Composite Stiffened Panels
Composite stiffened panels have many manufacturing constraints due to their tooling complexity. HyperX excels at finding low weight designs while satisfying fabrication criteria.
Capability Pages
Manufacturing composite stiffened panels can be complex for geometry such as “I” or “hat” stiffened panels due to the multiple manufacturing tools and various ply packs that must be assembled and cured simultaneously. This requires many constraints to be enforced on the panel geometry during optimization to ensure that the panel is manufacturable. HyperX exposes a variety of typical geometry rules for stiffened panels.
Additionally, stiffened panel geometry can be driven by needs other than weight. For example, stiffener height and spacing is often dictated by part clearance, fastener or bond accessibility, subsystems, etc. HyperX makes it easy to quickly identify the weight impact of constraining these dimensions.
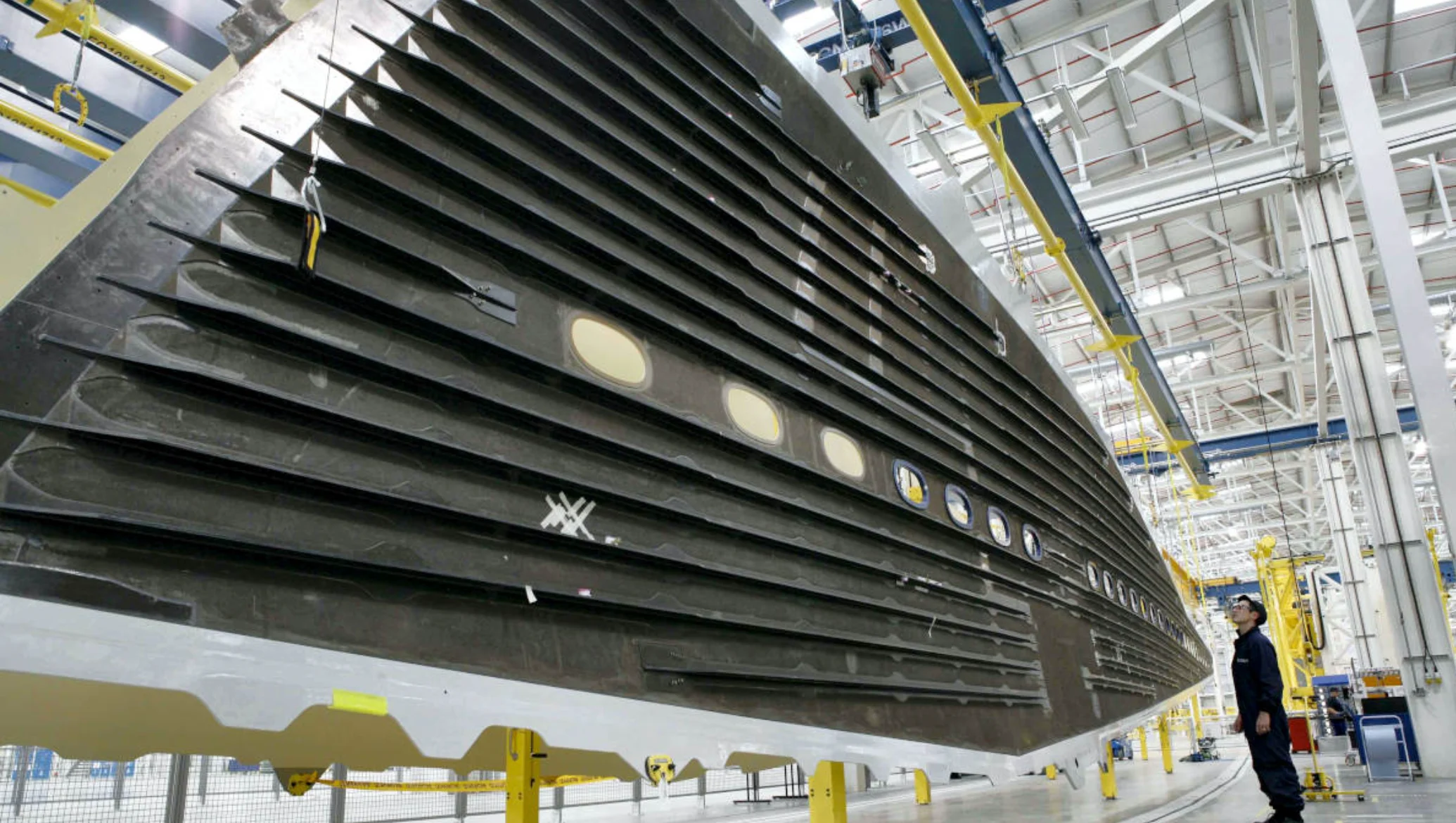
Cross section ratio bounds can be used to ensure that the optimized geometry is producible. Designs with short, squat or tall, slender geometry can be filtered out.
