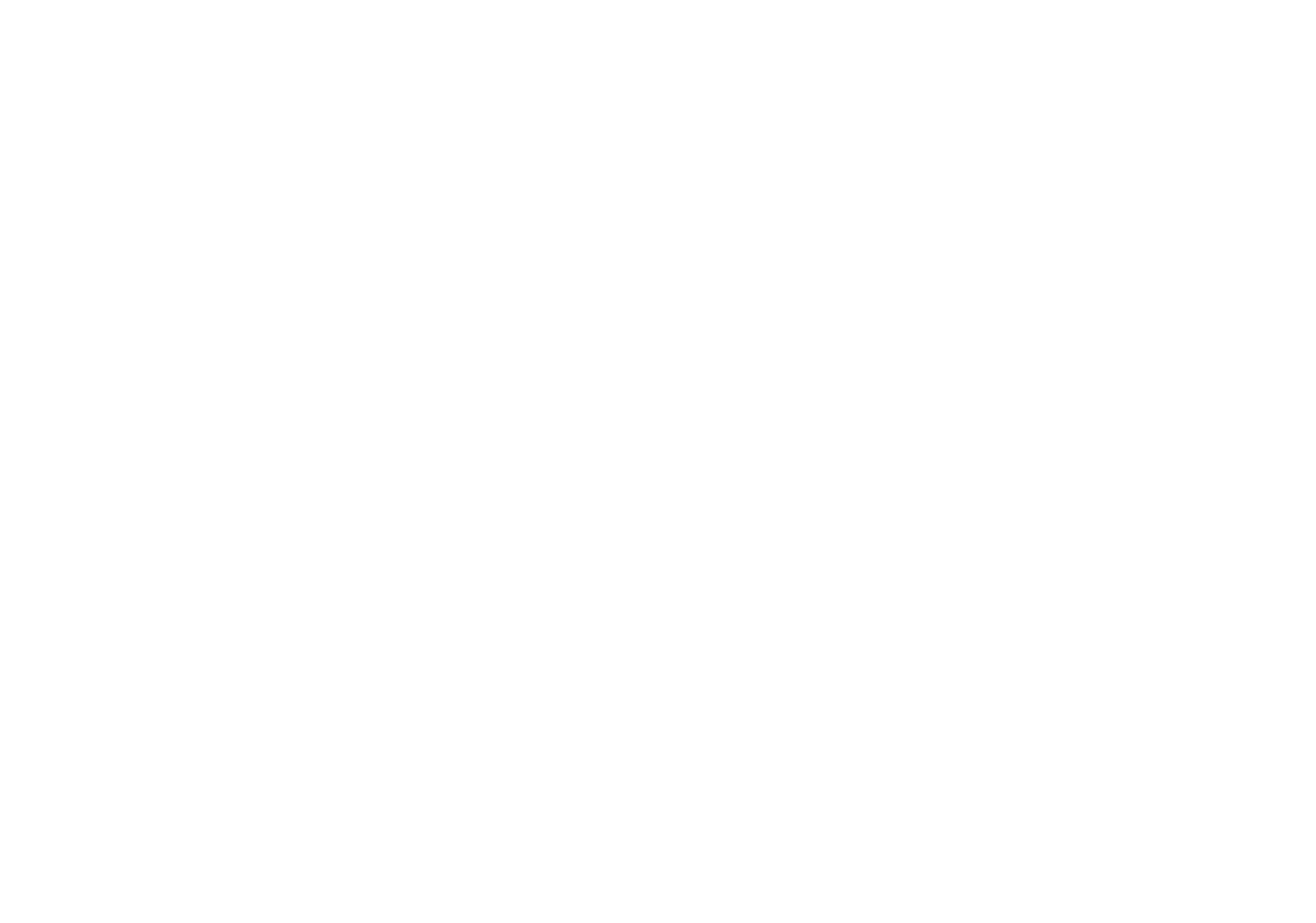
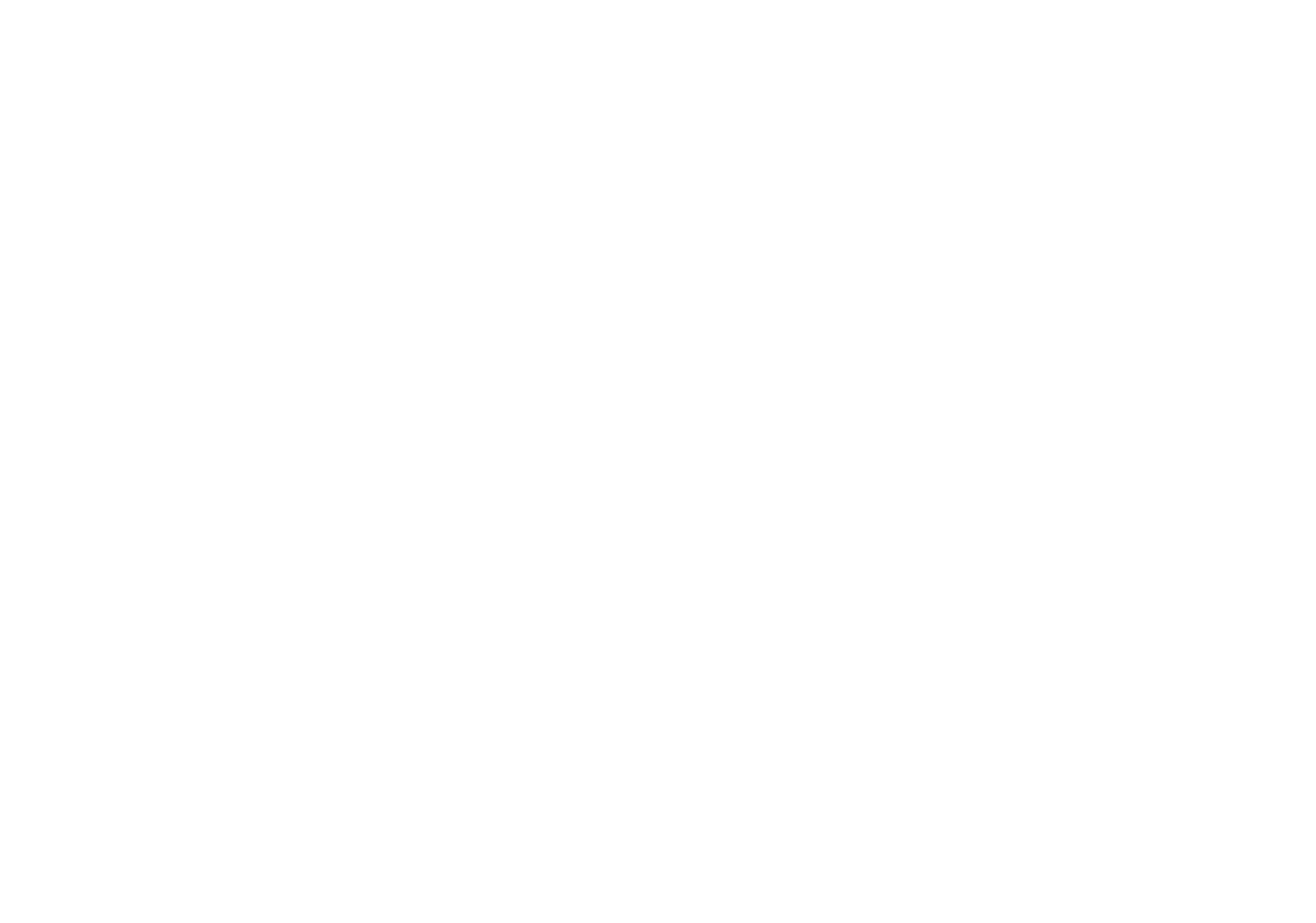
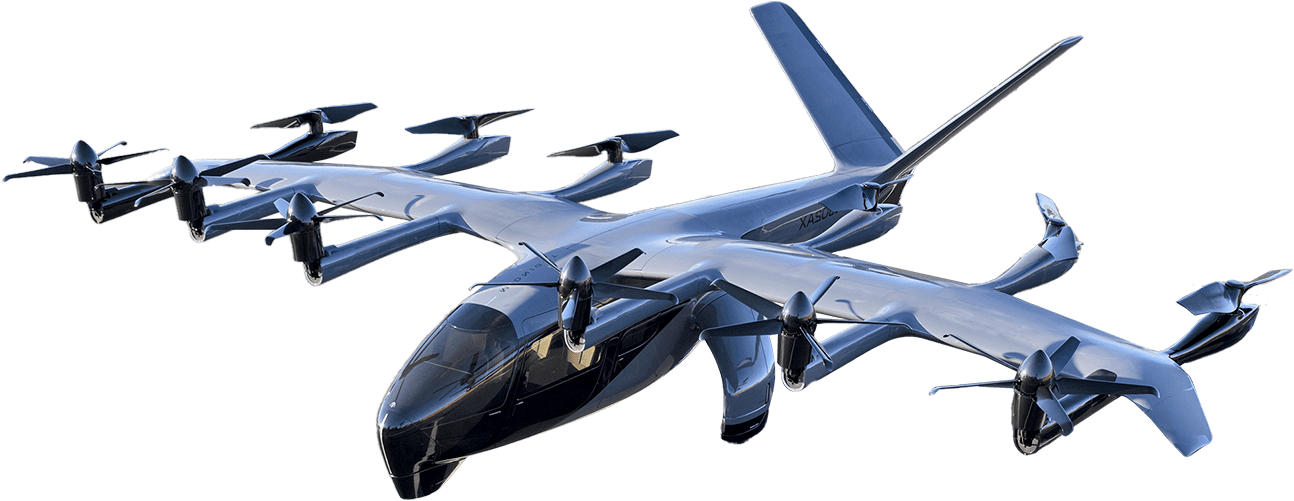
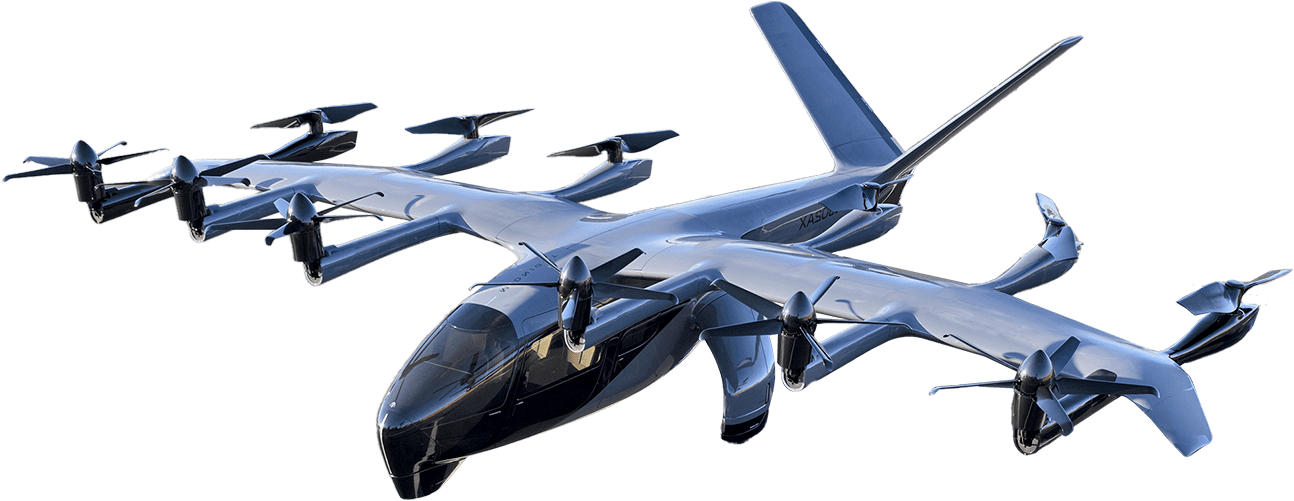
UAM eVTOL Aircraft
Urban/Advanced Air Mobility (UAM/AAM) Electric Vertical Take-Off and Landing (eVTOL) are aircraft that can hover in-place for take-off and landing, but transition to wing-born flight for forward cruise. Most