Composite Laminates
Laminates have many variables to optimize: ply material, thickness, angle, and layup stacking. Three approaches are provided: effective laminate, discrete laminate, and laminate family.
Feature Pages
See Relevant News Article:
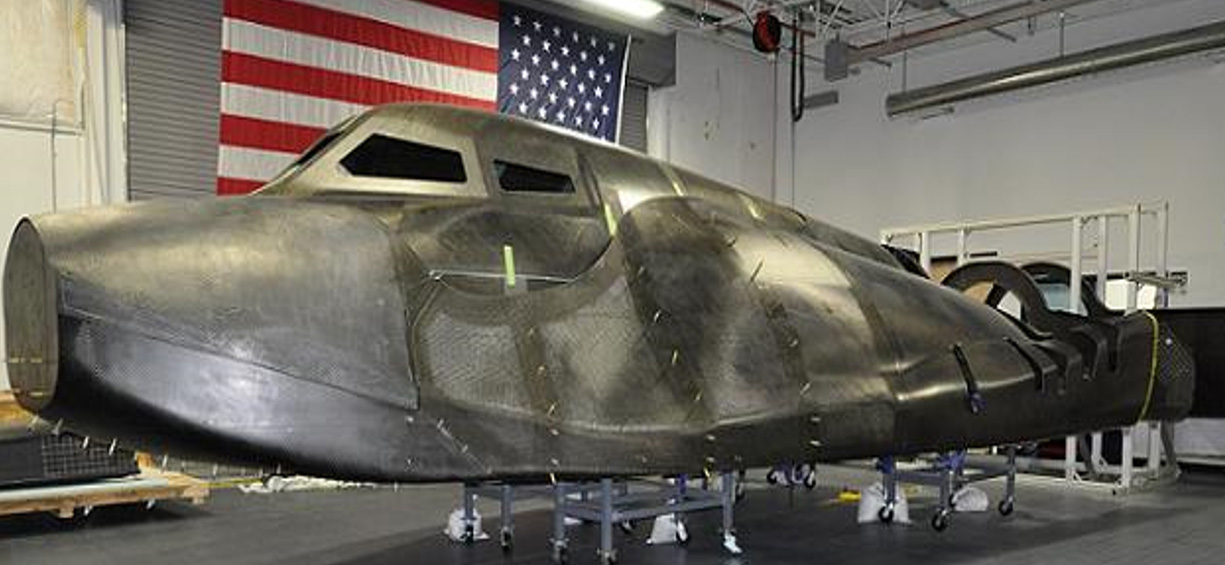
Net Composites – HyperSizer Aids Design of Dream Chaser Spacecraft
“The software’s suite of industry-standard failure criteria was extremely valuable for our team, enabling us to quickly size the Dream Chaser structure and perform architectural trade studies,” says Andy Kim, Senior Structural Engineer for SNC. “The software’s rapid sizing capability gave us more time to interrogate our results and gain insights into the sensitivity of the structural weight to various design features and stiffener cross sections.”
Analyses for composite materials can be ply-based and laminate-based. Laminate based strength include Open Hole Compression, OHC, and Compression After Impact, CAI, etc. type allowables. Both ply-based and laminate-based can include correction factors.
Introduction

Effective Laminates
A smeared representation of a laminate. Three variables: ply material, laminate thickness, and laminate angle % in the 0/45/90 directions.
