Analysis Consistency
A certification process requires analysis consistency. HyperX provides myriad of tools in a single framework to ensure consistency both within a team environment and throughout the entirety of a design cycle.
Capability Pages
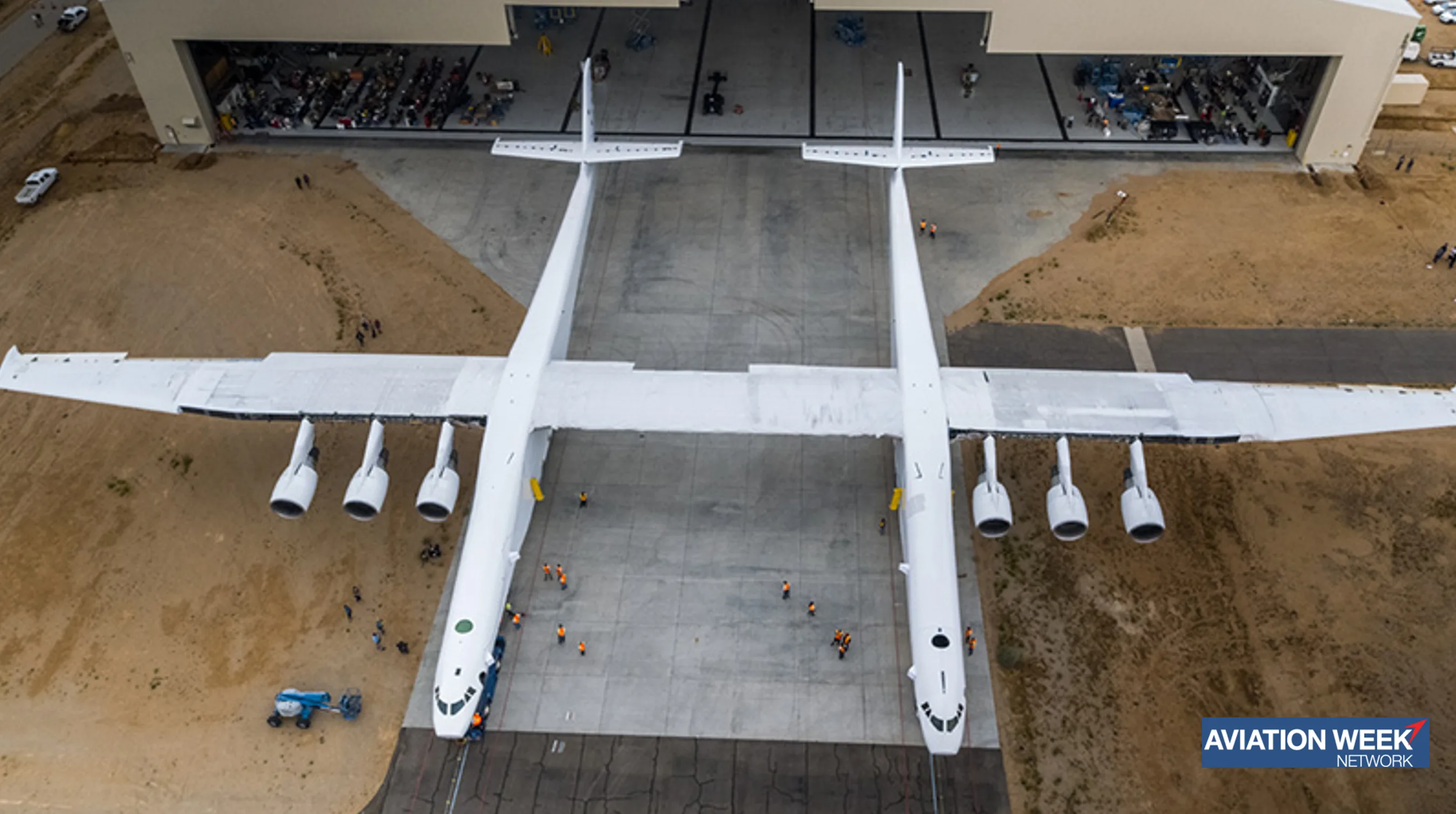
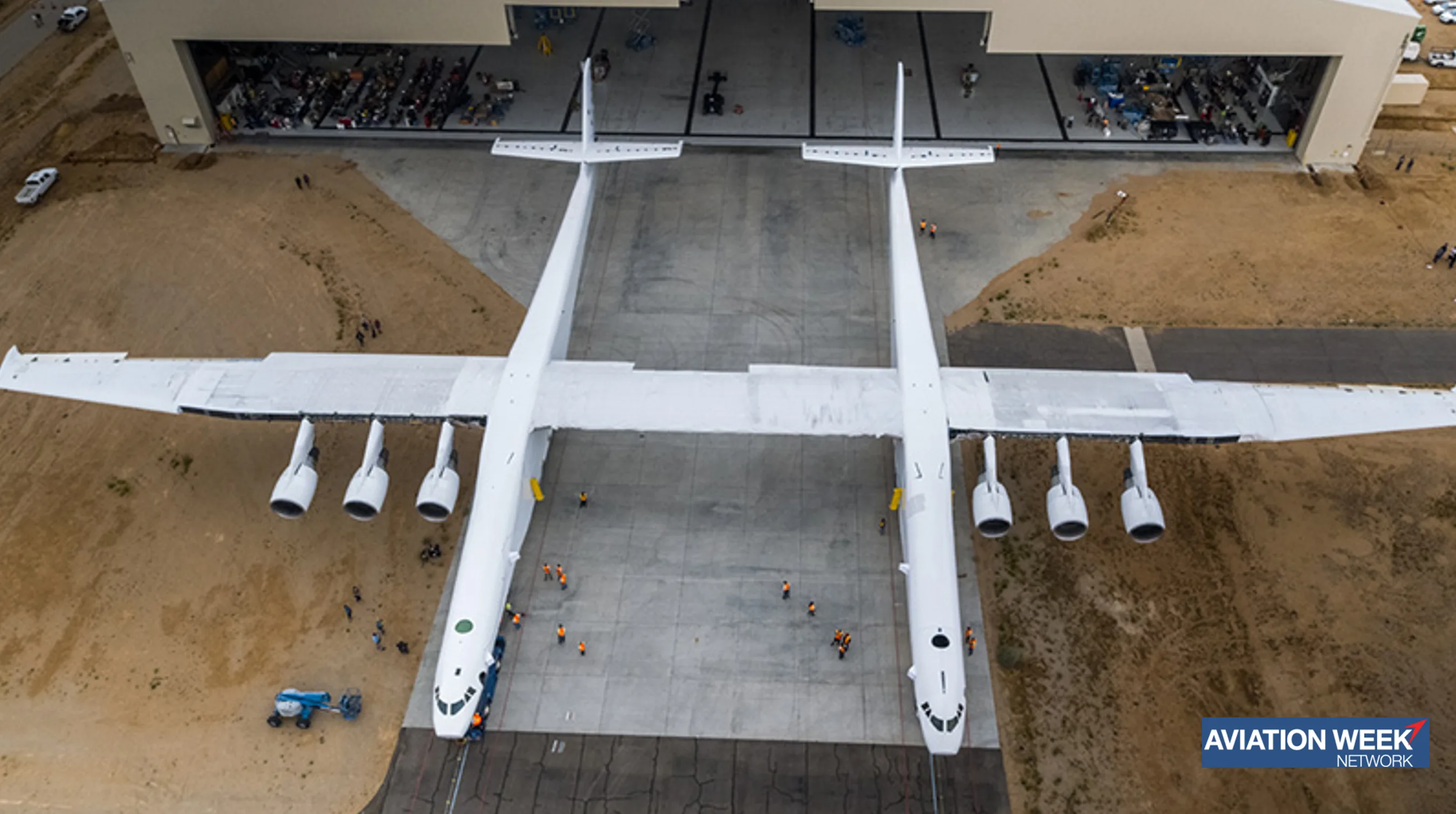
See Relevant News Article:
Aviation Week – NASA Project Seeks Faster Certification of Composites
Use HyperX in all phases of vehicle design to maintain consistency in workflow and implemented analysis.
One of the most powerful benefits of HyperX is not any one feature – it is the ability to provide value at any stage of the design cycle. A HyperX database contains material systems, analysis policy, and design space definitions. Employing this database from the conceptual phase of design ensures it can easily be adapted to support more detailed analysis and reporting phases – thus guaranteeing consistency both in workflow and in the details baked-in to the design.
A conceptual design phase likely consists of a simple, coarsely-meshed FEM. At this stage, HyperX is used to:
- Establish design trends
- Perform trade studies between various design concepts
- Determine appropriate material systems
The sizing and analysis capabilities within HyperX are used to make preliminary design decisions, which then inform PDR reports and continued refinement of the FEM.
