When do you use HyperX Software?
HyperX provides project phase, specific workflows for individual analysts and teams to mature their structure from a conceptual design all the way to part release. It provides a seamless process for performing sizing optimization using the same detailed analyses for conceptual design review (CDR), as it does for the preliminary design review (PDR), all the way to final design and part release certification.
Use HyperSizer to standardize your company’s analysis with its native verified and validated analysis methods, or with your plugged in methods. Since the same analysis methods are used from preliminary to final design, there are no surprise negative margins of safety that would detrimentally affect your schedule or cause weight growth.
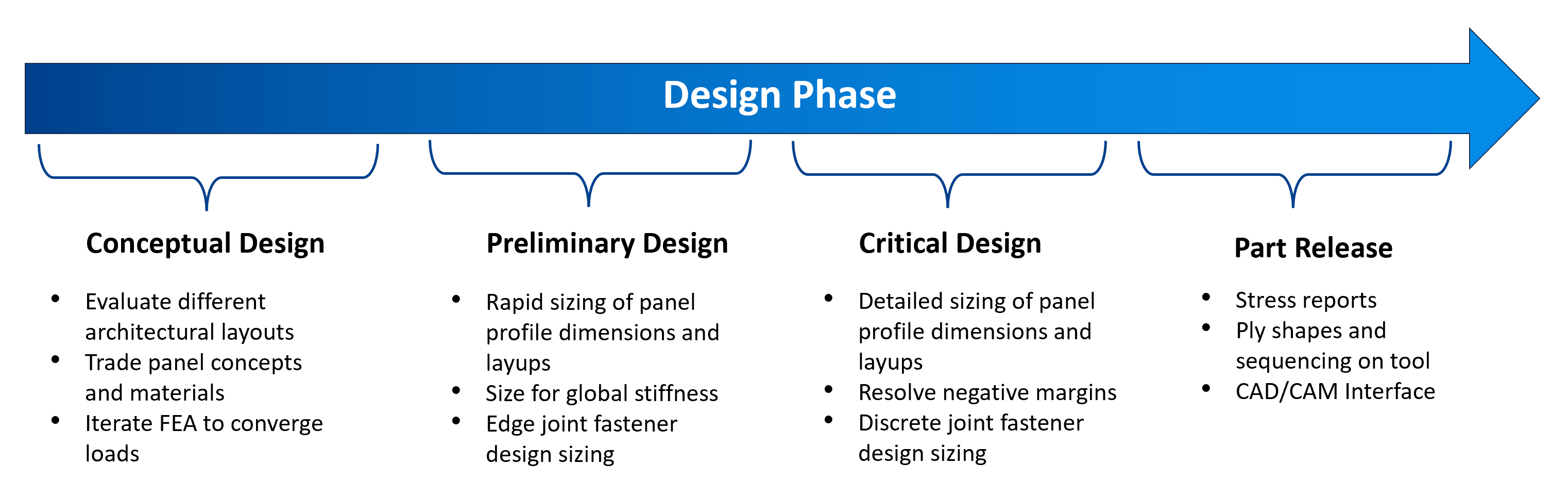
Conceptual Design
In the early phase of aircraft design, engineers are typically focused on speed and exploring the design space. Design to loads are entered either directly with table entry, or by using smeared coarsely meshed GFEMs. In either case, quick trade studies are performed to make decisions on material systems [thermoset/thermoplastic/resign infusion] and architectural layouts [such as wing rib and fuselage frames spacings]. Other design decisions to be made include panel concepts such as Sandwich vs Tee or Hat Stiffened.
During concept definition loads cycling occurs frequently with FEM updates and resulting FEA computed forces. As the structural members are being changed, the internal static load path is redistributed and converged.
In the conceptual phase there are billions of practical and relevant structural design alternatives to process. Even high performance computing (HPC) with multithreading and multiprocessing cannot evaluate all of these candidates. Needed is a way to funnel down options that enable the engineer to interactively steer the sizing optimization, fully benefiting from his experience and intuition with power of computation.
The HyperX capabilities listed to the right provide solutions to these needs.
PANELS AND BEAMS
Conceptual design starts with trading between different panel concepts to attain the lightest weight design. This is done by optimizing each concept’s unique dimensions to the loads in the corresponding FEM property zone, [with automated FEA force extraction].