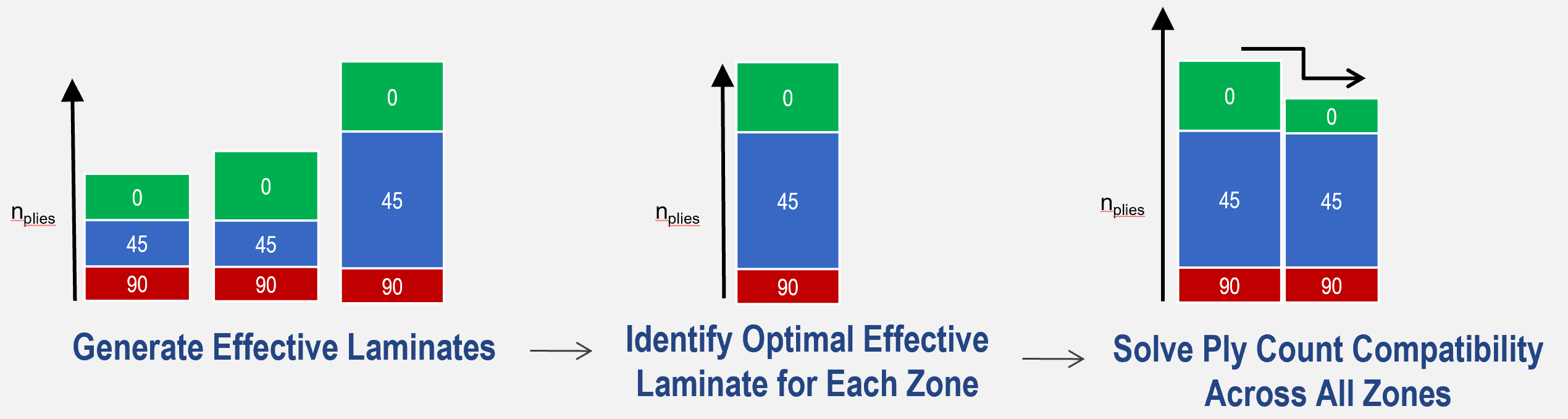
Process for optimizing with ELs
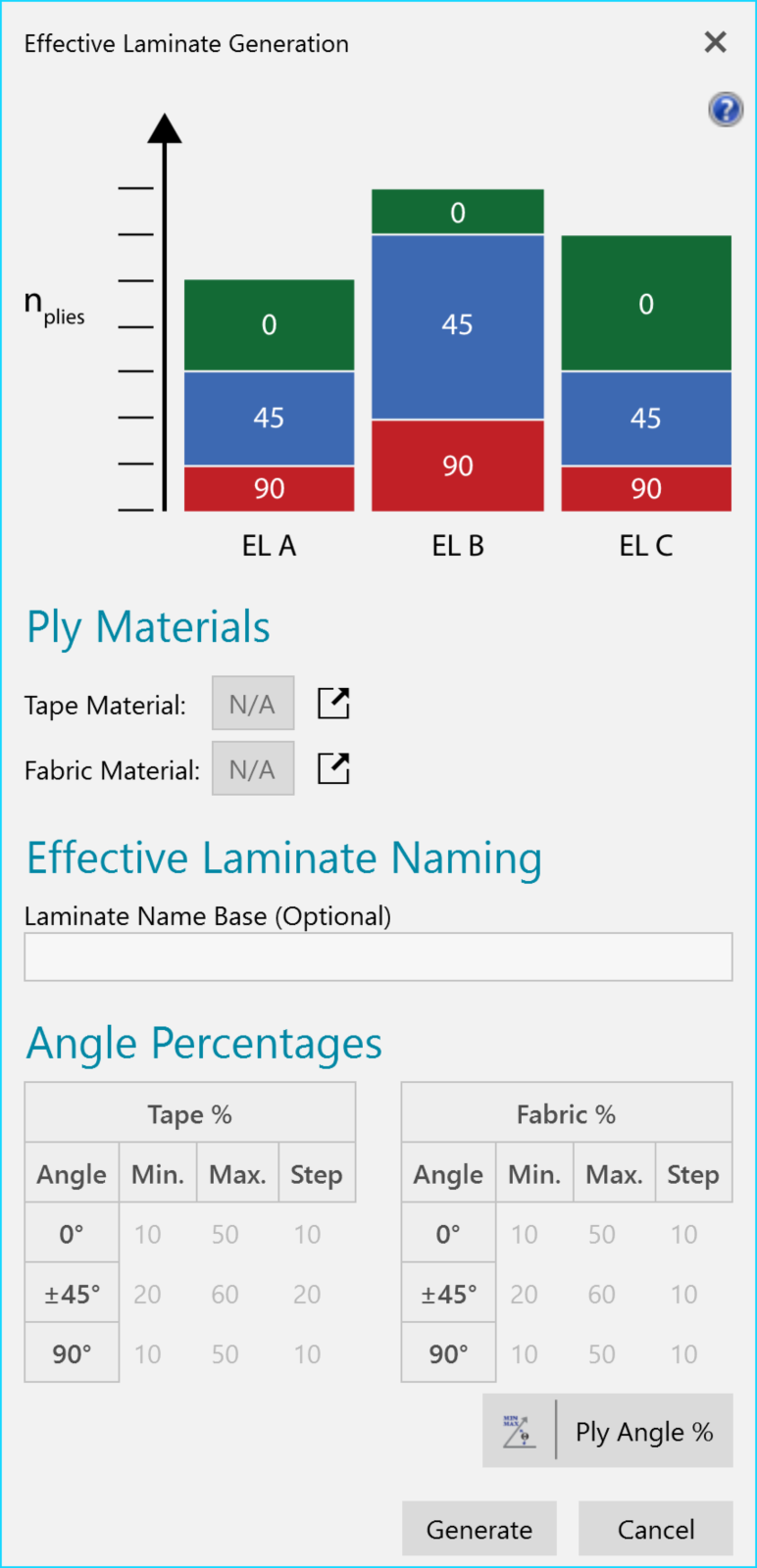
Effective laminates (EL) are suitable for rapid optimization since they can be sized by changing their thickness without consideration for their actual layup stacking order.