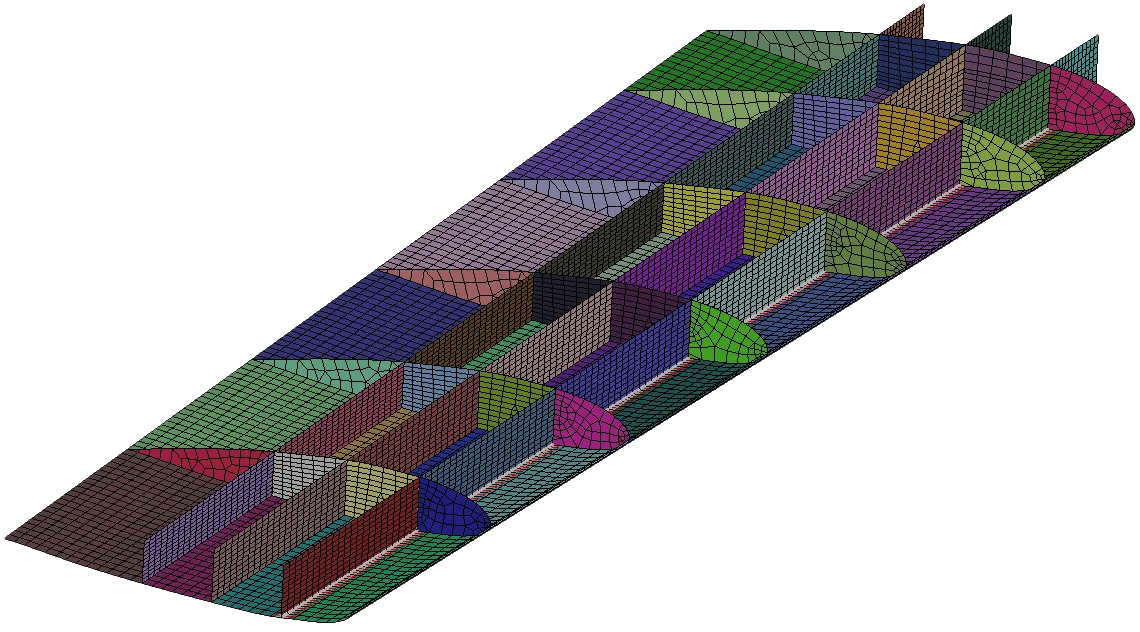
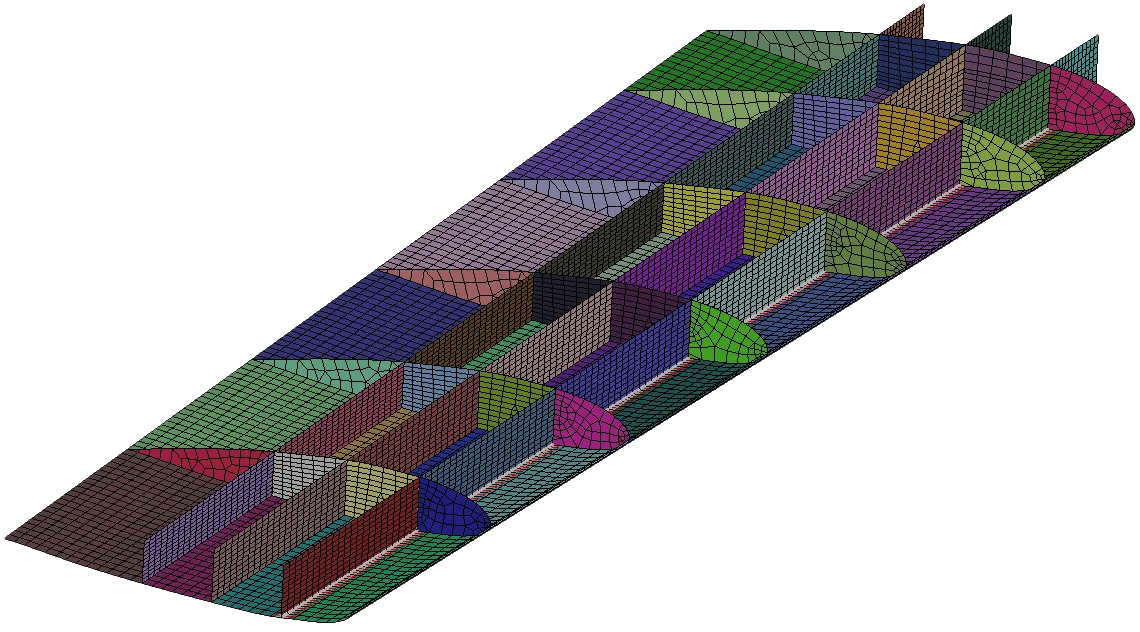
As the design cycle proceeds to CDR and part release, the focus shifts to showing positive margin, writing stress reports, generating plots, etc. Here, HyperX is used to:
- Analyze discretely meshed stiffener sections of stiffened panels
- Write margins to mature design features such as core ramp downs and discretely modeled fasteners
- Sequence zone-by-zone laminate results into a global ply layup schedule that can be transferred to a CAD/design model
- Uncover problem-areas and identify solutions with minimal impact to the rest of the model
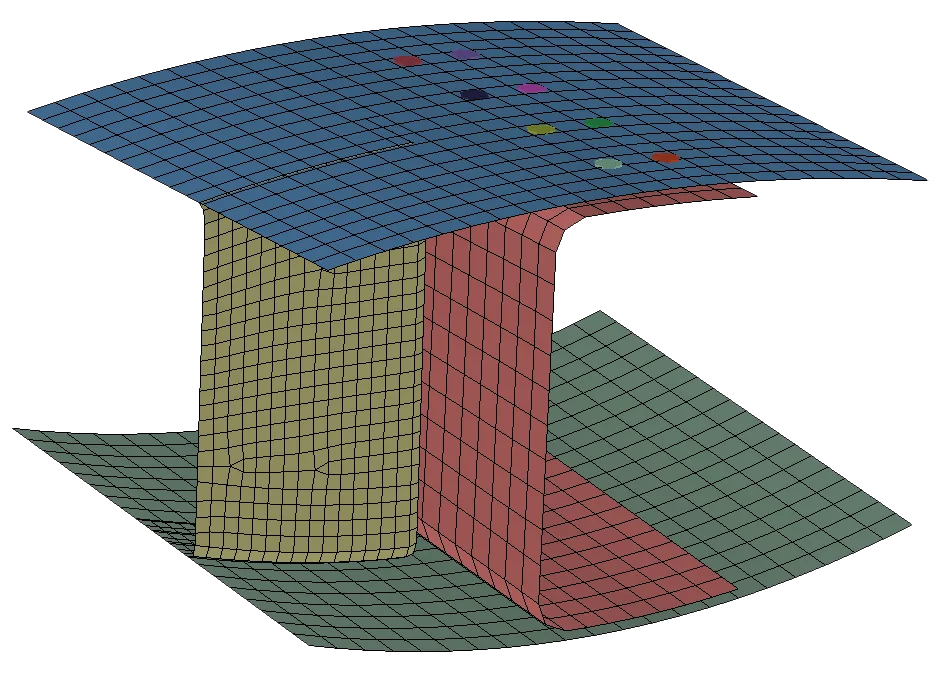