designs are battery powered, and with the weight of the battery make their designs very challenging to meet Empty Weight Fraction requirements. Engineering teams need to explore the design space completely and rapidly to achieve necessary lightweighting. Additional challenges that companies in this competitive market are meeting with HyperX include:
Schedule: 4 years to Entry-into-Service (average for General Aviation is 7 years)
Producibility: Rate & Cost: 10,000 aircraft per year by 2030 (highest General Aviation volume is 2200/yr)
Certification: Design-Analysis Cycle (DAC) must be fast, accurate, and provide excellent traceability
1000
Altitude: Feet
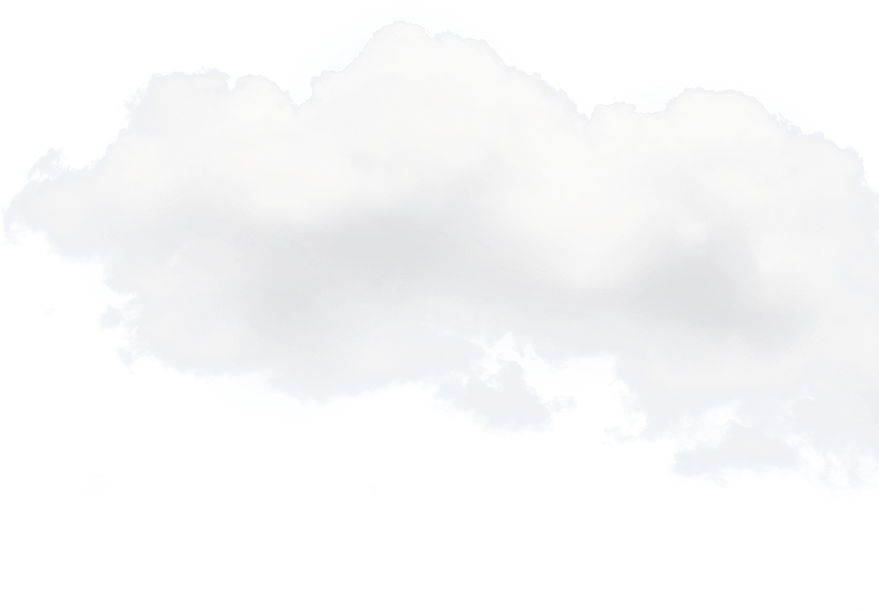
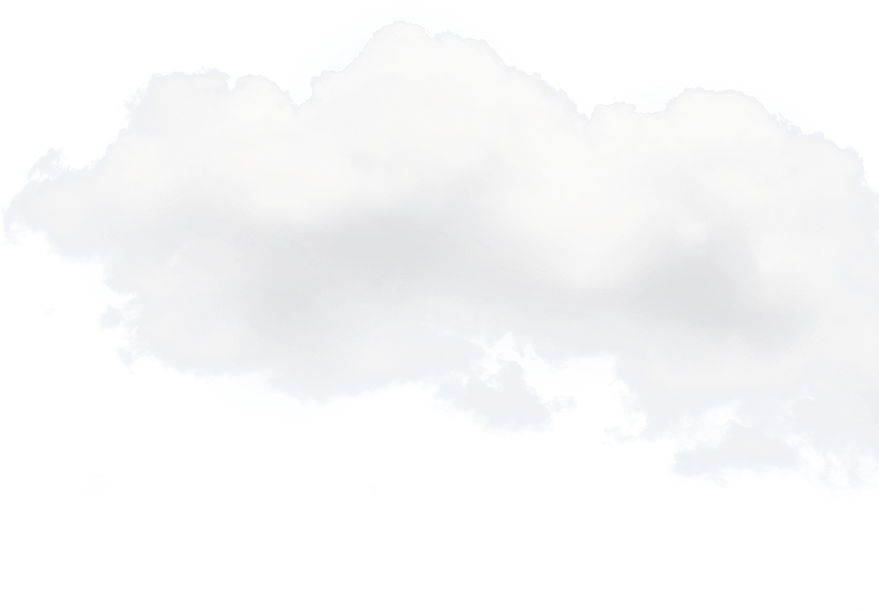
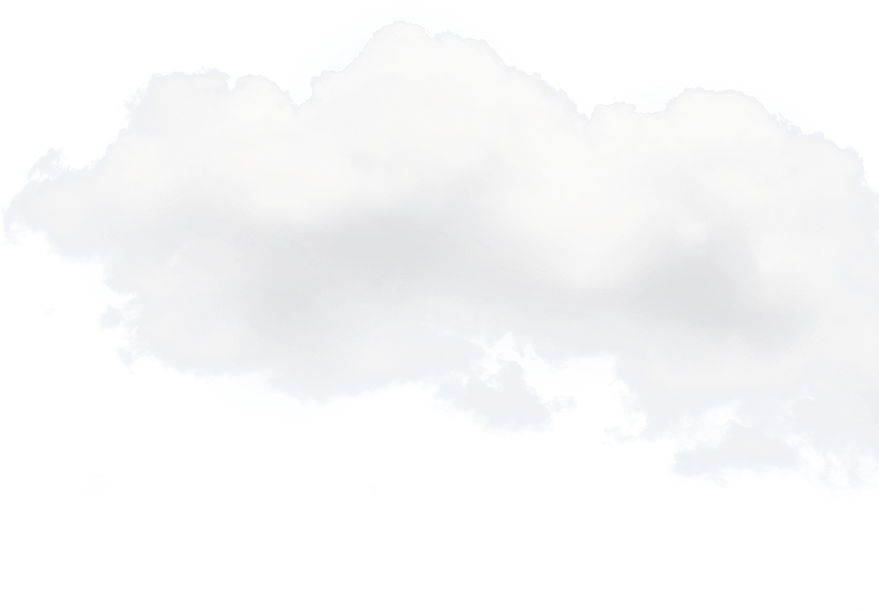