The software can automatically generate an EL for each combination of ply material and ply angle %’s the user selects to consider. Each of these ELs can be sized to find optimum ply counts in each angle.
Discrete Laminates
Layup stacking. Four variables: ply material, thickness, angle, and stacking order. Primarily used to represent imported laminates from the FEM defined with data such as Nastran PCOMP.
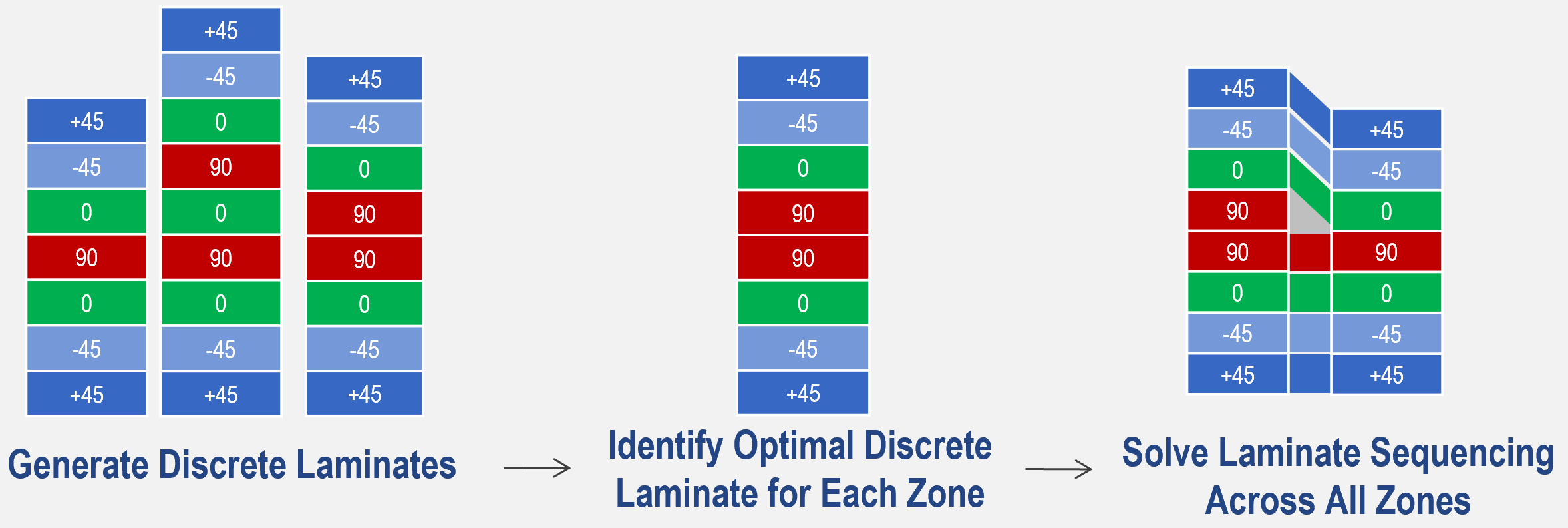
Process for optimizing with DLs
HyperX can sequence discrete laminates across a surface in a 2D manner as illustrated in the figure.
However, for large structures with many zones, the HyperX best practice is to use laminate families.
Laminate Families
Layup stackings defined as columns in a table with shared plies. Sizing produces manufacturable laminates that have continuous sequence of layers laid up over a part.
