Laminates
Laminate optimization is a core part of HyperX’s composite capability. This includes generation of producible laminate families and tools for performing design studies to find a balance between weight and producibility.
Capability Pages
Introduction
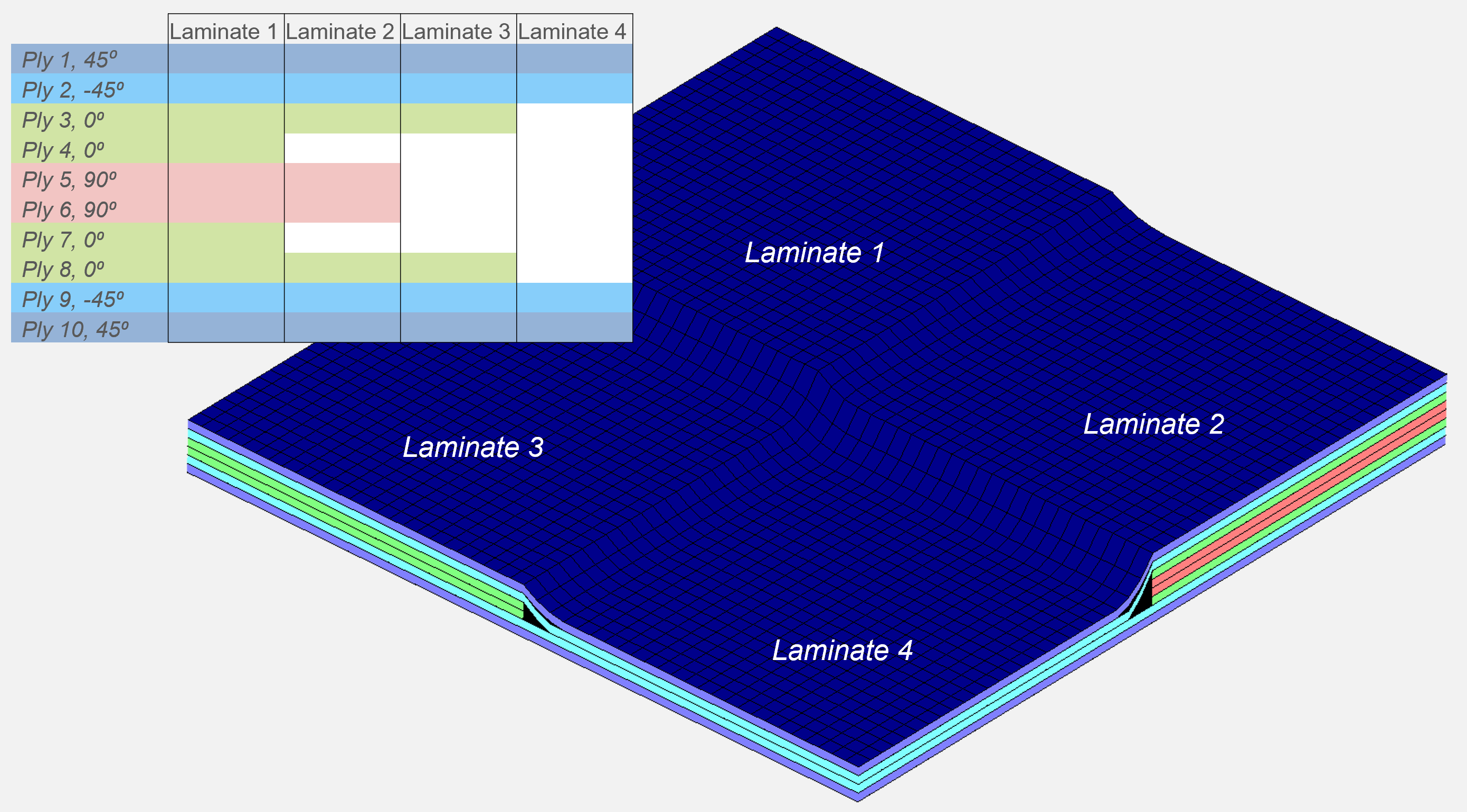
Generate Laminate Families
Generated families have stacking sequences and ply counts that are tuned to provide low weight and manufacturable solutions for specific zones or structures.