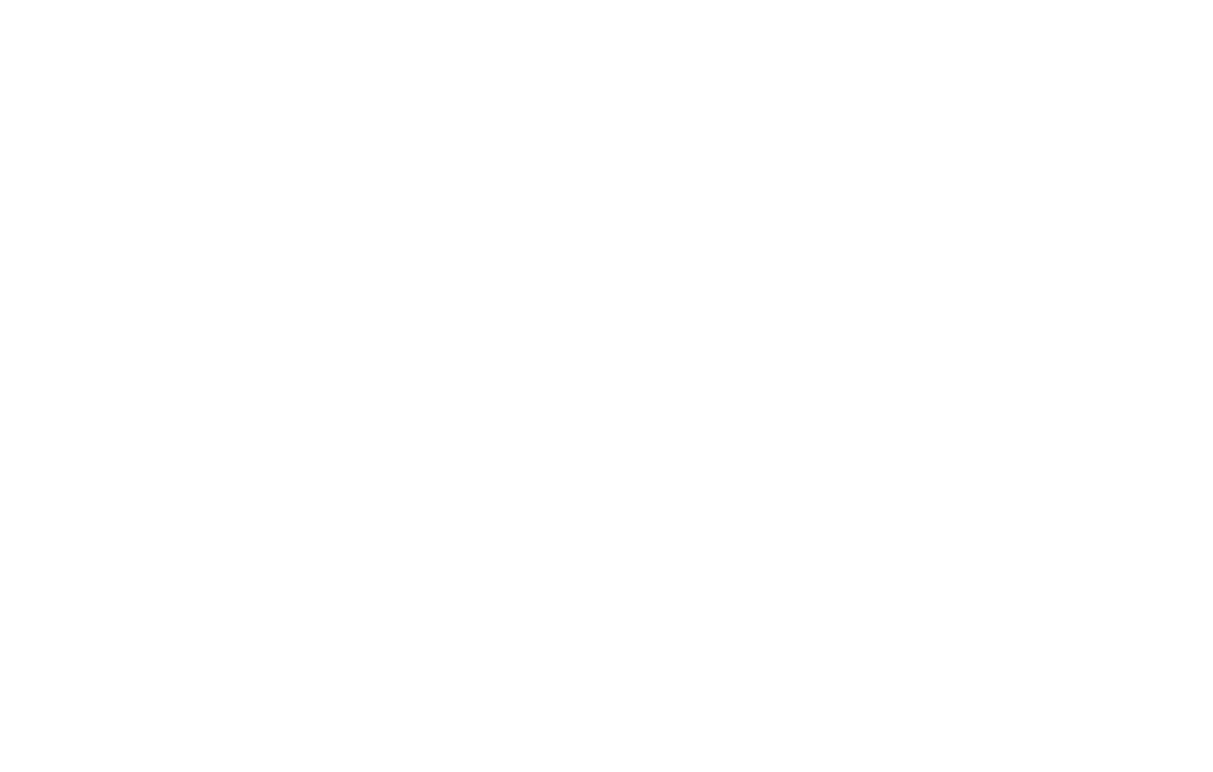
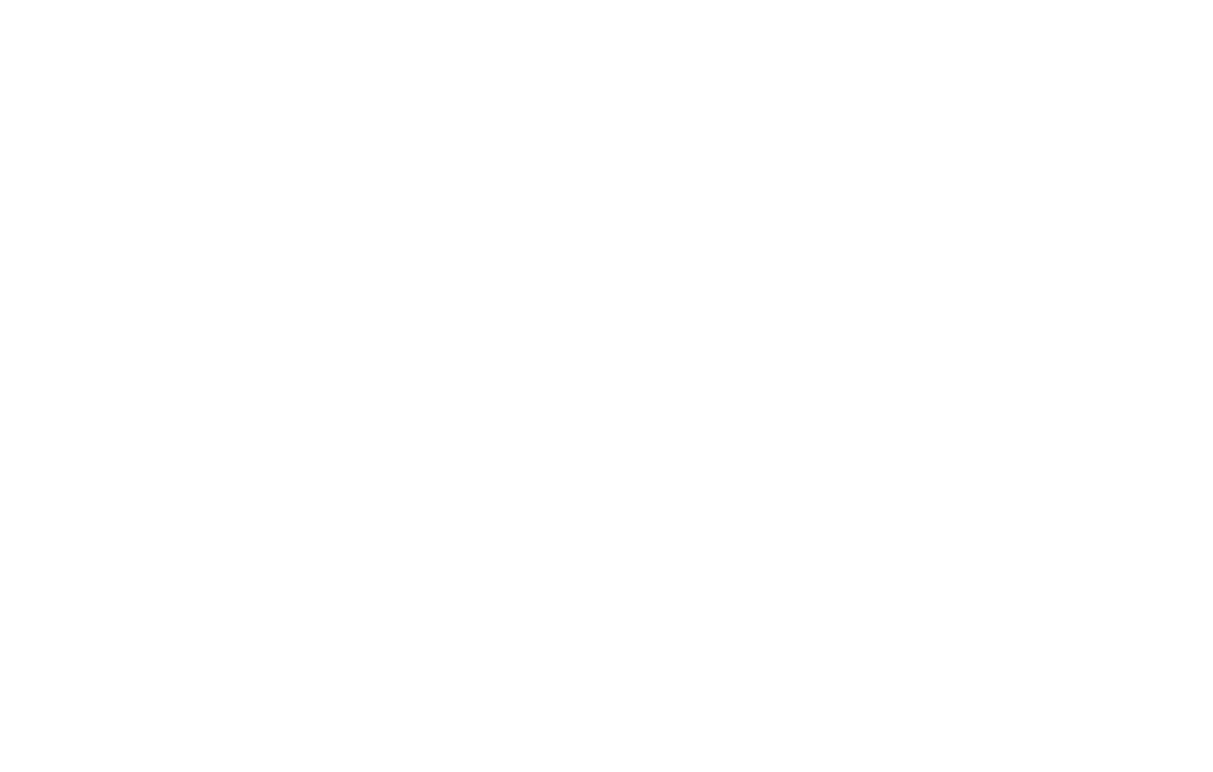
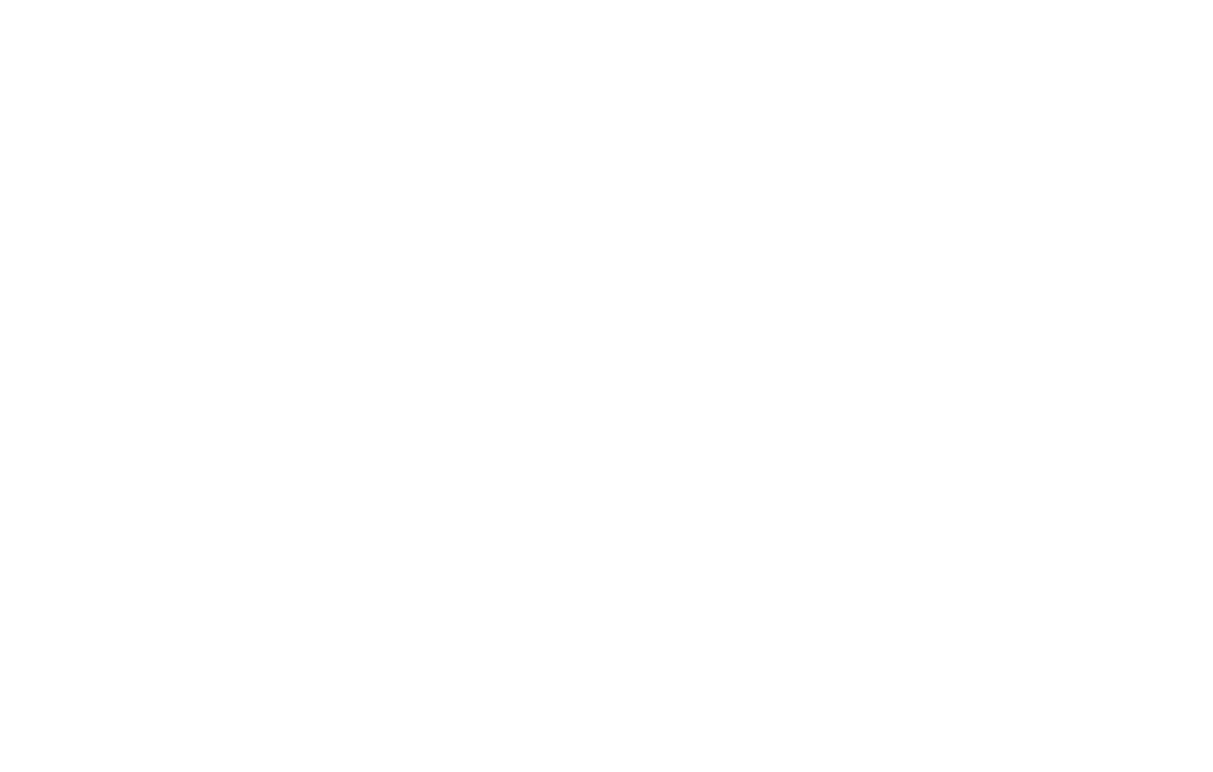
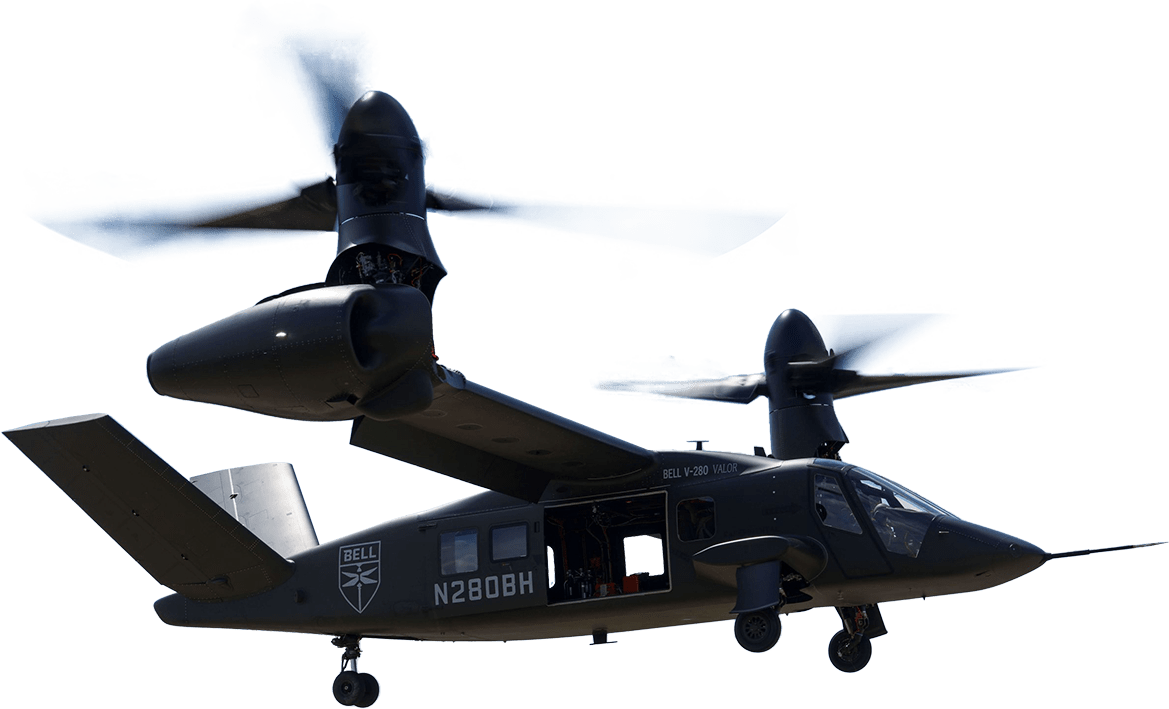
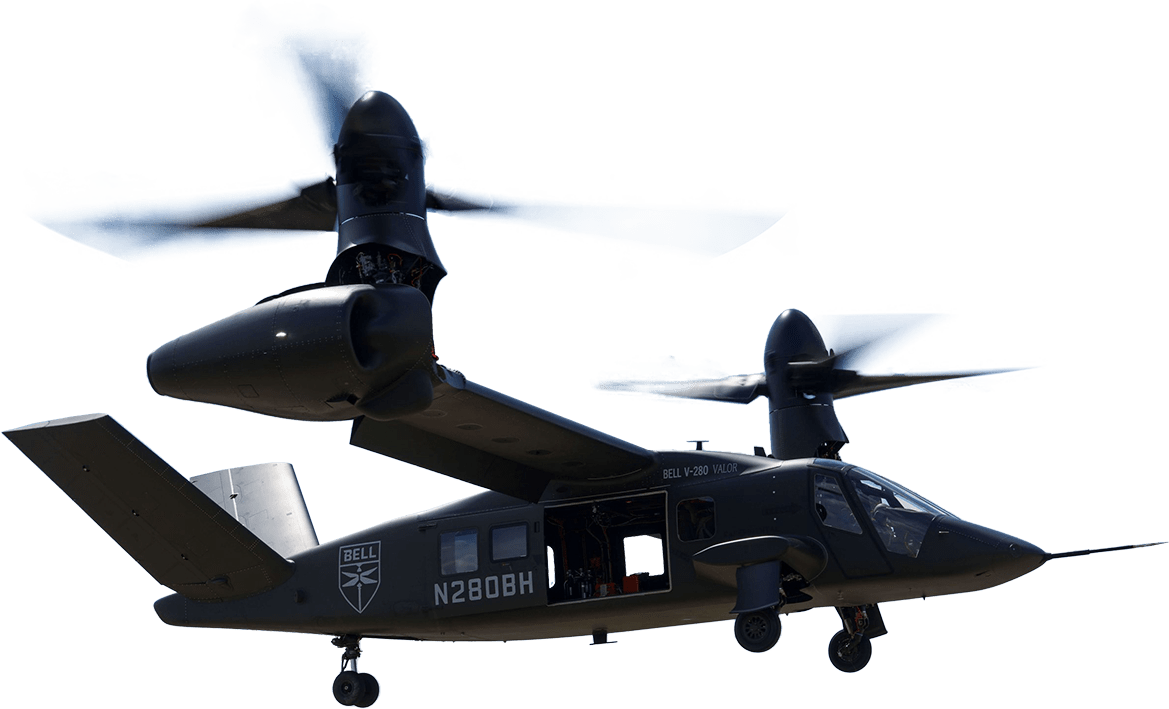
V280 Military Tilt Rotor Aircraft
In 2023, the Army is contracting with Bell to provide V-280 tiltrotors to replace much the Sikorsky H-60. V-280’s cruise speed is more than 280 kt with a combat range of 500 nm
In 2015, for the V-280 prototype program, Spirit AeroSystems designed and fabricated the fuselage ahead of schedule and within budget. To get their Spirit used HyperSizer for detailed sizing of the fuselage to structural requirements including strength, stability, stiffness and deflection/rotation limitations for severe flight, landing and ground load cases.
