Stress Reports
HyperX provides various stress report formats for exporting stress data from the software. Useful for traceability as well as standalone documentation.
Capability Pages
In addition to viewing data directly in the viewport, HyperX offers several different stress report options for exporting data directly from the software to either Excel Spreadsheet or Word Document.
Each report type has its own purpose and use-case, summarized in their respective sections below. The over-arching goal, however, is to provide the user access to all data. In this way, engineers can directly follow all calculation steps throughout each analysis and sizing routine. Additionally, this data can be used to directly supplement in-house stress reports – whether by directly copying-and-pasting, or via scripting mechanisms to directly print HyperX-extracted data into in-house report formats.
This advanced level of reporting has proven instrumental in providing the level of traceability required to smoothly achieve certification.
Excel-based Stress Reports
Spreadsheet Stress Reports extract all relevant data to summarize: FEM files, database settings, margin summary tables, critical load cases, and sizing results.
The full list of applicable data is shown in the image below, in which each check-box option represents a tab of data added to the report.
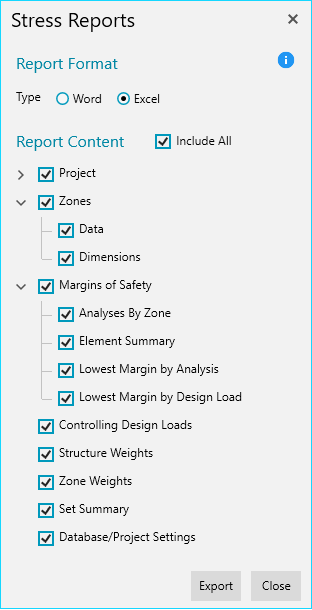
The user has complete control over what data is exported in each printed report.
This report also includes additional, back-end data that is not readily seen in the interface. For example, Excel-based reports include the Critical Design Loads tab – which contains a table ranking the load scenarios used to analyze the model in order of criticality. This is particularly useful to streamline future FEM runs, as well as better-inform in-house stress reports.
In general, the biggest use-case for Excel-based reports is for readily creating tables of summary data that can be copied and pasted to other, more verbose reports to support design review or certification.
Word-based Stress Reports are generated in an organized format with headers, table of contents, and sample calculations of each failure criterion with identified critical data.