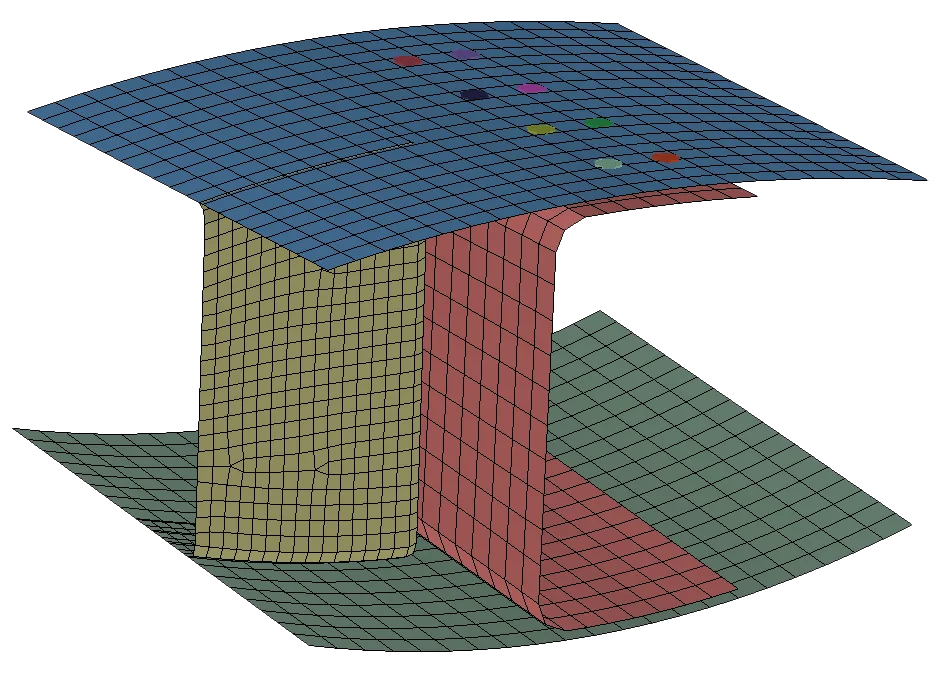
The goal is for analysis entities to be modeled as closely to their “as manufactured” parts as possible. HyperX readily supports this level of analysis and modelling technique. It is important to mention again that while doing so, HyperX will employ the same material systems, database defaults, and analysis assumptions that were implemented at the beginning of the design cycle (as are relevant). This increased level of consistency throughout all design phases is of upmost value to the certification process.
Design cycle consistency is further illustrated by the HyperX stiffened-panel sizing process – outlined in the table below.
