Analysis Methods and Customization
HyperX offers an extensive suite of failure criteria consistent with standard aerospace analysis which incorporates 25+ years of industry use and review. Custom methods can be implemented via Analysis Plugins.
Feature Pages
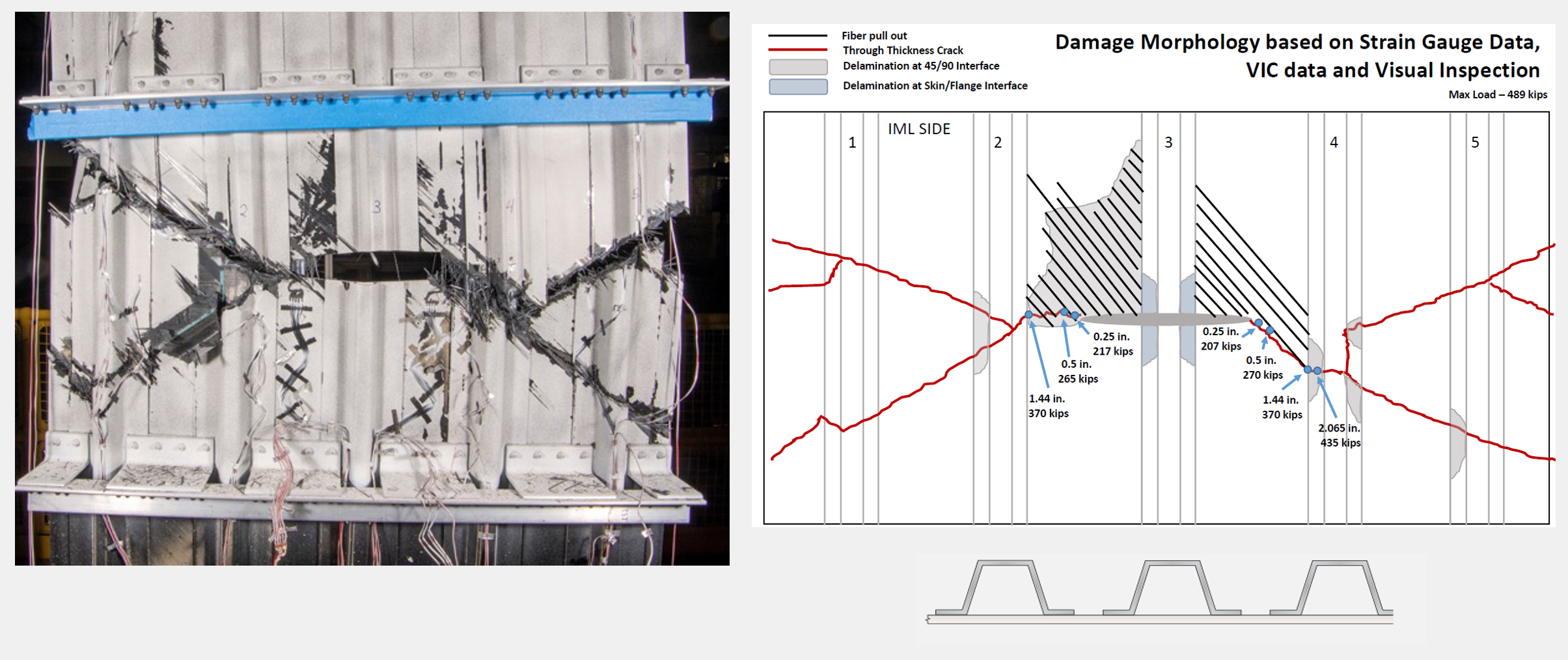
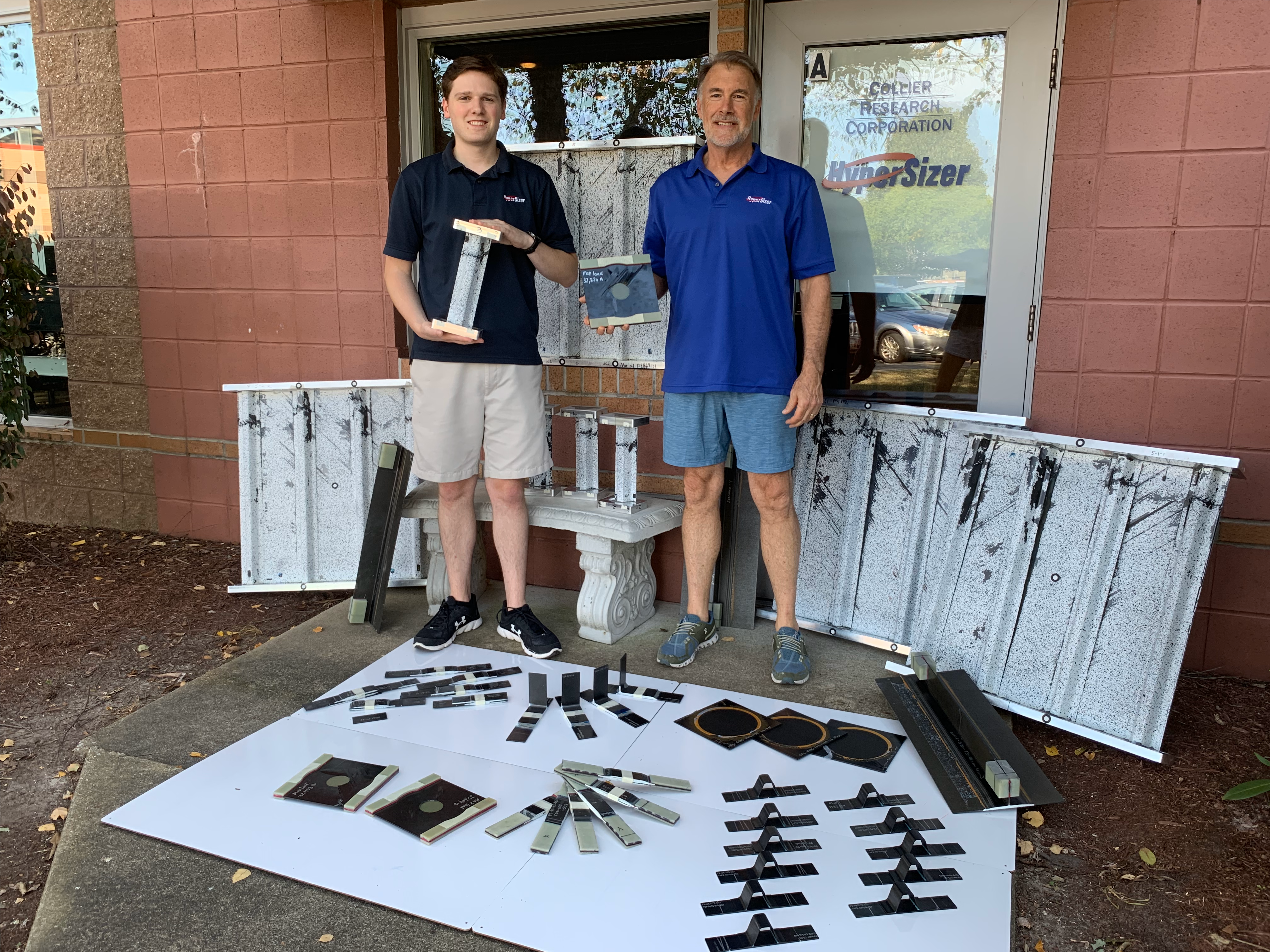
Testing at NASA Langley 2019. Boeing and Spirit Aero’s Two-Bay Crack, large damage prediction tool.
Instantaneously analyze and size structure for positive margin with respect to hundreds of non-FEA based failure methods commonly used in industry.
HyperX has been developed to include an extensive library of non-FEA-based failure analysis methods traditionally used in the aerospace industry to drive sizing and analysis resulting in margin of safety stress reports.
The following list outlines the broad categories of failure criteria implemented in the HyperX analysis code:
|
|
These methods directly support FAA certification requirements.