Of particular interest in Word-based reports is the Failure Calculations section. Here, each active failure criterion is summarized – including all necessary equations. Tables containing the data corresponding to the critical margin written are also provided per criterion. The screenshot below illustrates this level of detail, using the Intracell Dimpling check as an example. Note that the pages following the allowable equation outline calculations for each variable contained in that equation.
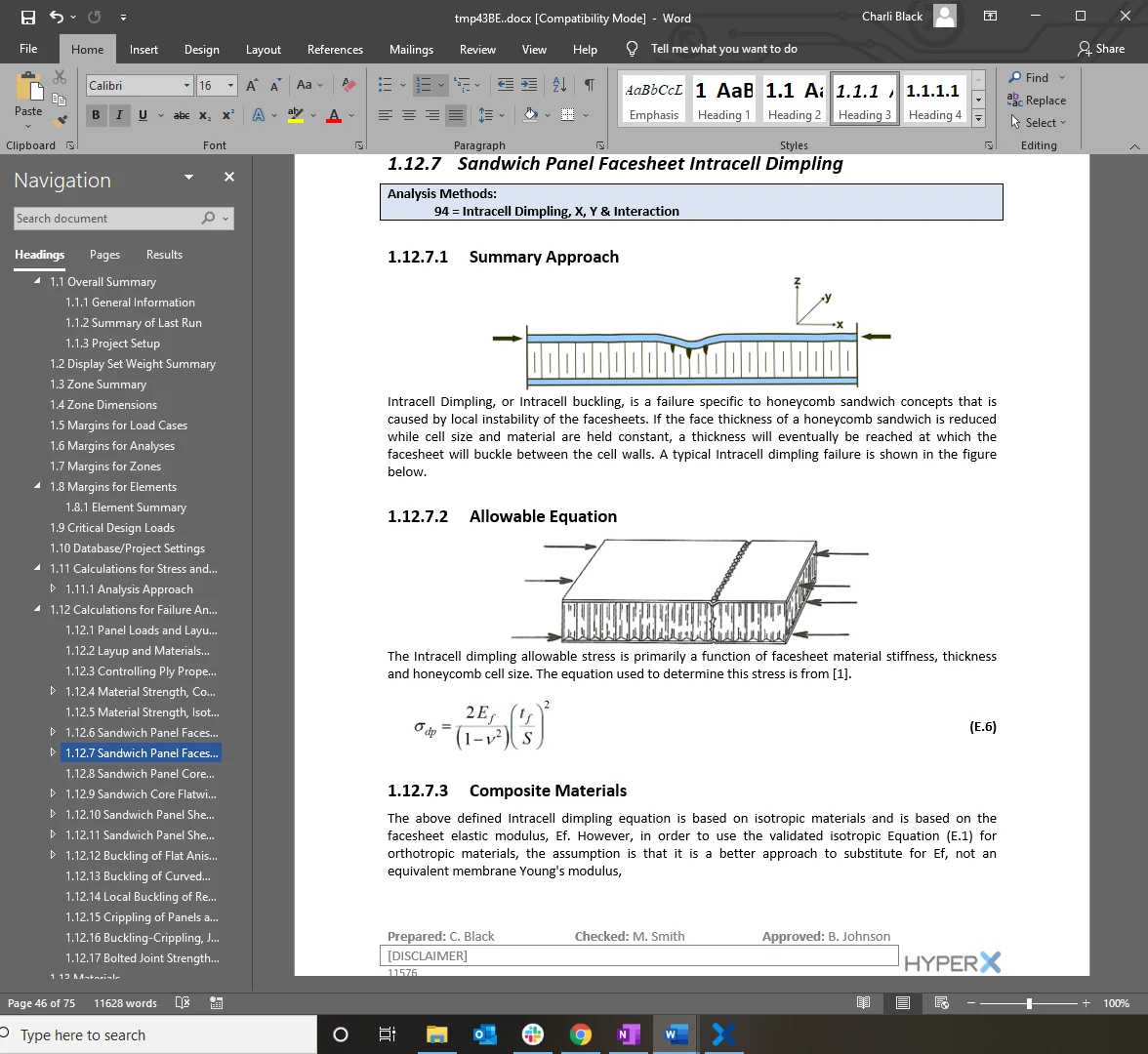
The verbiage and equations are coming directly from the HyperX Methods Documentation and also include the corresponding references at the end of the section.
Excel spreadsheets containing all intermediate data used to calculate the margins of safety for each zone and for each failure criteria.
In the example shown below, the intracell dimpling data is given for a single zone. Each row represents a single load case, while each column represents a data value used in the margin calculation.
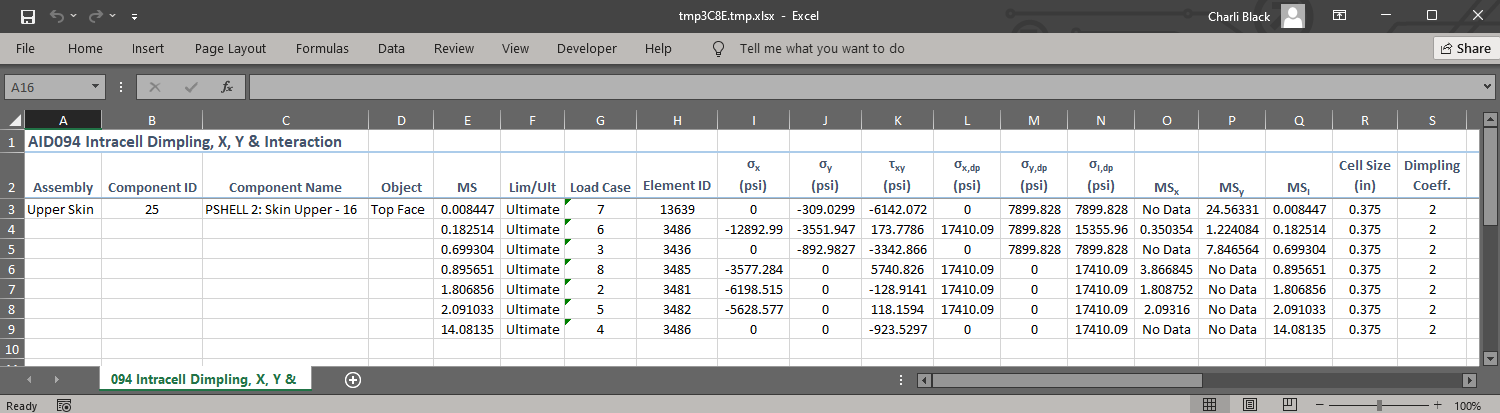
Analysis detail report exported for a single zone for intracell dimpling. All data values used to calculate the margins shown in Column E are reported for each load case.
The intent is for users to, in conjunction with methods documentation, directly back-calculate the margin results. This enhances user understanding and potential error tracking as well as provides additional data to supplement in-house reports.
Loads corresponding to discretely modeled fasteners are exposed by these reports.
HyperX joint capability automates the analysis and sizing of FEM joints, a process which is inherently understood to be tedious and complex – as a single model can contain thousands of joints and each joint must also account for the sizing of the joined members as well as the mechanism. Joint loads reports serve to expose a crucial part of this process – in which the loads corresponding to discretely modeled fasteners are transformed from FEM coordinates to HyperX coordinates. The data exposed by these reports is particularly useful for comparing fastener bearing forces, including bearing bypass, with post-processing tools and supplementing fastener-specific reports.
Contact Us
This site is protected by reCAPTCHA and the Google Privacy Policy and Terms of Service apply.