Collier Aerospace is looking forward to working with both Bell Aviation and Spirit AeroSystems as the V280 design continues through production.
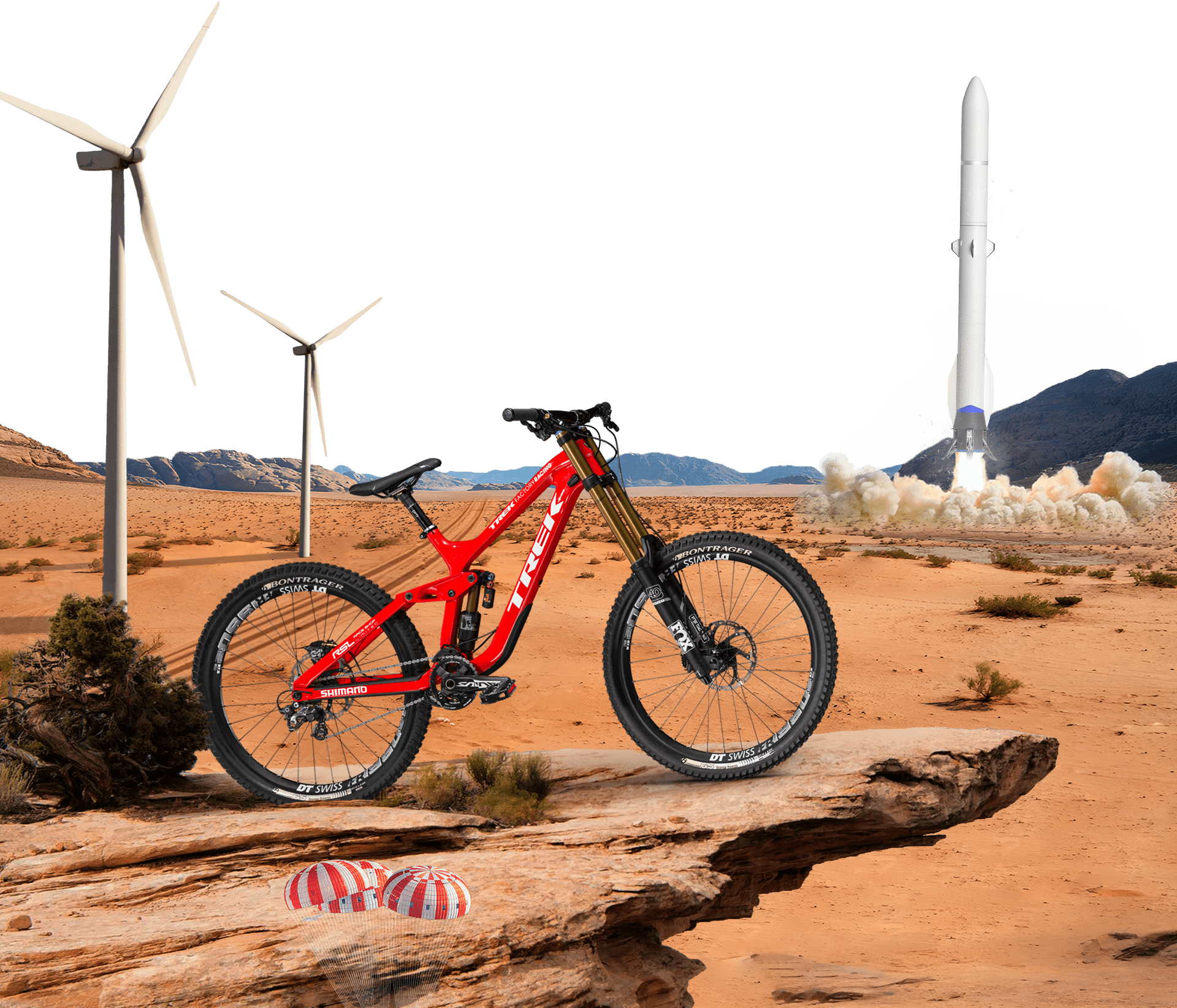
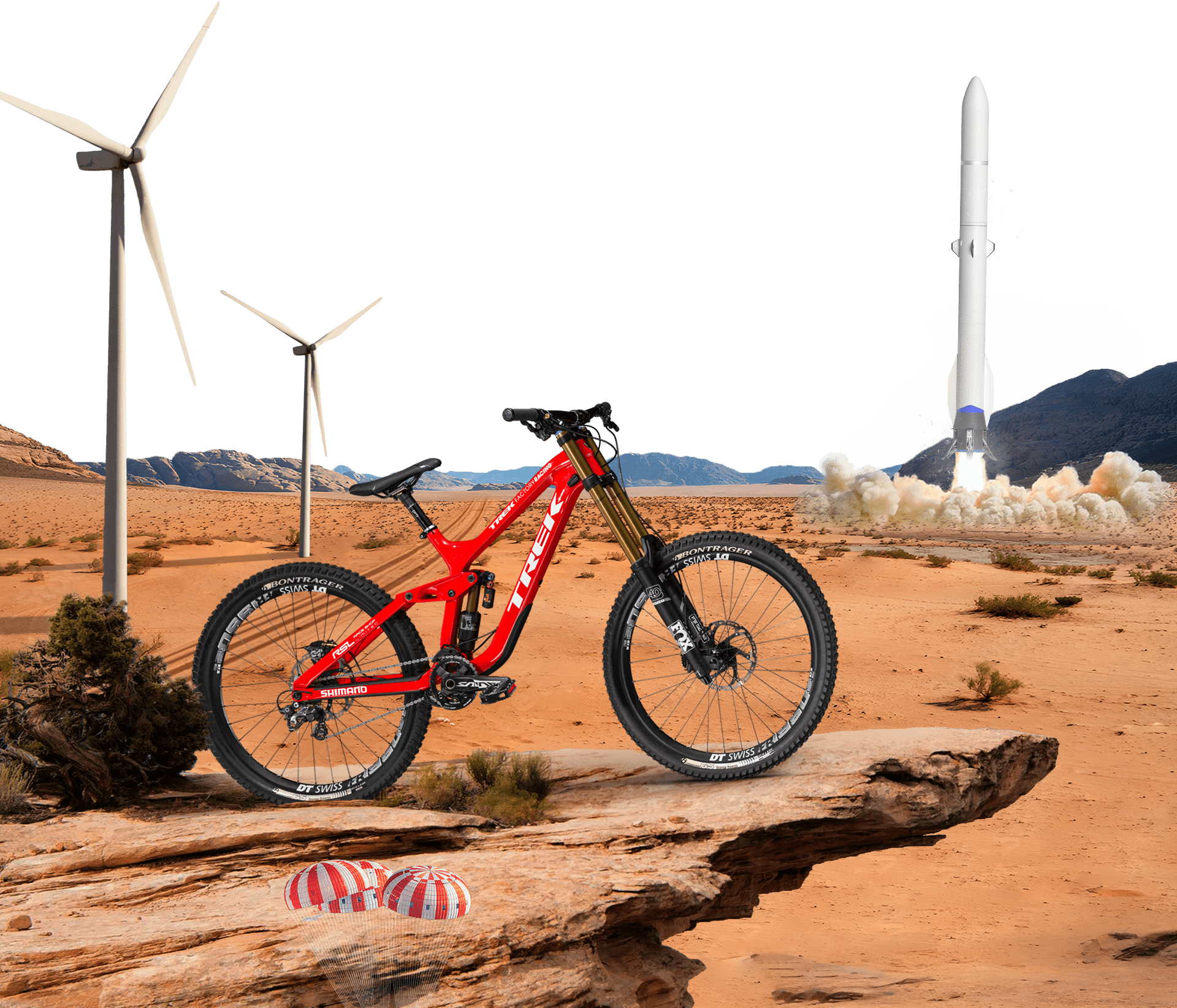
Trek Bike
Uses HyperX for designing high performance road and mountain composite bikes.
Adoption started with a straight handle bar and then moved to a challenging road bike (Madone) handlebar. Now Trek is applying HyperX to a frame.
There is much detail to ply shaping, sequencing, and stacking to achieve optimized material performance for the doubly curved surfaces at areas such as the bottom bracket.
Competitive sports require high performance but also speedy time to market and quick producibility. Trek is realizing all three enabled with HyperX’s capability to light weight, reduce schedule, and improve producibility.
Wind Blades
HyperX has been used for design and analysis of wind blades for over a decade for laminate stacking sequences, ply boundaries and layup stacking order.
1st published by NASA Tech Briefs in 2010 and most recently in 2022, as according to Professor Yeonseung (Y.S.) of the Hongik University in South Korea , “HyperX software made an incredible difference in the design and development of the wind turbine blades …since the software optimizes all requirements at once rather than one at a time.”