The ratio bounds enforced during optimization fall into two categories: cross section ratios and stiffener laminate ratios.
Cross Section Ratios
The first category is used to constrain the overall geometry of the panel, such as the ratio of the height of the web to the width of the foot. These are typically used to ensure that tooling for the panel is feasible.
Stiffener Laminate Ratios
The second category of constraints relates to the thicknesses of the individual composite entities in the stiffener, such as the thickness of the ply pack to the thickness of the base laminate. These are used to ensure that the composite entities are easy to work with during assembly and cure. For example, having an excessive number of plies in the base laminate can lead to wrinkles during cure at the corners of the stiffener.
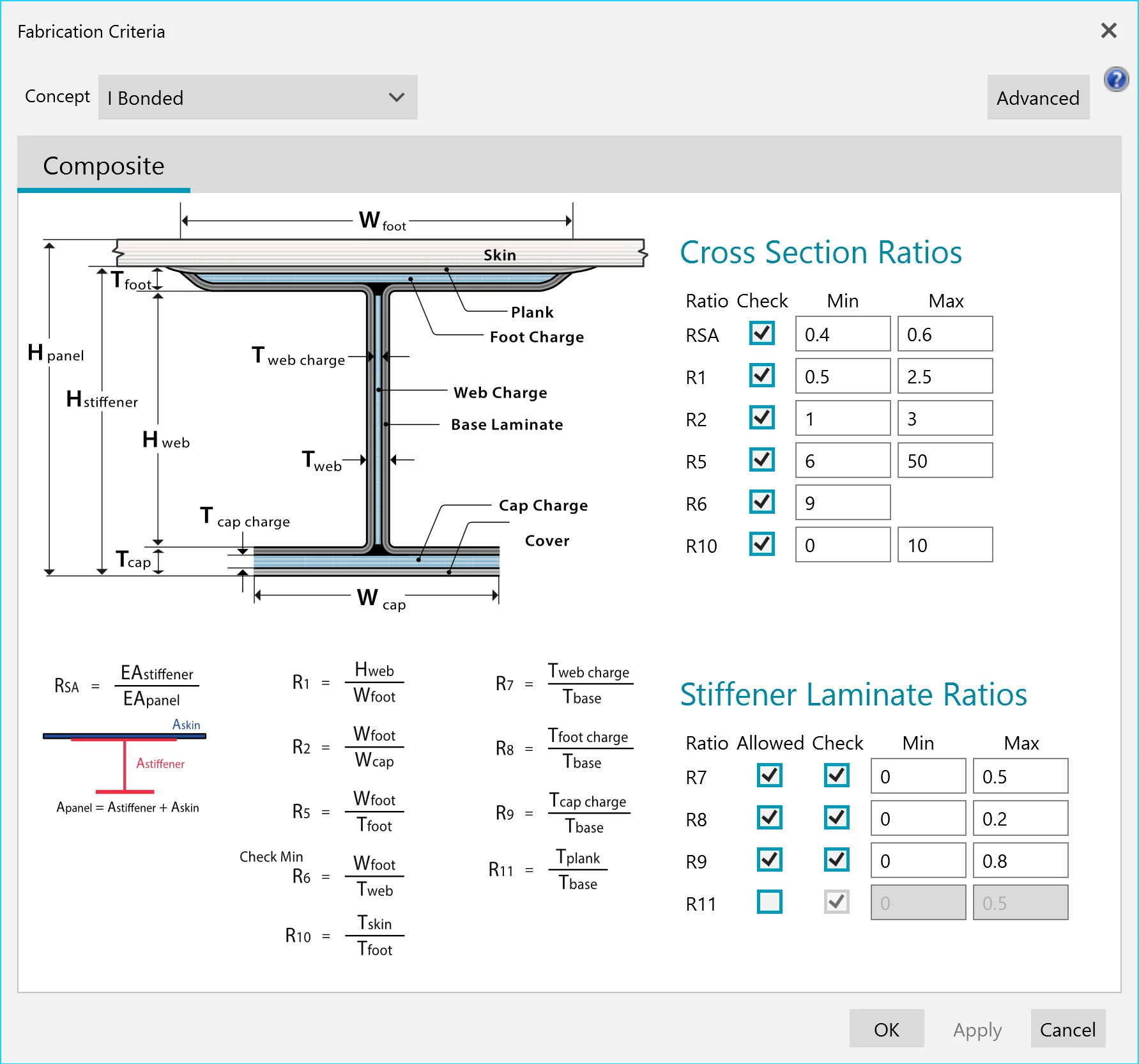
HyperX goes beyond finding an optimum layup for each stiffened panel object (web, cap, etc) and determines ply connectivity between objects.
Optimized stiffened panel geometry and layups can be displayed in a 2D viewport where