All criteria included in HyperX also have a corresponding HME (HyperX Methods and Equations) Document. These documents clearly outline the assumptions, derivations and calculation steps taken for each margin of safety. In many cases, additional verification and example problems are also included. Each HME ends with a list of cited references – which can be printed directly into HyperX-generated word stress reports or can be copied directly to aid report-writing.
HyperX includes built-in failure criteria for the numerous different buckling scenarios potentially experienced during flight. By using known analytical solutions based on assumed boundary conditions, a critical buckling load is calculated in each direction. This solution bypasses the need for FEA Eigenvalue buckling solutions, thereby saving valuable calculation time.
HyperX offers three main categories of buckling failure methods:
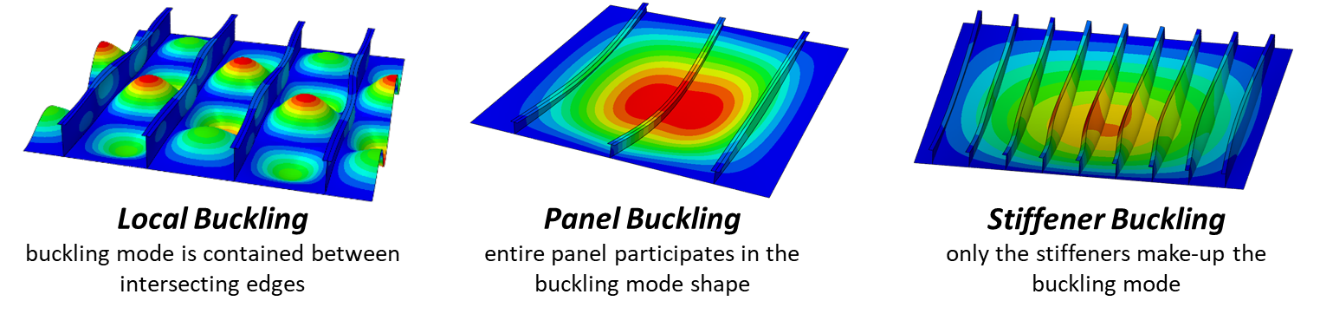
Sandwich panels, typically employed as a light-weight material system for buckling-critical skin structures, have several different design variables. Each design variable has its own set of potential failure modes.
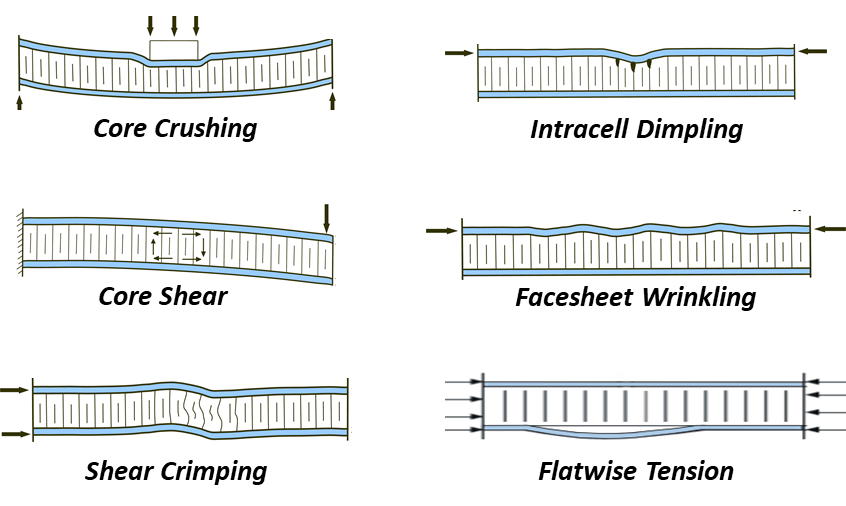
The images above represent the sandwich failure criteria categories found in HyperX, which account for all sandwich failure possibilities. During sizing operations, these methods are evaluated in tandem, ensuring that the resulting design returns positive margin for all criteria.