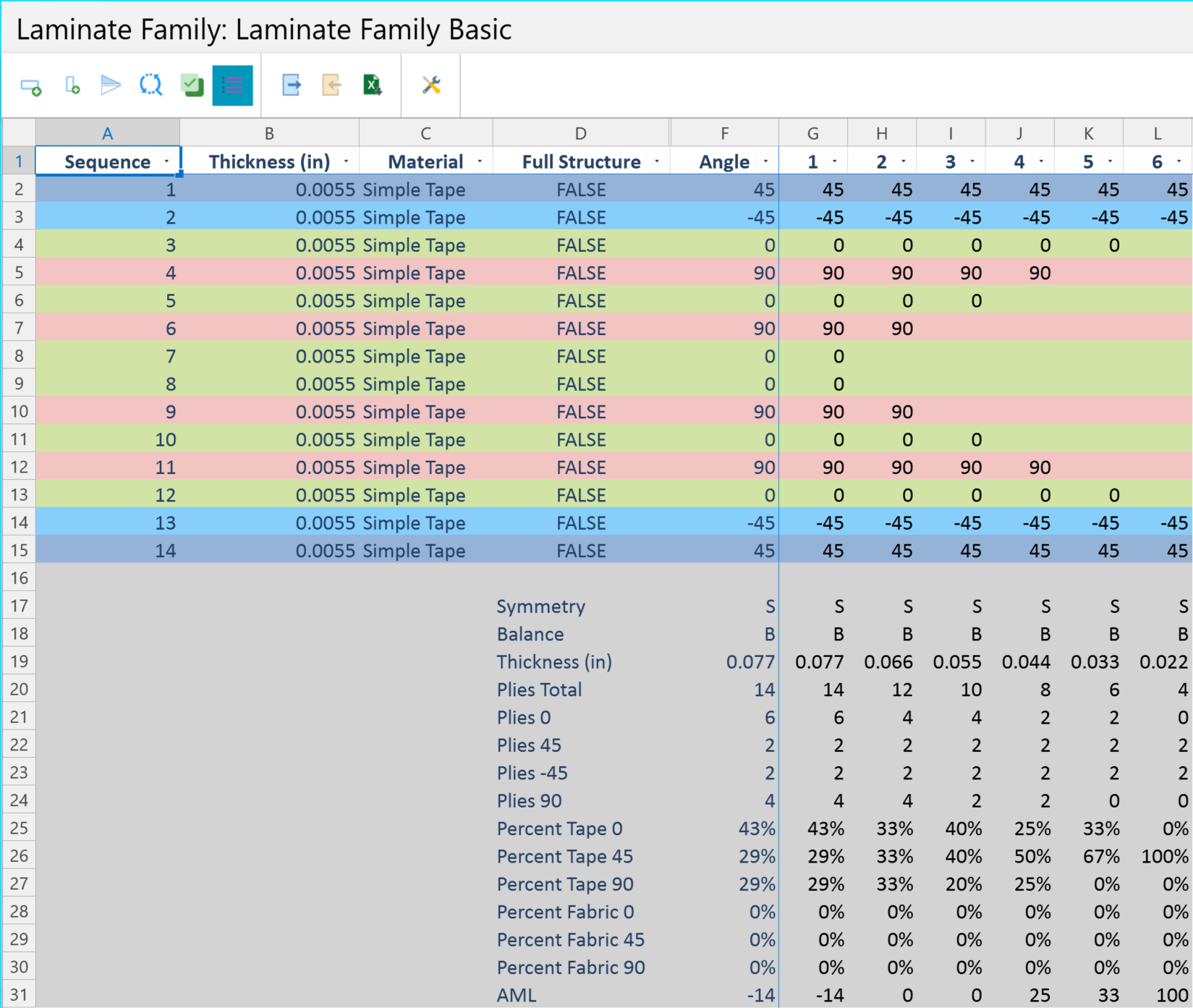
Laminate Family with meta data displayed at bottom in gray.
Laminate families (LF) are the primary way to size laminates.
Each column of a family is a discrete laminate candidate available for selection by the sizing optimization.
Main Stacking Sequence
HyperX is able to generate candidate main stacking sequences (MSS) that represent all discrete laminate solutions (ply layups) from zone or element sizing results.