the user can examine the size and shape of the panel as well the plies within the panel. Multiple viewports can be opened to compare designs between zones.
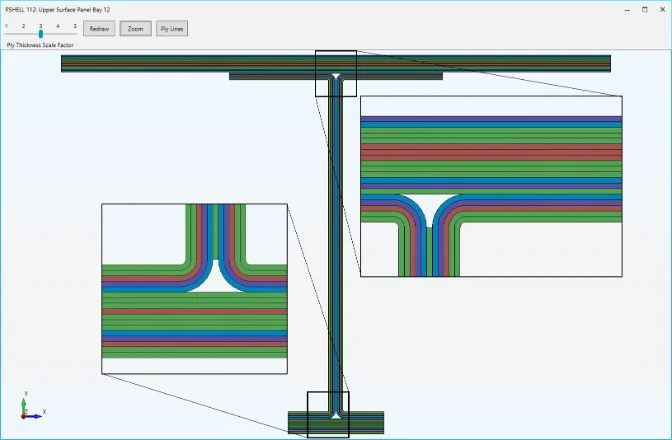
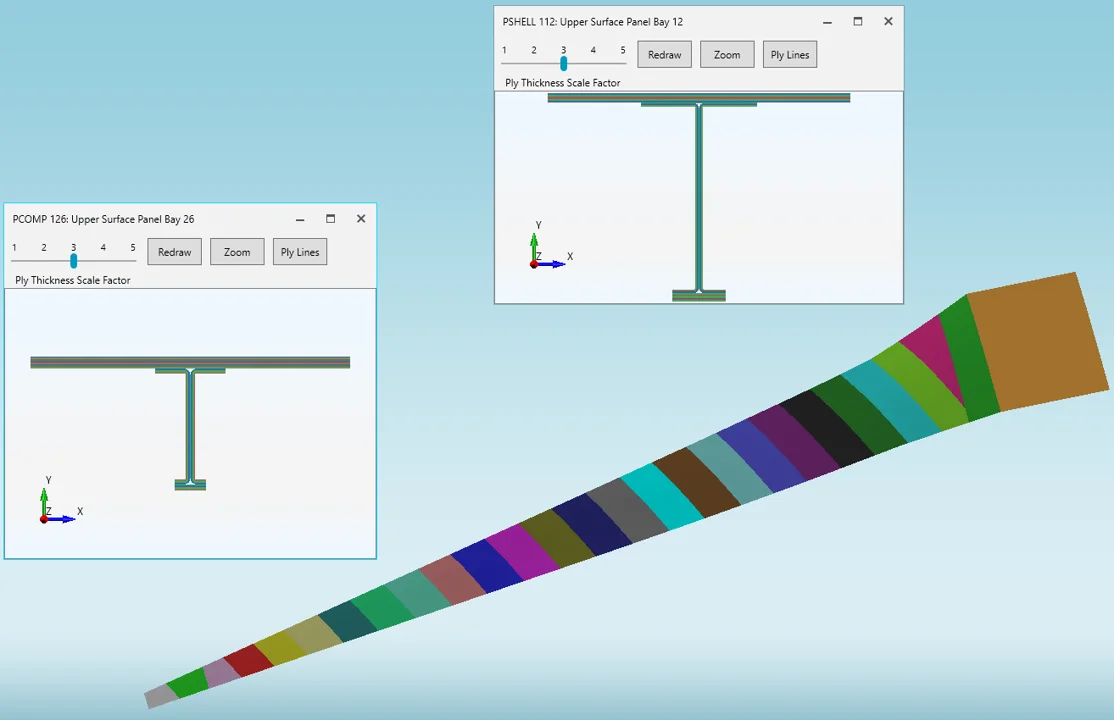
Height and stiffener spacing can be constrained by producibility as well as subsystem requirements. HyperX can study weight impact due to these constraints.
HyperX’s rapid sizing capability for stiffened panels can be used to quickly study the impact of constraints on stiffener height and spacing. The