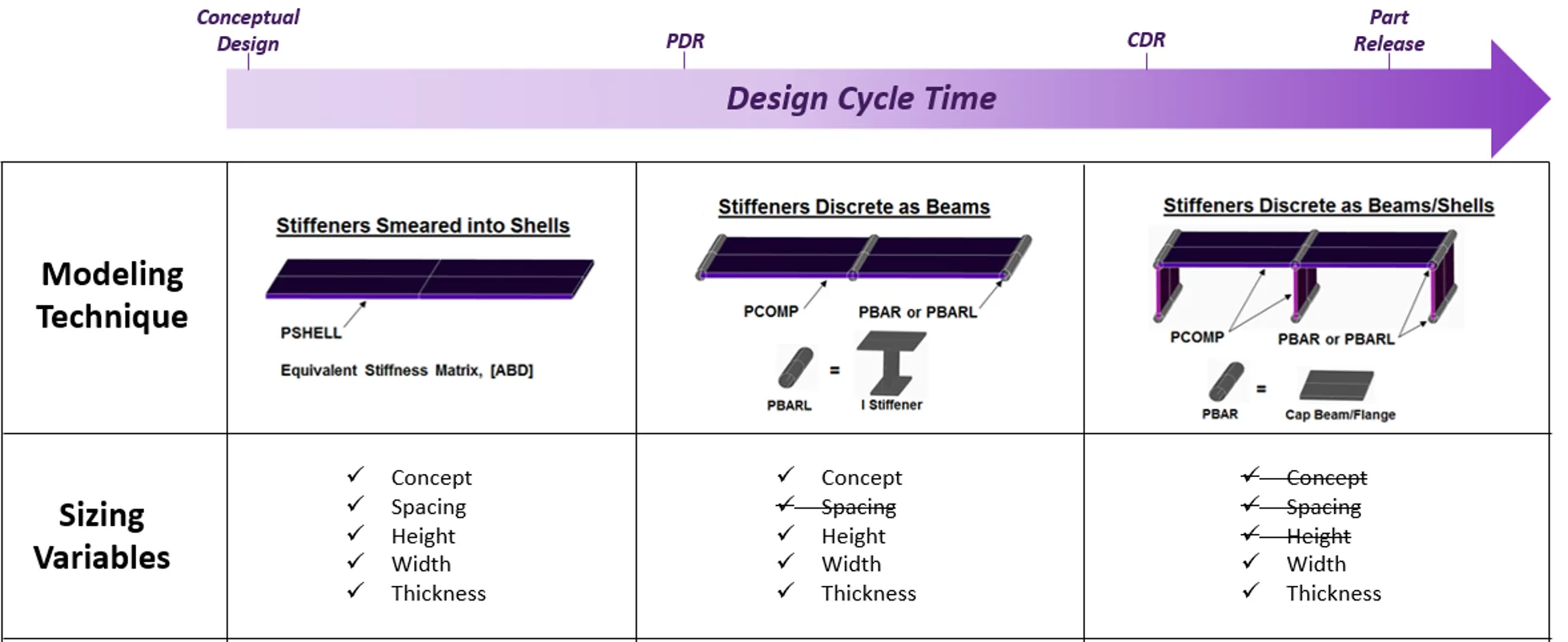
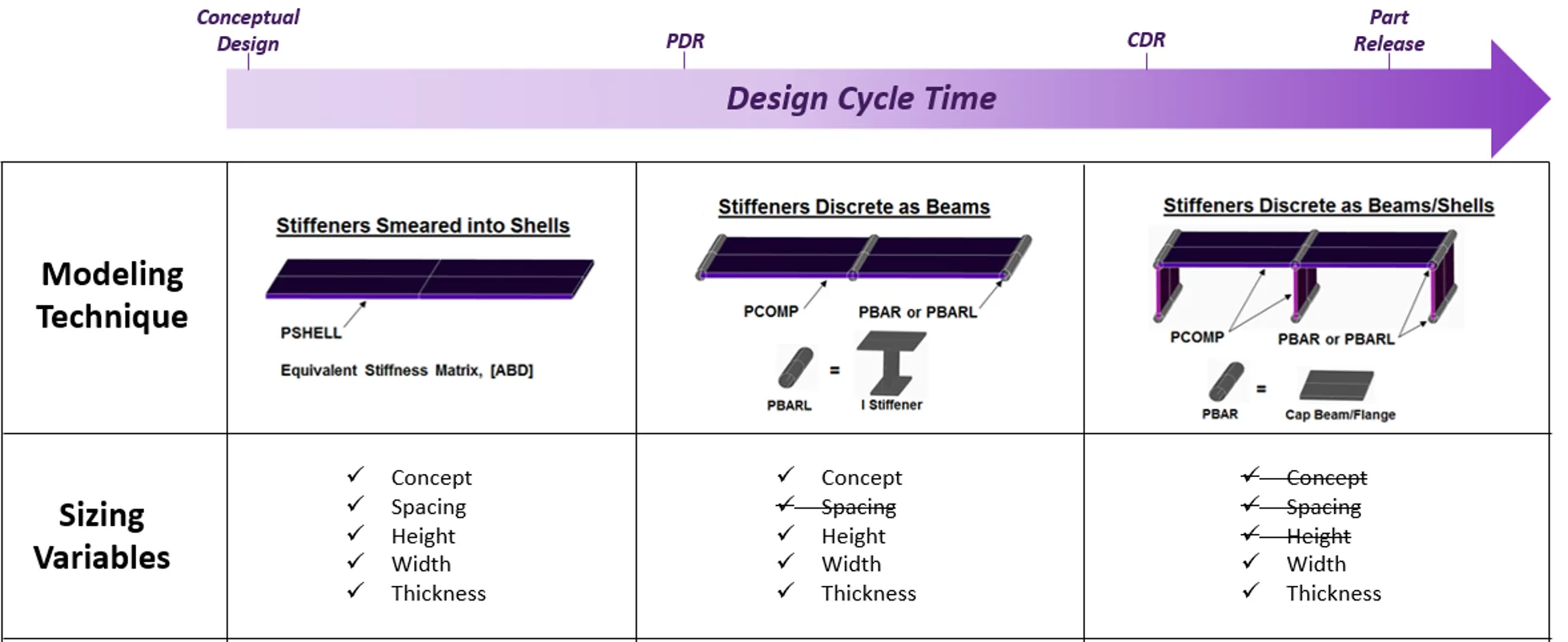
In short, as design decisions are made and the FEM is matured, HyperX maintains value in margin writing – actually increasing details in each step. While this changes the scope of the analysis, this does not change the HyperX workflow on the user-side. Stiffened panels within HyperX are always performed consistently and accurately, using the same material data and analysis methods in each phase.