SANDWICH PANELS
The most basic panels are sheet metal and laminates. These concepts do not have stiffeners nor cores to provide buckling stability. Sandwich panels are useful for structures that have biaxial compression and/or shear loading causing buckling.
STIFFENED PANELS
Useful for structures that are mostly under uniaxial loading. Open sections such as ‘I” or “Tee” are often used for airframe wing skin and closed sections such as ‘Hat’ for fuselage skin.
GRID STIFFENED PANELS
Used for metal biaxial and shear loaded structure such as an aircraft rib, or space launch vehicles. These concepts have many dimensions to optimize.
SMEARED FEM MESHES
HyperX supports several different strategies for modeling panels. The simplest of which allows all objects to be ‘smeared’ into a single surface of 2D shell elements. By doing so, any panel concept shape can very accurately be analyzed and sized without remeshing the FEM.
CONCEPTUAL TRADES
During conceptual phase of design explore alternative configurations. Rapidly evaluate different architectural layouts, material, panel, and joint designs. Establish weight and structural performance trade studies for your project.
LIGHTWEIGHT & MANUFACTURABILITY
Using a full factorial DOE-type approach, HyperXpert™ systematically varies all design variables, including cross-sectional dimensions, materials, and laminates across a part and organizes the data in a tree for controlling the display. This allows you to quickly reduce the design variation in your part, understand trends, and decide the “best” lightweight & manufacturable design for yourself.
RAPID SIZING
Start with rapid sizing which is a non-parametric approach to sizing that does not require user to input variable bounds.
EFFECTIVE LAMINATES
Switch to parametric sizing using effective laminates that represent the layup as homogenous anisotropic material where the thickness is sized with min & max variable bounds and step increments.
INTERACTIVE OPTIMIZATION
HyperX’s interactive optimization approach facilitates the user to start with an open design space with millions of candidates and funnel down to a preferred design.
LEGEND
Plot all relevant input and computed data directly on the model for enhanced understanding of all structural sizing and analysis specific results occurring throughout the design analysis process.
FEM ZONE GENERATION
Automatically split large FEM property areas into many analysis/sizing zones at geometric boundaries such as intersecting structure. Optimize zone shapes and sizes to load gradients.
Preliminary Design
In preliminary design, leading up to Preliminary Design Review (PDR), the vehicle is well-defined. The FEA has 1000’s of load cases to represent the complete flight envelope and off nominal events. Loads groups and structural analysts are working together to converge internal load paths and to meet required airframe stiffnesses. In the case of a wing, these are EI and GJ cut section values per station.
Part cross-sections and layups are being selected. Laminate ply drop ramp rates such as 20 to 1 are being met.
Line loads are used to begin evaluating joint concepts.
FEA eigenvalues are computed to predict buckling.
The vehicle is represented with a ‘loads’ model, referred to as a GFEM (Global) or as a AVFEM (Air Vehicle).
DESIGN WORKFLOW
Design sizing optimization of acreage surface panels and fastened and bonded joints. Improve producibility, reduce weight, and resolve negative analysis margins of safety.
AEROSPACE INDUSTRY METHODS
Instantaneously analyze and size structure for positive margin with respect to hundreds of non-FEA based failure methods commonly used in industry.
ANALYSIS PLUGINS
Directly incorporate your own analysis methods into HyperX via a plugin. Obtain legacy code analysis methods while maintaining HyperX workflow. Plugins can be in C++, C#, and Python.
DATABASAE TEMPLATE
Save all project level data and method preferences in a HyperX Database Template. Use these templates as a starting place for all team members to ensure one source of truth for analysis and sizing.
FEA LOADS CYCLING
HyperFEA™ automatically iterates FEA solutions and HyperX sizing. Converge load paths and enforce global deflection, buckling, or frequency requirements.
SECTION CUTS
Calculate cross-section stiffnesses, center of stiffness, and shear center. Apply minimum EI GJ requirements at different section cuts when sizing. Report summation of “built up” section cut loads, per loadcase.
FEM JOINT
A FEM joint is a HyperX derived entity. They are generated automatically from the intersection of structural zones. One- and two-member line joints are used for load processing, meeting shear and pull-off loads.