Specifically for composite materials, rather than just relying on ply-based stress and strain allowables, HyperX supports laminate-level strength analyses as well. In this case, laminate-level stress allowables, typically obtained via test, are directly compared to the panel loads determined by HyperX in the applicable direction. Pristine, after impact, barely visible impact damage (BVID), compression after impact (CAI), and open hole strain allowables can all be defined for implementation in their own specific analysis method.
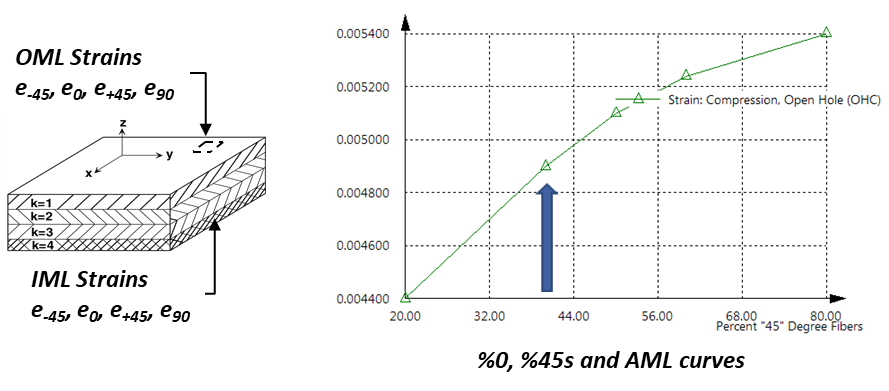
HyperX includes several different metrics for evaluating joint failure. Each method takes into account the type of joint, the joining mechanism, and the members being joined in order to write a comprehensive margin to the joint entity.
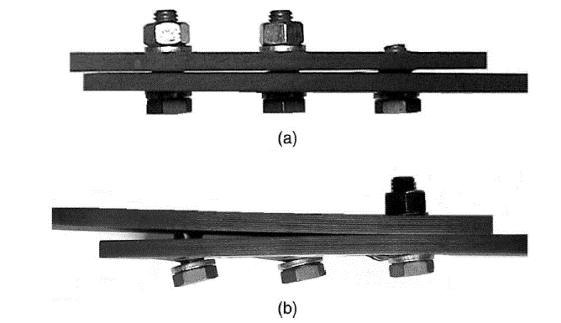
Fastened joint failure could occur in the form of fastener strength failure, sheet bearing, or a bearing-bypass interaction. HyperX utilizes fastener specification data as well as sized panel results in order to properly size for each consideration.
Bonded Joints
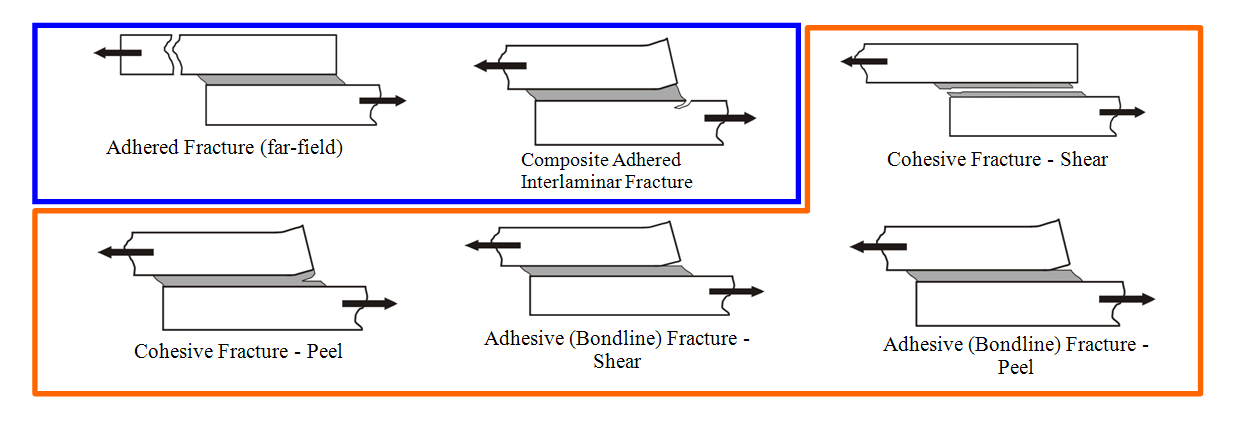
Stress Based
In plane and out of plane stresses are computed in the adhesive bond line, as well as throughout the thickness (ply by ply) of joining laminates. Usually, stresses are extracted at a characteristic distance (.0025”) and compared to their respective allowables. Many different stress interaction failure criteria are provided.