two variables can be studied independently or simultaneously. For each datapoint, HyperX will determine the optimum designs for all panels in a structure with the height or spacing (or both) set to a fixed value across the structure. The resulting data is useful for evaluating the mass penalty of different configuration decisions made at a systems level.
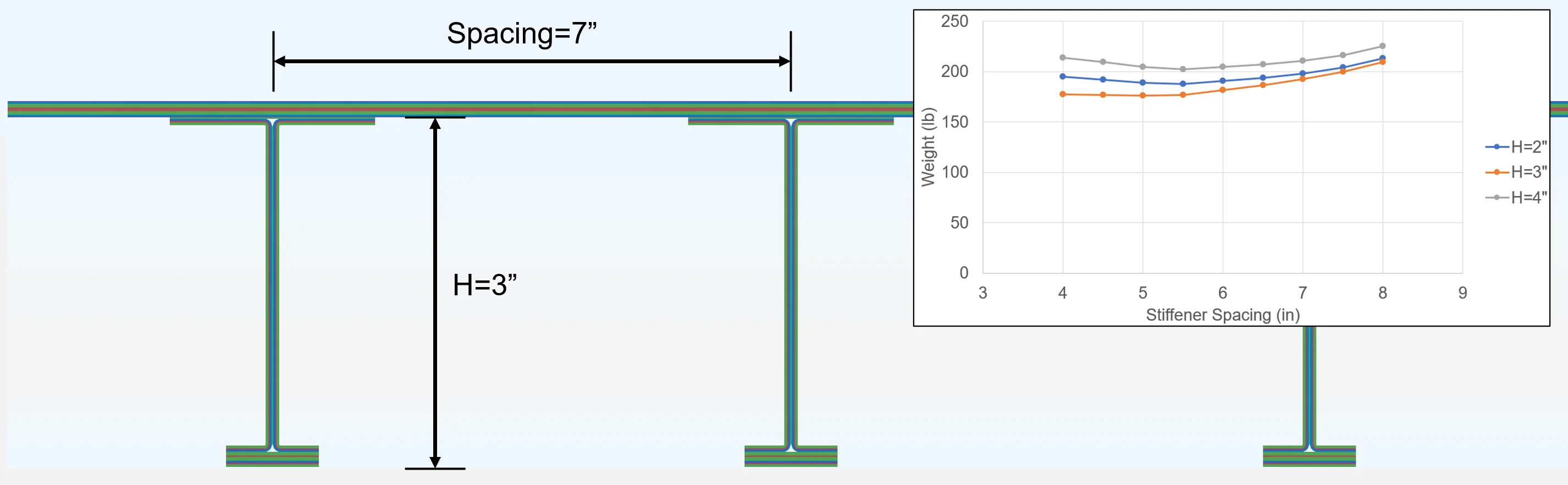
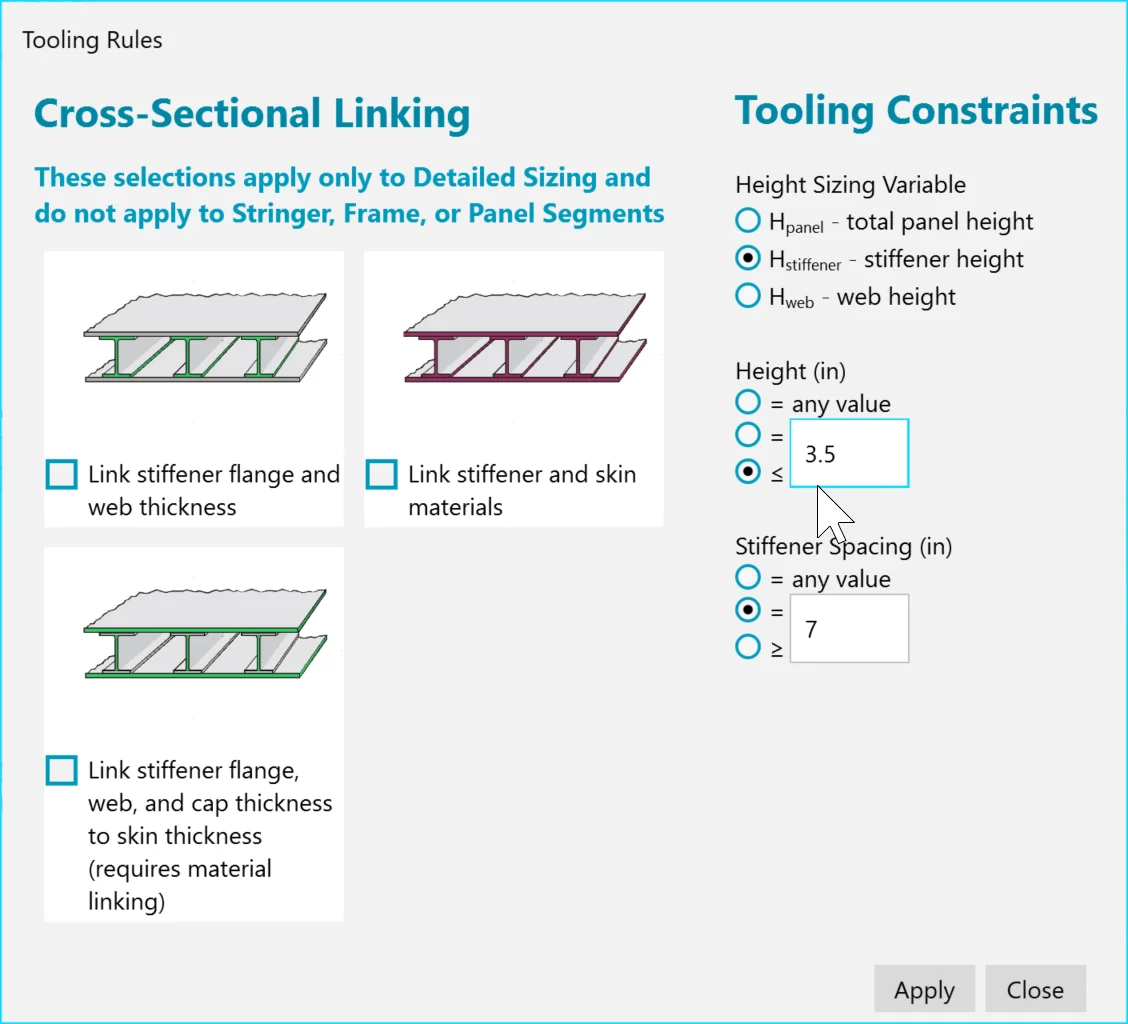
Contact Us
This site is protected by reCAPTCHA and the Google Privacy Policy and Terms of Service apply.