Advantage is the software will determine the optimum MSS that satisfies all zones of the structure so the user doesn’t have to guess and likely not begin the process with a good one. This results in a MSS with the fewest ply counts that represents all possible individual input laminates.
Ply Drop Patterns
After a MSS is defined, then a user is able to auto generate candidate laminate family ply drop patterns, referred to as ‘stacking options.’ An additional advantage is that they abide by all of the user selected layup rules.
Laminate family generation and optimization follows all of the rules shown below.
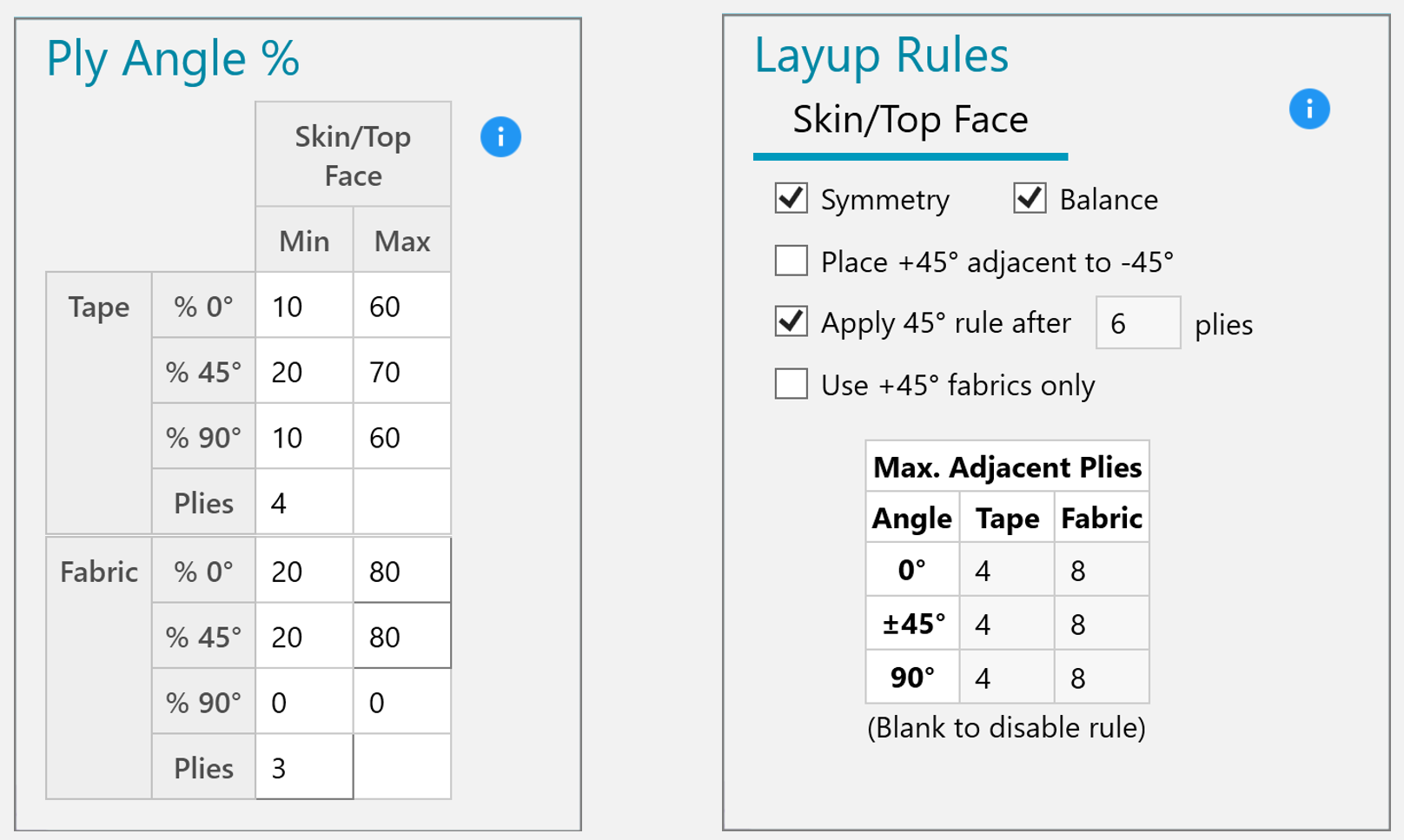
Layup rules are user defined.