Fracture Energy Based
Failure considerations include fracture in principal stress directions, edge delamination, and adhesive delamination – necessitating the evaluation of all joint members within the analysis. Fracture mechanics techniques predict (and therefore, avoid) crack growth of a particular size. The FAA requires an assumed crack (usually of ¼”) to be analyzed for residual strength.
Custom Plugins
Directly incorporate in-house analysis methods into HyperX via plugin. Obtain analysis method and legacy code implementation while maintaining HyperX workflow.
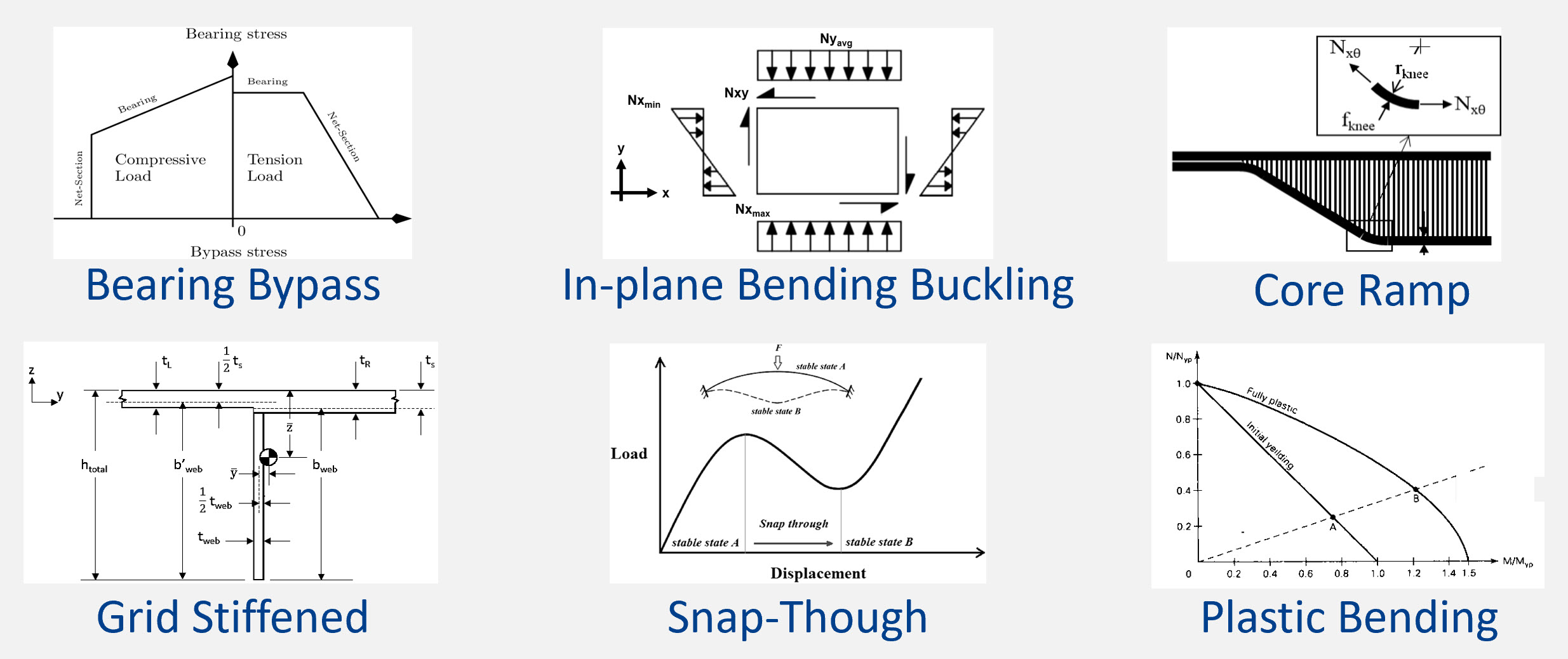
Example non-proprietary plugins available with a HyperX license.