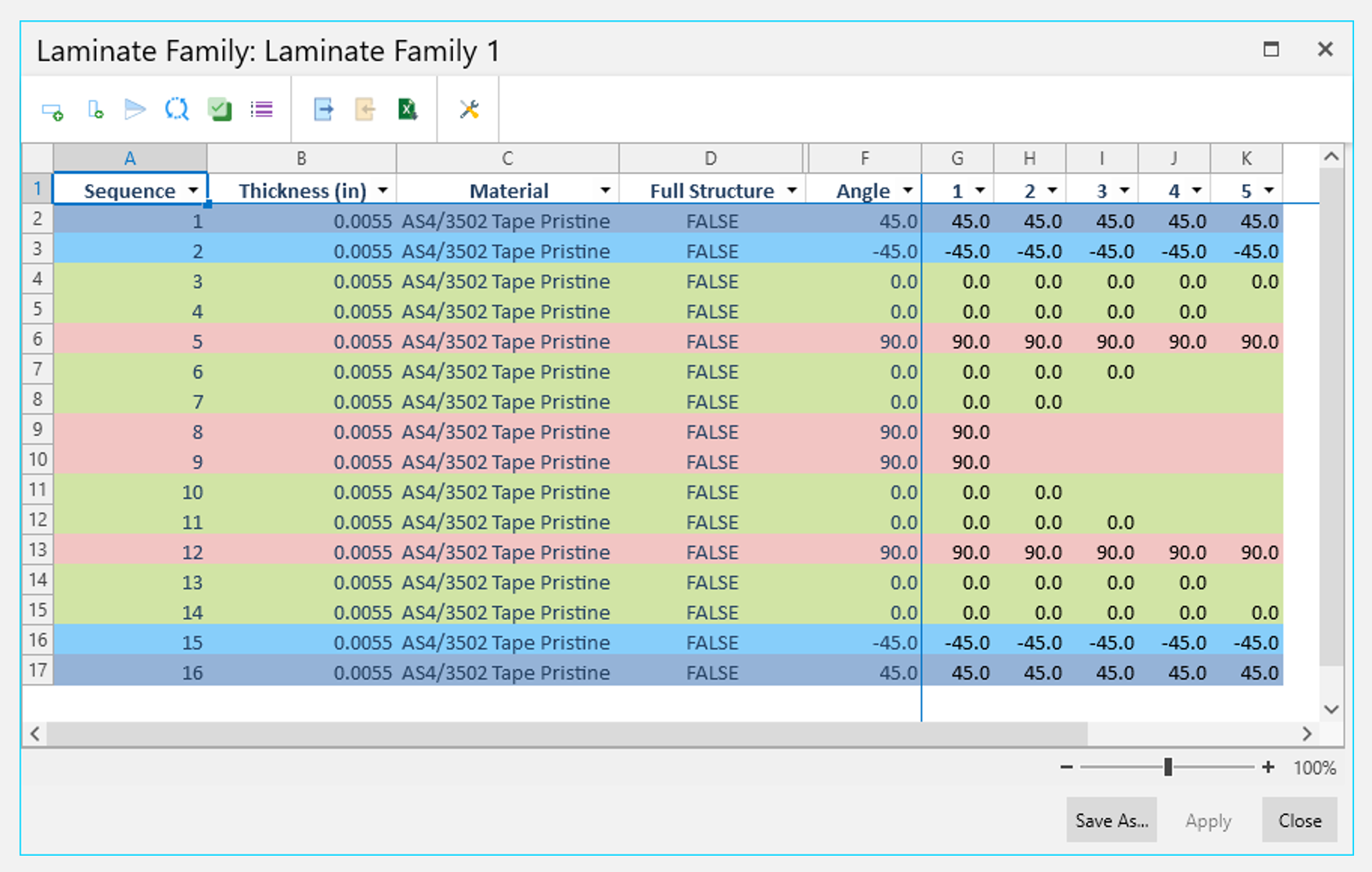
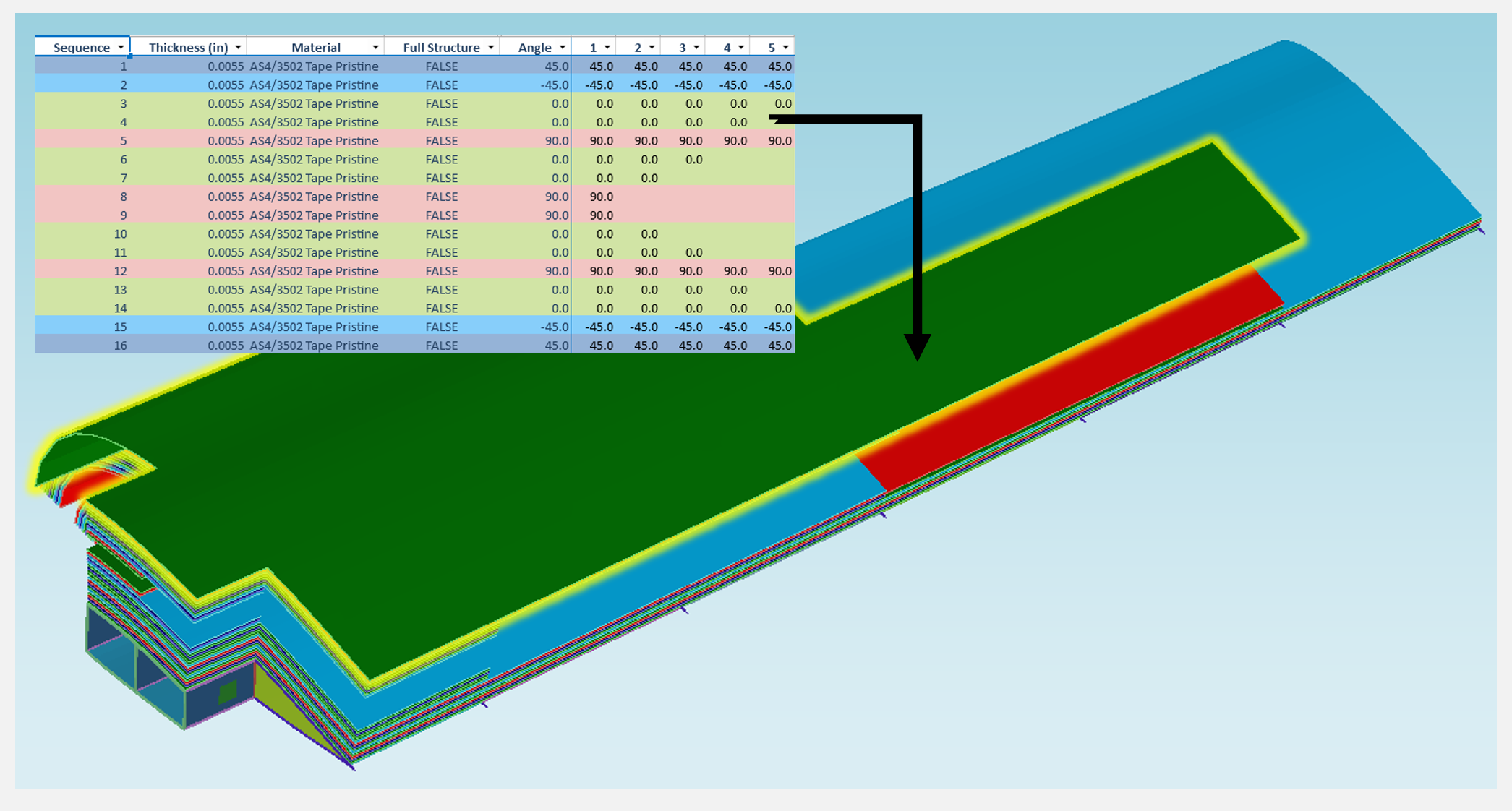
Laminate families are frequently used in composite aerospace structures due to their ability to produce manufacturable designs as well as simplify the design space during sizing. They consist of two parts: a Main Stacking Sequence (MSS) and the laminate family members. Laminates in a family are all a subset of MSS, making them highly compatible with one another when they are used to generate plies for manufacturing. HyperX has significant infrastructure to generate, import, manage, and size Laminate Families.