COMPOSITE STIFFENED PANELS
Cross section ratio bounds can be used to ensure that the optimized geometry is producible. Designs with short, squat or tall, slender geometry can be filtered out.
LAMINATE FAMILIES
Layup stackings defined as columns in a table with shared plies. Sizing produces manufacturable laminates that have continuous sequence of layers laid up over a part.
STOCK SIZES
Non-machined, sheet metal parts are supplied by vendors in material stock sizes. HyperX can enforce that stock sizes are used when performing optimization.
DASHBOARD
Upload your HyperX results from your local database to a shared database hosted in either the cloud or on company servers. Interactive 2D curve trendlines give immediate insight into design studies. Others can view the results using typical web browsers.
SCRIPTING API
Automate repetitive process tasks through code or seamlessly incorporate HyperX into larger software environments.
Critical Design
Critical design marks the shift to a mature structure design with most decisions made on manufacturing tooling, panel cross sectional dimensions, and acreage layups are locked down. Since most of the design has been chosen, higher-fidelity models contain more elements to discretely model features such as stiffeners, fasteners, sandwich core ramps, and metal fittings. Final material allowables are established for strength checks, including damage and fatigue criteria.
This phase typically has aerospace engineers working to resolve negative margins of safety to final FEA load iterations in order to submit passing designs for Critical Design Review (CDR).
A need is in depth analysis traceability.
At this stage the vehicle is represented with a DFEM (Detailed) model with a finer mesh that discretely models features.
Solid elements are used for fatigue analysis of fittings. Lugs are typically analyzed using classical aerospace methods.
ANALYSIS WORKFLOW
During this project phase, primarily perform aerospace stress analysis methods simultaneously executed to thousands of load cases. Immediate interactive feedback to the engineer on the FEM: critical failure modes, load cases, and margins of safety
ANALYSIS WATCH WINDOW
The Analysis Watch Window automatically lists every single margin of safety for the zones selected.
WATCH WINDOW
Tabulate data for a selection of zones. Use this real time, interactive data to trace through analysis calculations and supplement reports.
STRESS REPORTS
HyperX provides various stress report formats for exporting stress data from the software. Useful for traceability as well as standalone documentation.
DETAILED SIZING
When need to resolve negative margins or over conservatism in the design, rigorously size many structural zones to all load cases with user controlled variable bounds.
DISCRETE STIFFENED MODELS
The discrete-stiffener modeling (DSM) approach explicitly models stiffeners with bars, shells, or a combination of element types.
MATERIAL AND FASTENER DATABASE
Maintain and deploy verified and test validated material and fastener properties required for certification.
FASTENED JOINT
Fastener types, diameters, spacing, and number of rows are sized. Analysis include fastener bearing and bearing-by-pass on the laminate. NASA 5020 analyses include pull off and torque.
BONDED JOINT
Adhesive material, thickness, overlap length, and taper angle are sized. Analyses include linear/nonlinear peel and interlaminar shear stresses; and VCCT energy solution for disbonds.
DIMENSION OVERRIDES
If the user identifies regions where part dimensions need to be modified, these modifications can be specified as dimension overrides in HyperX.
FEM REIMPORT
As the design matures, the initial FEM geometry, architectural layout, and mesh may be redefined. The new model can be reimported into the HyperX project, keeping its previous setup data intact.
Part Release
The aircraft design cycle ends with part release. In order for parts to be released to the shop floor, they must be fully defined in part drawings, with all manufacturing considerations considered. These drawings are typically accompanied by detailed stress reports, which contain summaries of all design and analysis requirements, margin reports and screenshots of important part data.
At this phase iterations are done between stress sizing and results produced by AFP software such as CGTech’s Vericut. Margins are defined that account for simulating fiber paths of complex curved parts that quantify steering radius limits and laps and gaps in slit tape placement and corresponding updates to the FEM ply rosette angles.
CAD/CAM INTERFACE
CAD and CAM software play a big role in generating producible designs. HyperX is able to read in CAM manufacturing data such fiber directions and export data such as optimized CAD ply boundaries.
PLY SEQUENCING
The minimum-weight laminate for a zone is not always the most producible. Ply sequencing assembles zone laminates into producible plies on a structure.
MACHINING
HyperX generates producible designs for machined grid stiffened panels (such as orthogrid) by considering factors such as machining tolerance and geometry rules.