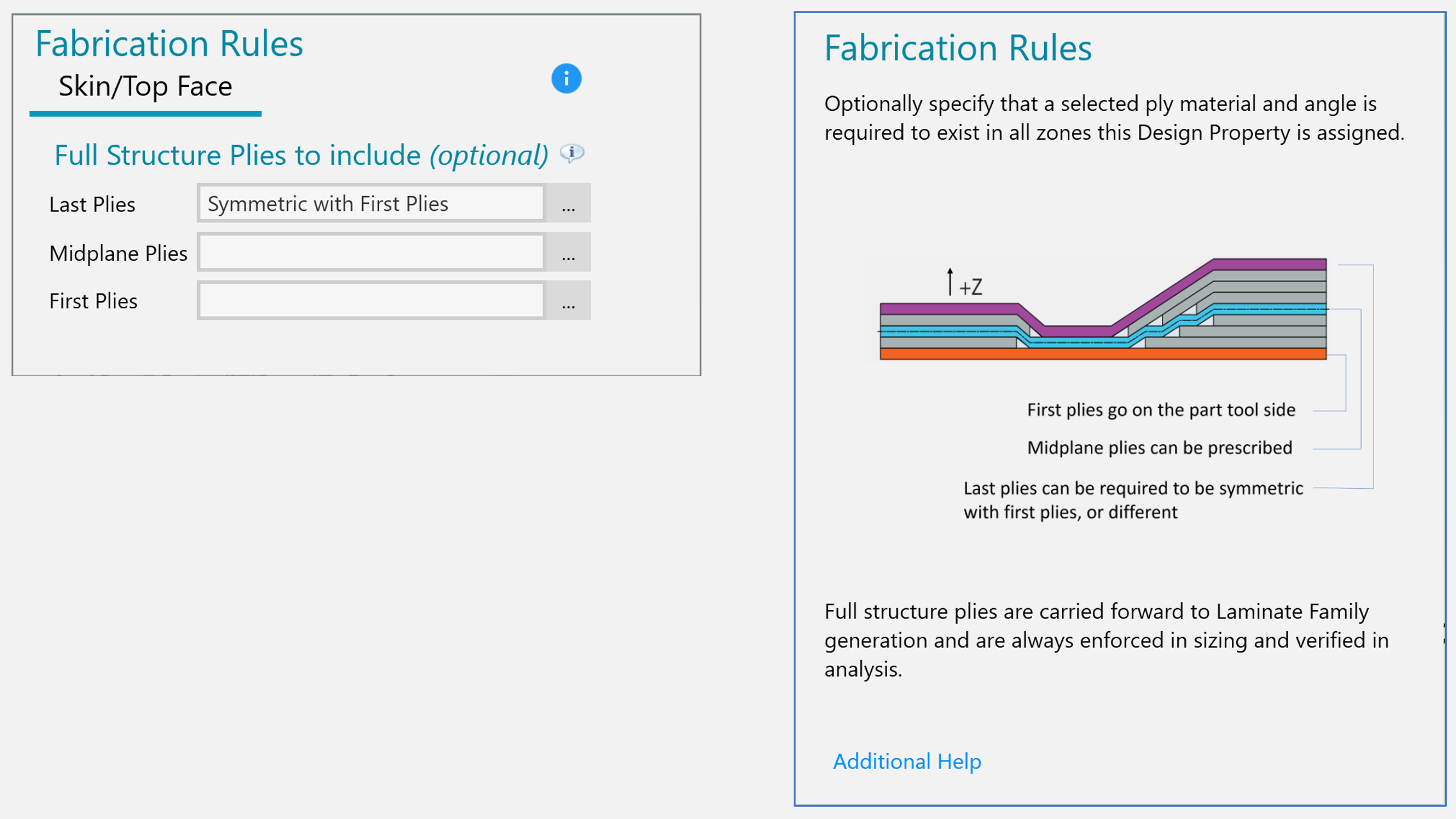
Fabrication rules are user defined.
Features
- Autogenerate stiffened panel specific laminate families for the stringer
- Any ply layer can be identified as required full assembly
- Non traditional laminate families can be made and used. These have ply angles other than 0/45/90
- User can edit, in place, on the form
- User can export and import from an Excel spreadsheet
Contact Us
This site is protected by reCAPTCHA and the Google Privacy Policy and Terms of Service apply.