The primary drawback of sizing with laminate families is that they can result in higher weight than a “free” sizing, where each zone in a structure can choose a laminate that has been developed specifically for the loads in that zone. HyperX addresses this shortcoming generating a Master Stacking Sequence (MSS) that works well for all zones in a structure. This is done by aggregating optimum designs for each zone and generating a MSS that will produce a good sizing result for each zone.
HyperX has several different algorithms for MSS generation to handle different panel concepts (stiffened vs unstiffened) as well as different sizing modes. The MSS generation can incorporate layup rules, ply percentage limits, and fabrication rules such as OML and IML plies. Additionally, the MSS can be manually customized after it has been generated.
HyperX has a variety of options for selecting ply drop patterns within a family. This determines the order in which plies are dropped from the MSS, which in turn impacts the ply stacking of the laminates in the family. These drop patterns also respect user defined layup rules, ply percentage limits, and fabrication rules such as OML and IML full structure plies. HyperX allows for many families to be generated from the same MSS with different drop patterns and provides a tool to help the user determine which drop pattern is best for their application.
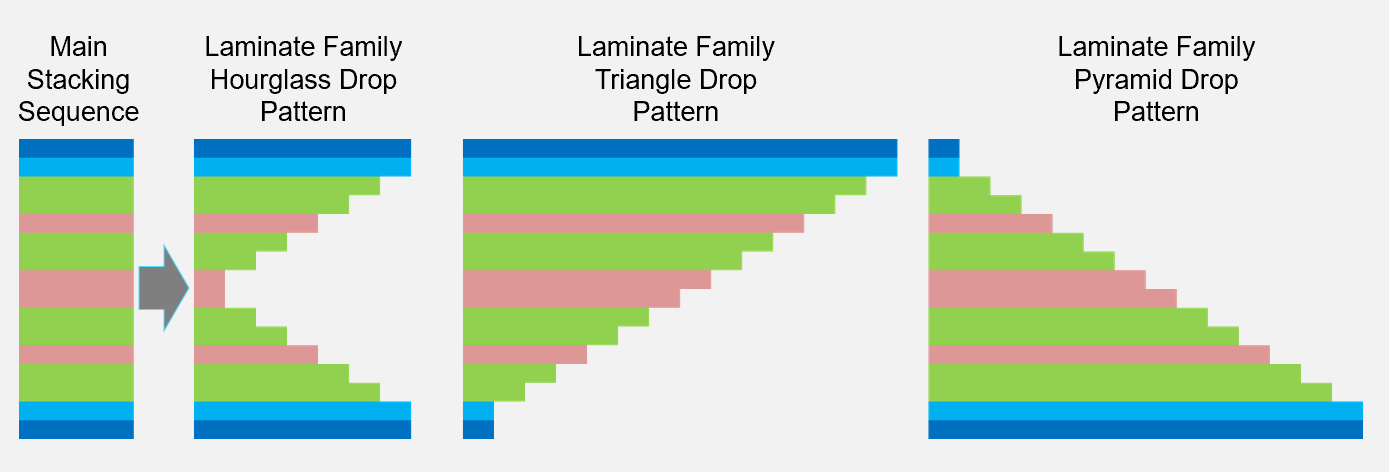
Existing families can be imported to HyperX and used for composite optimization.
Users who already have laminate families defined in spreadsheets can import existing laminate families for sizing. Laminate families might be required for a project due to constraints such as existing laminate test data, stacking sequence rules, etc. In this scenario the entire family definition can be imported, including sequence angles and material definition. Mixed materials are permitted in user-imported laminate families.
Ply angle (0⁰,45⁰,90⁰) percentage limits in laminate optimization influence both weight and producibility. HyperX’s design study tool is used to examine the trends.