Maintain and deploy verified and test validated material and fastener properties required for certification.
Verifying and validating material properties is required for certification. What’s more, these approved materials must be incorporated throughout all aspects of design. HyperX databases provide an environment for programs to store all structural material data – whether obtained from public sources or internal test programs. All engineers have access to this data and can use it in analysis and sizing.
All material forms are compatible with Excel, allowing for quick import and edits, as well for export to supplement certification reports.
Commonly used metal material and fastener and rivet types used in the aerospace industry have already been pre-defined with vetted, public-source data. These definitions come “out of the box” and can be used consistently by the engineering team the second HyperX is installed.
Composite material stress/strain allowables require in-situ testing and data calibration. HyperX provides ply and laminate-based approaches to establishing strength, along with multiple ways to define correction factors.
Save all project level data and method preferences in a HyperX Database Template. Use these templates as a starting place for all team members to ensure one source of truth for analysis and sizing.
Maintain consistency within a program or design cycle with Database Templates. A Database Template defines all analysis and design inputs required by the program. It is then saved and passed to all engineers as a common starting place for sizing.
Database Templates incorporate any combination of relevant database-level entities – including materials (all types), laminate definitions (including laminate families), fasteners and rivets, design space definitions, analysis methodology, and load processing techniques.
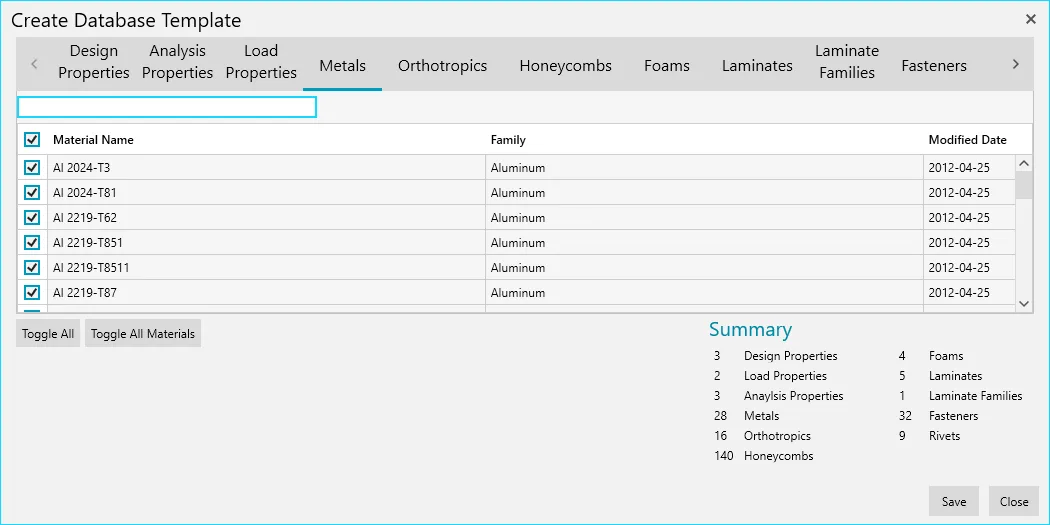
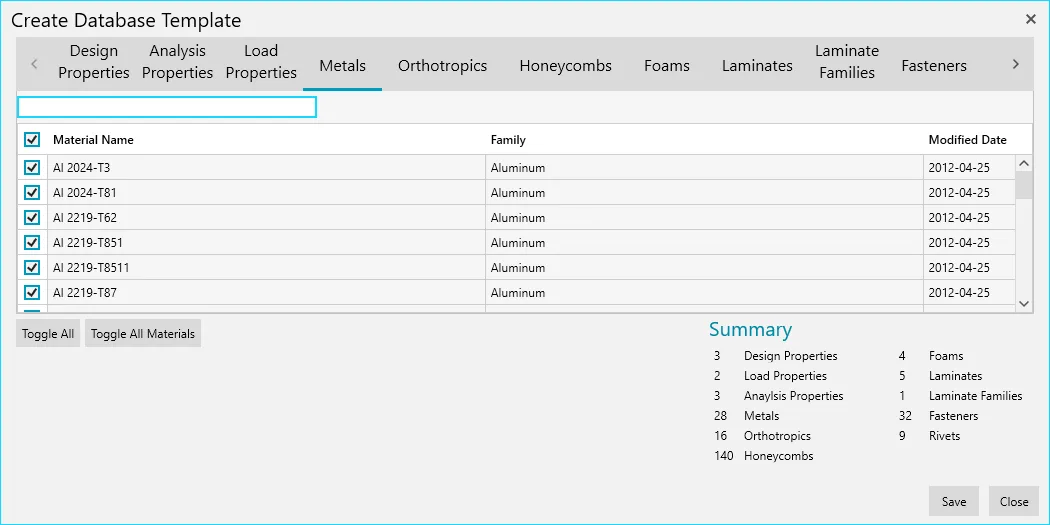
Example database template creation form, illustrating all possible HyperX entities that can be saved and enforced throughout a team of collaborating engineers.