HyperX is used by industry to design wind blades from 30m to offshore 100m length designs. Professor’s Lee’s application was a 7.4-meter natural fiber composite blade.
Reusable Launch Vehicles
There is a lot of structure inside of rockets (see image) that are highly loaded and require detailed sizing and analysis.
HyperX has a long history of use by both government and industry for design and analysis of launch vehicle structure.
NASA uses our software on all of their rocket designs going back to Ares 1, Ares 5, and SLS.
Industry such as Blue Origin (New Glenn rocket) uses HyperX and our Collier engineering team on nearly every piece of structure:
Fuel tanks with and without internal frames and stiffeners, Pressure domes, Interstages and intertanks, Fins and strakes, Dry structure and thrust structure, Fairings/shrouds, etc. for composite sandwich and machined metal orthogrid stiffened panels.
HyperX is used for weight reduction sizing from early PDR to CDR, and analysis and margin stress reporting through drawing part release.
Rockets have large FEMs with element count in the millions, and reusable hardware that reenters earth atmosphere have hundreds of thermomechanical external loadings, all of which HyperX efficiently handles.
Ground Level
Altitude
Ground Level
Altitude
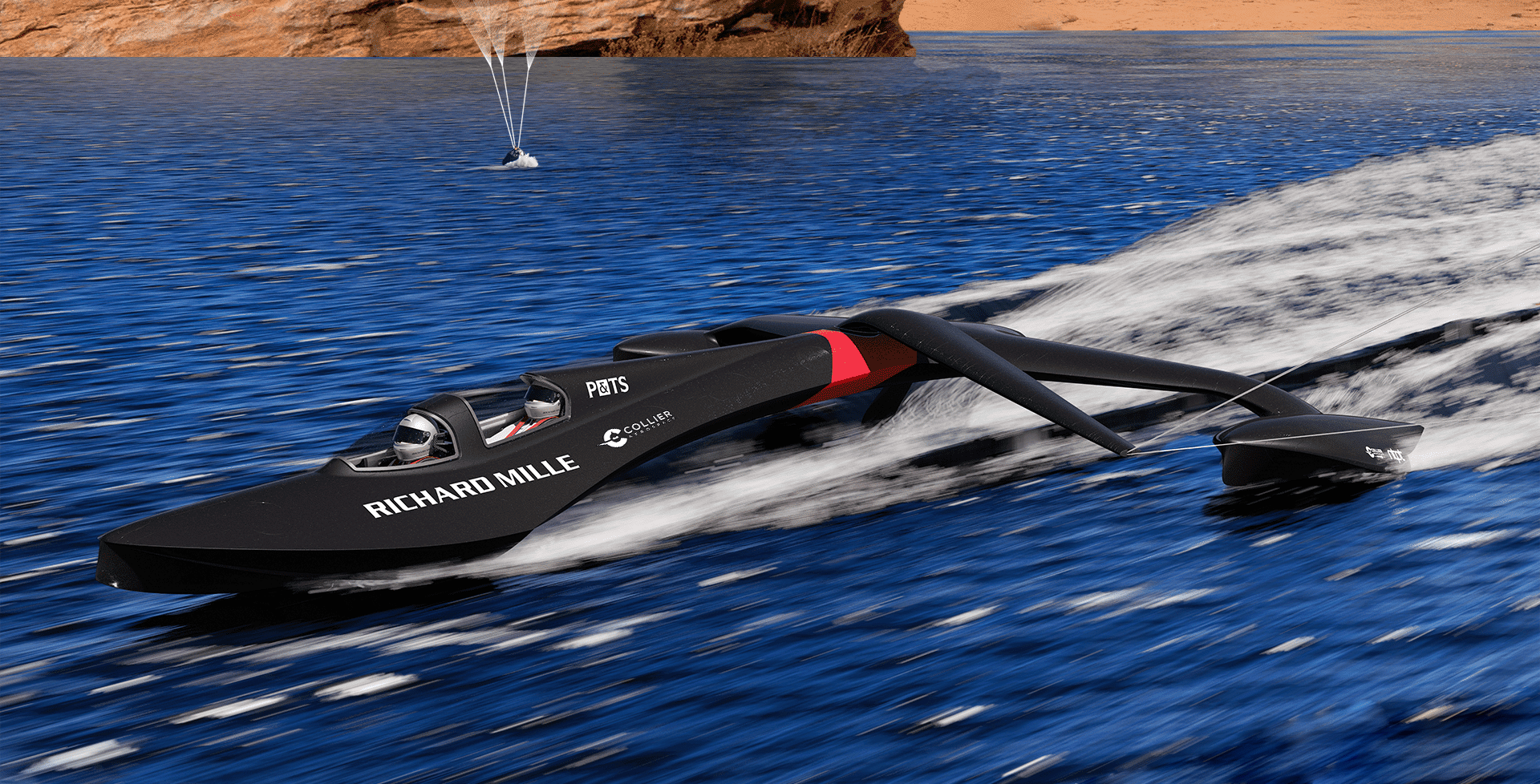
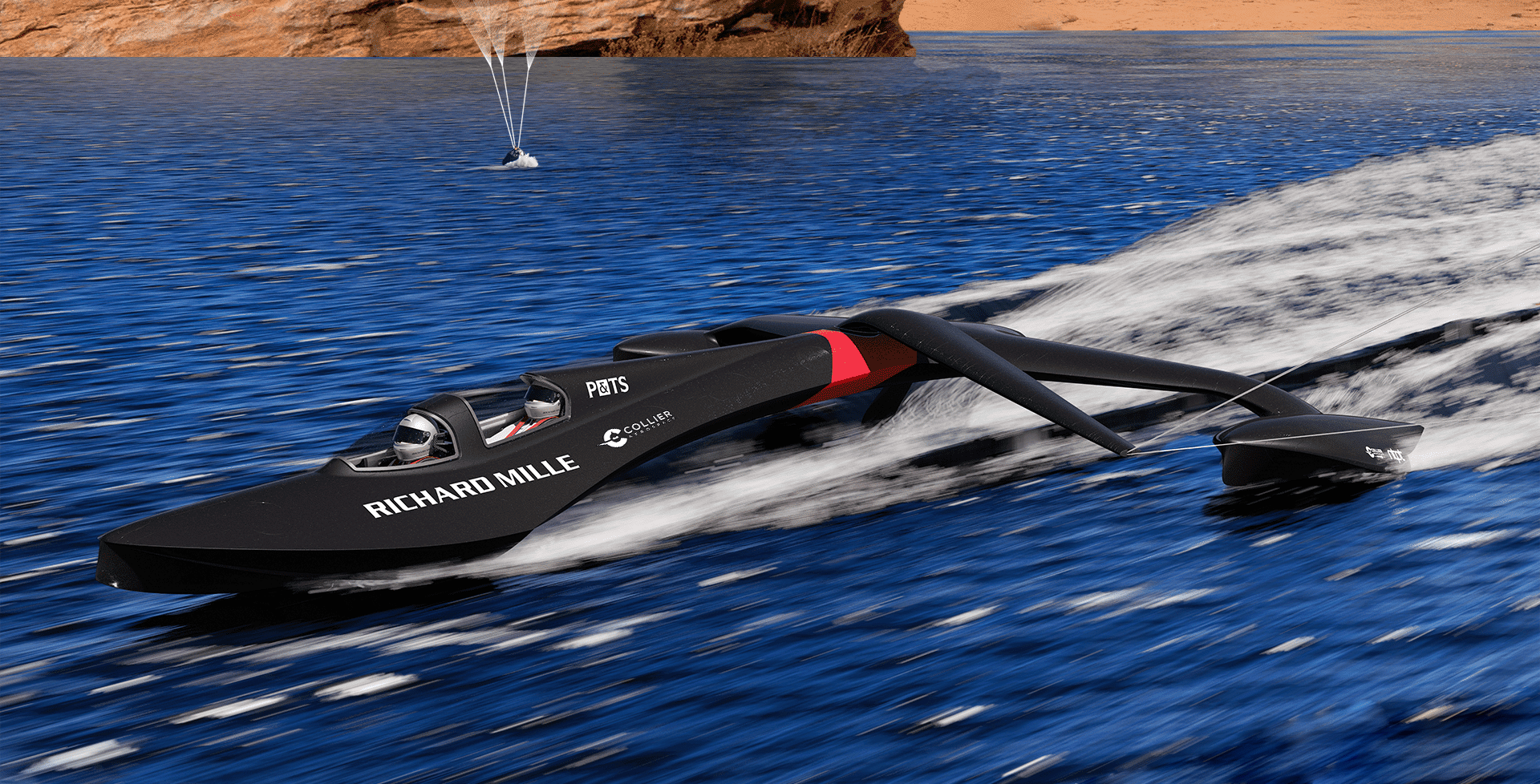
NASA Composite Crew Module
Water “splash down” impact loading is a driving load case on the bottom of the crew module while parachute loads are on the top. Many other load cases drive the design of these space capsules including abort, and trans lunar insertion.
Seen from outside is the familiar looking aeroshell. Inside the aeroshell is the pressure vessel that protects the astronauts. The composite design uses sandwich panel and solid laminates throughout with bolted and adhesively bonded joints.
A full scale test article was fabricated and successfully loaded to failure, which occurred above the damage tolerate ultimate design loads.
HyperSizer was used for architectural trade studies, ply by ply sizing optimization, and pre-test strain predictions to correlate with strain measurements.
The World’s Fastest Sailboat!
The SP80 Composite Sailboat
team is attempting a world sailing speed record by developing a kite-powered boat capable of reaching 80 knots.
Collier Aerospace is an official partner responsible for:
- -Performing trade studies using numerous sandwich core materials
- -Optimizing the all-composite structure for minimum weight
- -Producing an “optimized for producibility” fabrication ply sequence using unique thin-ply carbon fiber tape manufacturing requirements
- -Determining inadequate structural design concepts, guide the necessary changes, and quickly size/optimize the newly generated structures