The percentage of 0⁰, 45⁰, 90⁰ ply angles allowed in laminate optimization has an impact on both weight and producibility. At one extreme these percentages can be allowed to vary from 0% to 100% (black triangle in the design space below). In this scenario optimized laminates will have very low weight but may have a lot of variability in ply angle composition. At the other extreme the ply percentages can have very narrow bounds, essentially collapsing the design space into a single point. In this scenario optimized laminates will be highly compatible with one another (and therefore producible), but may have a significant weight penalty. It is necessary to find a compromise between these two extremes that is both light weight and producible.
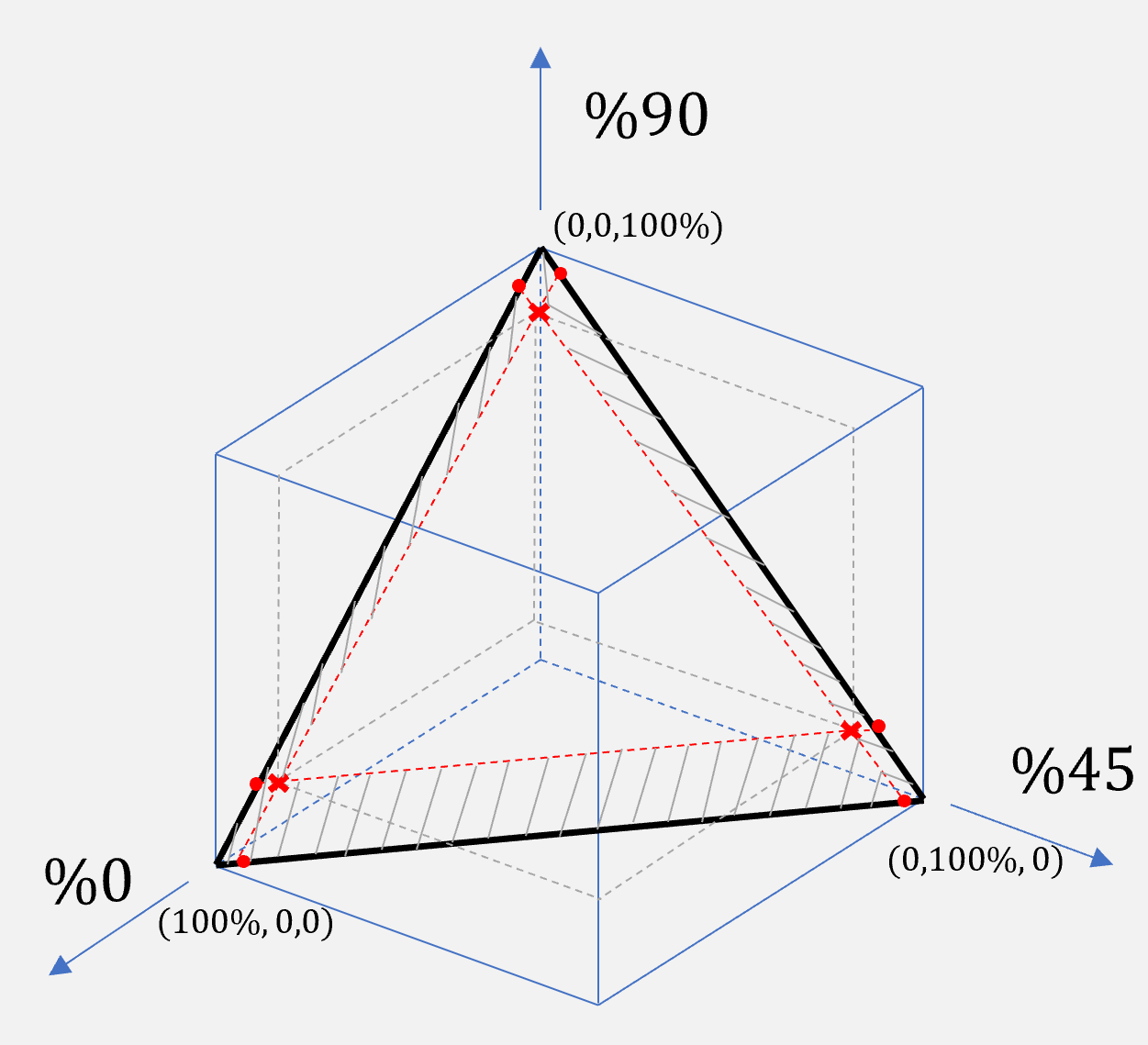
HyperX has a design study tool that allows the user to quickly examine a large number of ply minimum angle percentage bounds on a structure. HyperX will perform laminate optimization on every zone in a structure for a specified list of minimum ply angle percentages for each orientation. The weight and producibility of each combination is recorded and plotted. The plot identifies the angle percent limits on the Pareto front, which indicates the combinations with the best possible weight for a given producibility metric value. This helps the user quickly select new minimum ply angle percent limits that are best suited for their structure.