The HyperX install includes supplemental Collier Aerospace plugins that are developed and maintained in-house, which can be used alongside the software’s native methods. These plugins are designed for the strength and stability analysis of metal grids, core ramps, sandwiches, and composite panels. In addition to these general-use plugins, more specific plugins have been internally developed and are available upon request. Examples of these plugins include:
- Strength analysis of curved metal beams
- Local crippling analysis of grid stiffeners
- Plastic bending of metal beams
- Local pressure analysis of DSM skins
- Local and panel snap-through buckling analysis for orthogrid, flat, and sandwich panels
- Strength analysis of metal and composite panels with flanged and unflanged cutouts
- Multi-bay crack analysis of metal panels (Niu)
If your in-house analysis method is not natively included in HyperX, a custom plugin can be created to add that method directly into the software. Your company can develop the plugin or contract with our company to develop it for you.
Plugins are also used to integrate a company’s legacy analysis code into HyperX. The plugin package can wrap existing C/C++/Fortran code using static or dynamic link libraries (LIB or DLL respectively). You can also read external files and shell out to executables, like Python scripts, if desired.
Methods written in an analysis plugin can be directly integrated into HyperX, such that they can be selected alongside native methods in order to be accounted for in both sizing and final analysis use-cases.
The diagram below illustrates a custom Stringer Panel Plugin Package, which contains custom analysis methods for Skin Strength, Stringer Strength, Local Crippling, Section Crippling, and EI Ratio check.
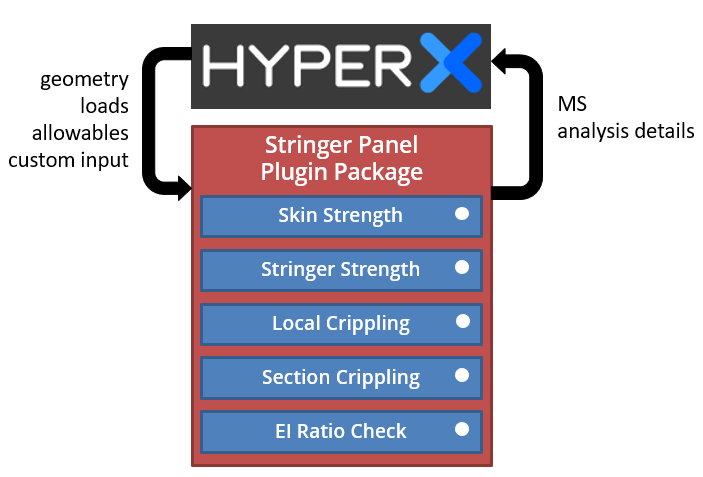
This custom plugin paradigm provides additional control and customization over your sizing process, while also maintaining the consistent and traceable analysis platform that HyperX provides.
When an analysis is initiated in HyperX, HyperX will send all geometry, loads data, material allowables, and other relevant data directly to the plugin package. The plugin package will use this data to evaluate each analysis criterion for each applicable zone under each load case – just as HyperX does for native methods. Then, all margins of safety and corresponding analysis details are passed back to HyperX. In this way, all data corresponding to the custom analysis methods can be treated exactly like natively-generated analysis data – meaning this can be displayed in the watch window, plotted directly on the model, and analysis detail and stress reports can be printed for each method.
For more information about what data is sent from HyperX to plugin packages, visit the API Types and Enumerations documentation on our Help website: Plugin API
Contact Us
This site is protected by reCAPTCHA and the Google Privacy Policy and Terms of Service apply.