All database-level defaults, which include analysis assumptions, safety factors, analysis temperatures, composite layup and fabrication rules, etc. are automatically saved as part of database templates.
Anything that is part of the template will be set to ‘read-only.’ This way, these properties and materials cannot be edited during design. This feature is particularly useful in providing confidence to program managers and reviewers.
Applying this level of consistency with database templates enhances the certification process by providing a single “source of truth” for all engineers to use for part design and reporting.
Enterprise Deployment
Maintain consistent material data, margin policy, load conditions and factors, across all separate engineer databases.
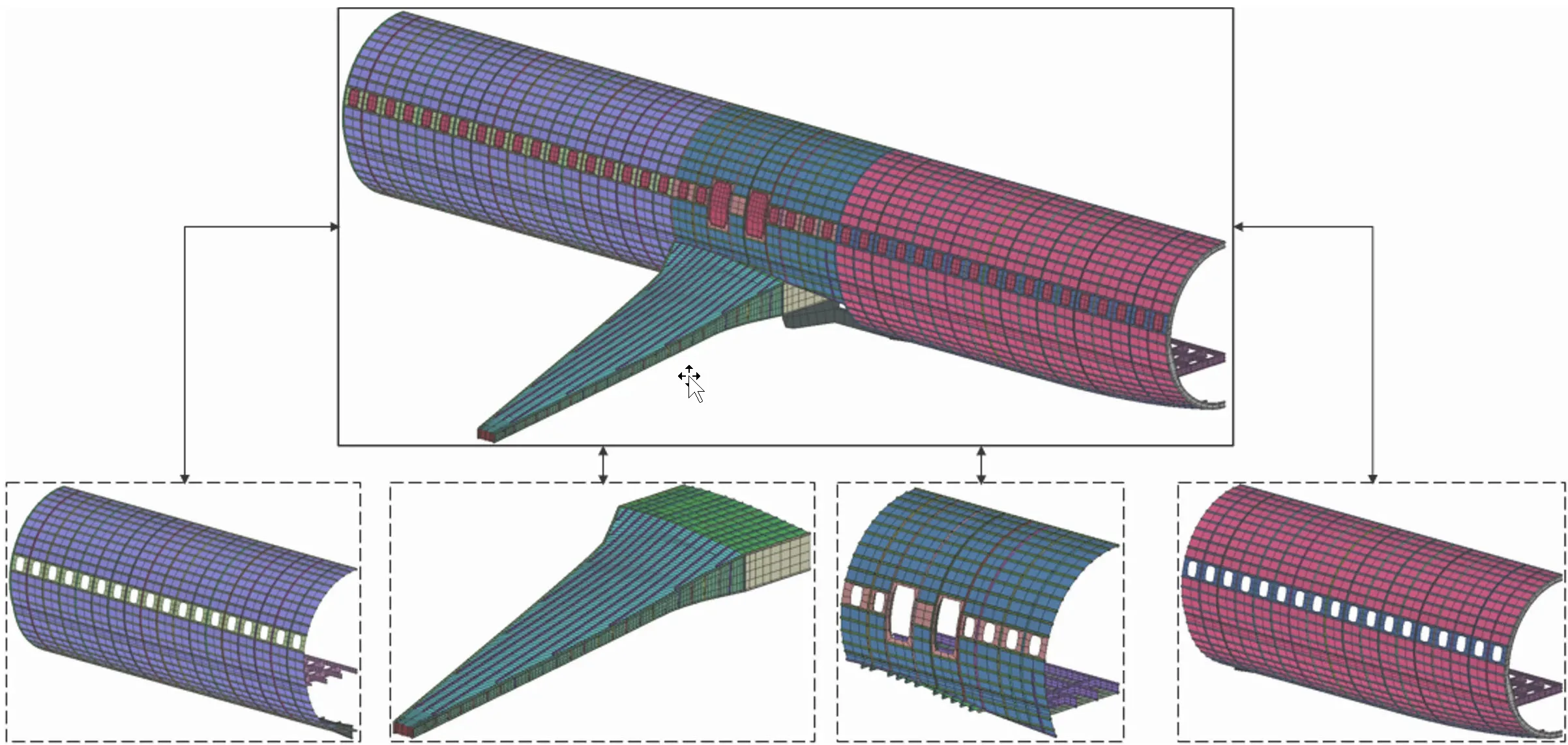
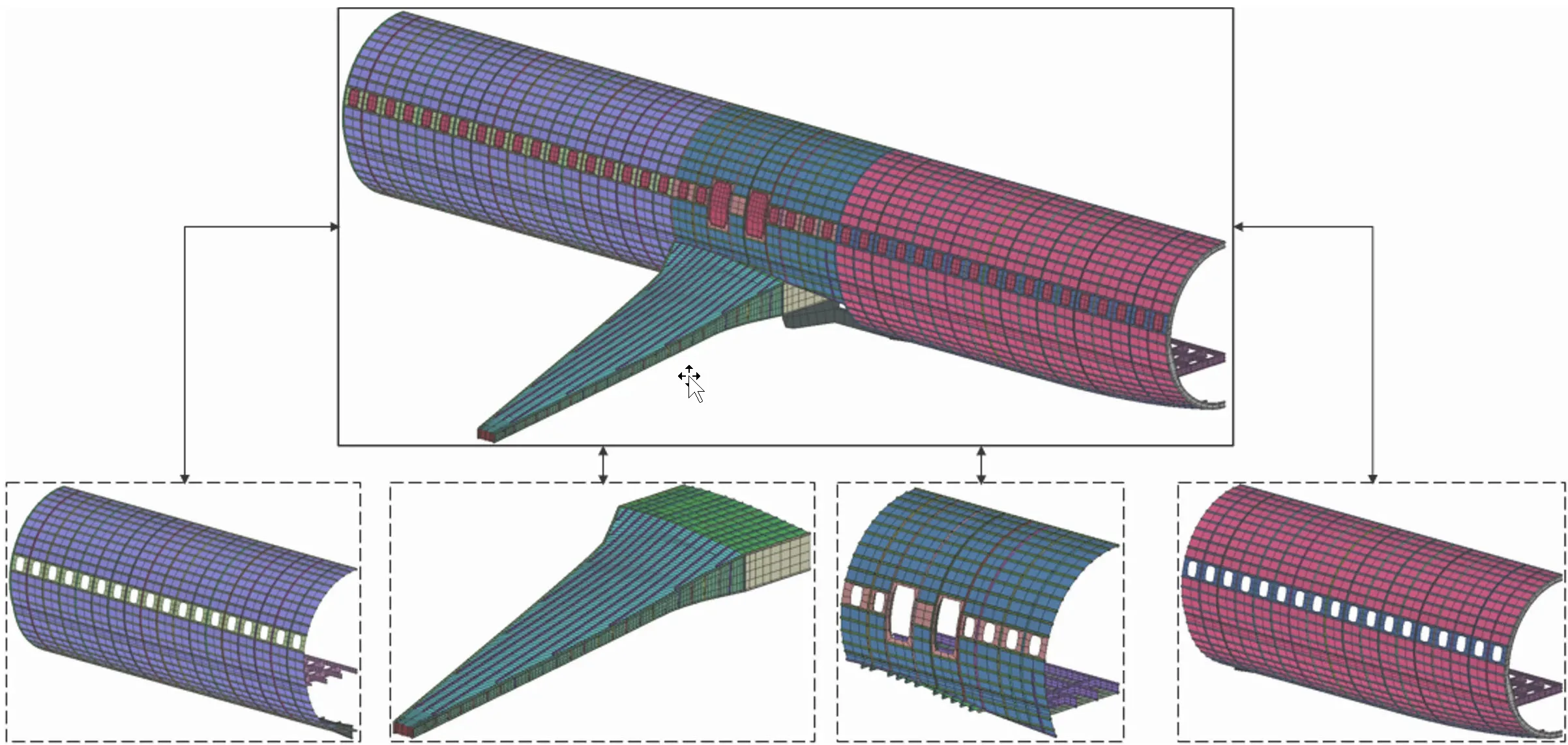
The Enterprise Workflow takes the ‘Database Template’ idea several steps further by providing automated tools to enforce consistent assumptions within multiple individual databases created from the same internal loads FEM. This not only puts program managers at ease, but also offers a convenient way to maintain the level of consistency required for certification reports.
Each engineer can independently size their structure within their own database while still respecting program-level data and requirements.
Once all structures have been sized, HyperX can automatically ‘roll’ the results from each engineer database back into the parent database. Standard company material data cannot be edited by individual engineers, but FEM setup data is allowed but without authorization. Reports are made during the roll back process for the Group lead that identify data that has been potentially improperly modified.
Contact Us
This site is protected by reCAPTCHA and the Google Privacy Policy and Terms of Service apply.