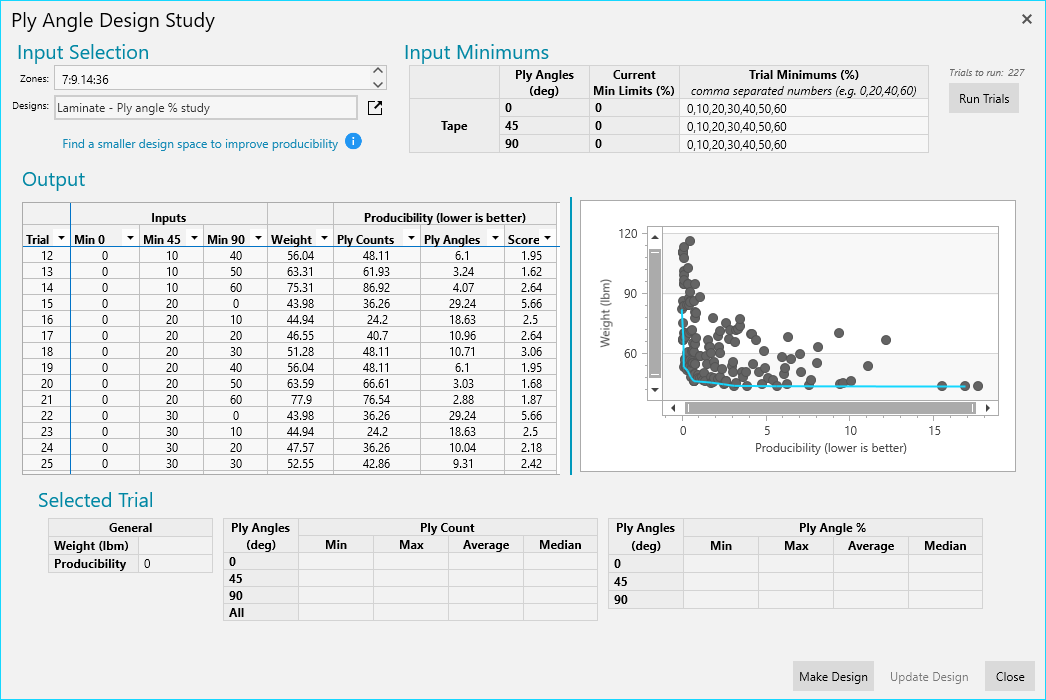
HyperX’s laminate family design study tool is used to analyze weight and manufacturability trends resulting from different drop patterns, ply shapes and Main Stacking Sequences (MSS).
This design study tool pairs with HyperX’s ability to generate a large number of candidate laminate families. The tool cycles through each laminate family and sizes zones to generate plies. The weight and manufacturability corresponding to each family is stored for the user to study. Manufacturability of plies is assessed from overall ply shape, number of plies, number of ply cuts, and orientation of fibers relative to the ply edges, based on ply scoring metrics described later.
The laminate family design study form provides a report of the metrics described above for each laminate family as well as an interactive plot of the weight vs producibility metric of each family. The plot identifies the families on the Pareto front, which indicates the families with the best possible weight for a given producibility metric value. This allows for a small number of high-performing families to be quickly identified out of 10s or 100s of candidate families. Once the user has selected their preferred family it can easily be on-ramped in the standard HyperX sizing workflow.
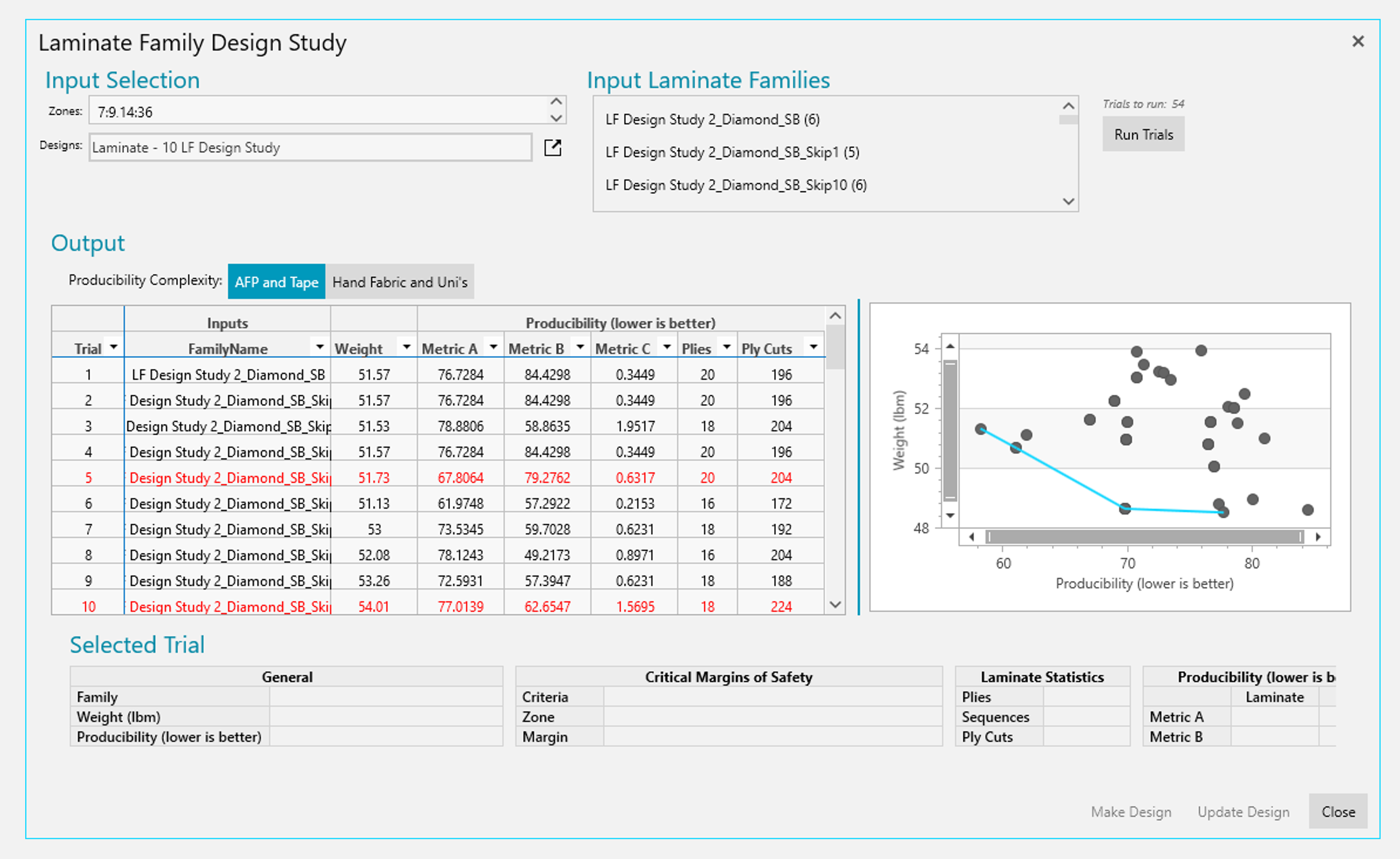
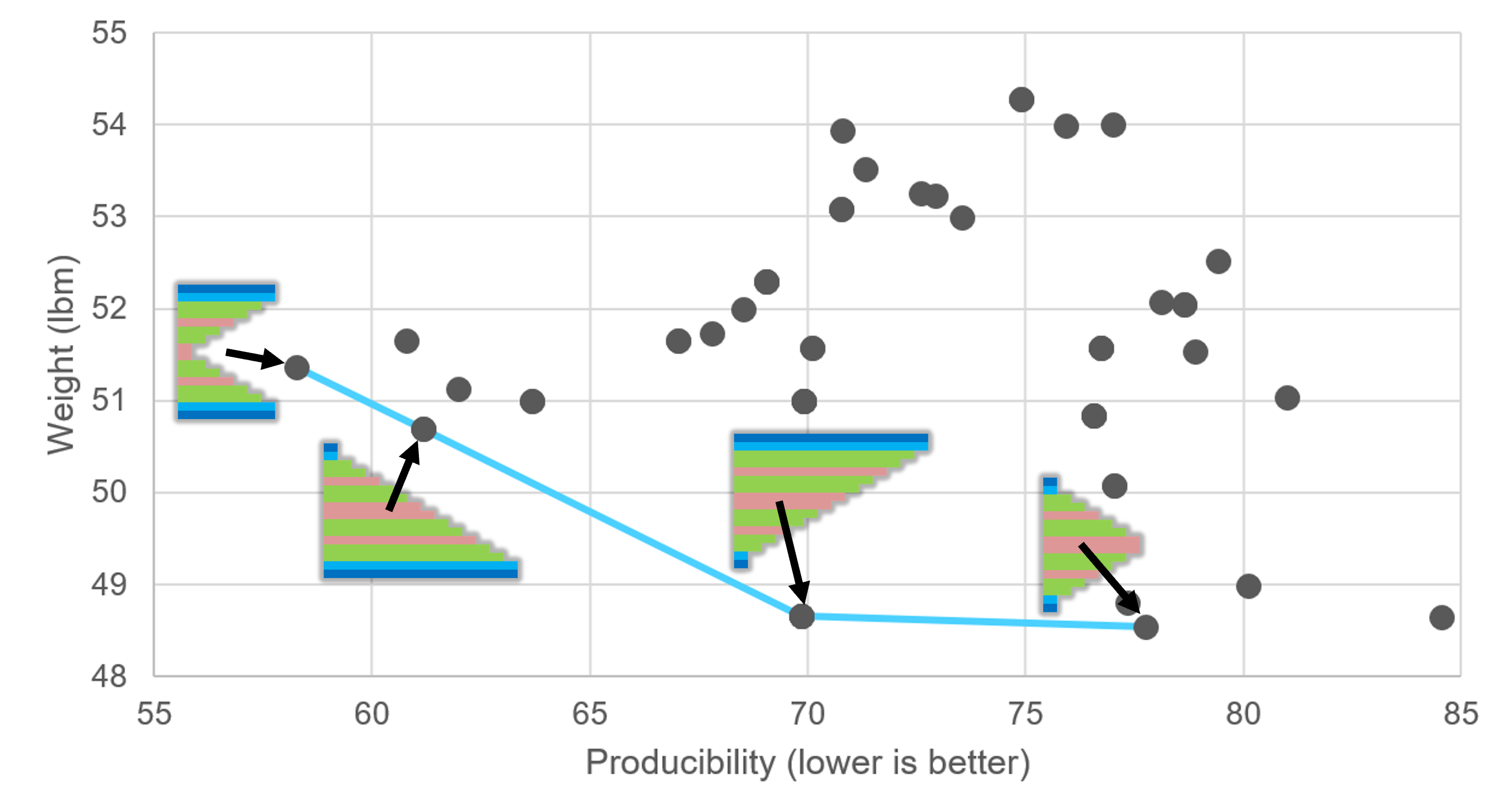
Contact Us
This site is protected by reCAPTCHA and the Google Privacy Policy and Terms of Service apply.