Trade Studies
Rapidly evaluate different architectural, material, panel, and joint concepts such as those identified below using HyperX’s three automated trade study tools, listed in order of importance:
Capability Pages
Introduction
HyperXpert
HyperXpert extends the typical HyperX workflow. Using a full factorial DOE-type approach, HyperXpert systematically varies all design variables, including cross-sectional dimensions, materials, and laminates across a part and organizes all possible (positive margin) designs in a plot for review. This allows you to quickly compare results, understand trends, and decide the “best” design for yourself. See HyperXpert
Dashboard
As engineers continue to search for lightweight structures, the most innovative will emerge from robust trade study optimization that tackles every variable, generates a number of alternative designs, and identifies substantial weight savings. The role of the dashboard is to preserve this generated data and to make the weight trends available to all. See The Dashboard
Laminate Family Design Study
This design study tool pairs with HyperX’s ability to generate a large number of candidate laminate families. The tool cycles through each laminate family and sizes zones to generate plies. The weight and manufacturability corresponding to each family is stored for the user to study. See Laminate Family Design Study
Material Trades
Composite Material Trades
- Tape or Fabric
- Thermoset or thermoplastic or resin infusion
- Intermediate modulus or high modulus
Metal Material Trades
- Aluminum or Titanium or high strength steel
- Thermal environment vs temperature dependent material properties
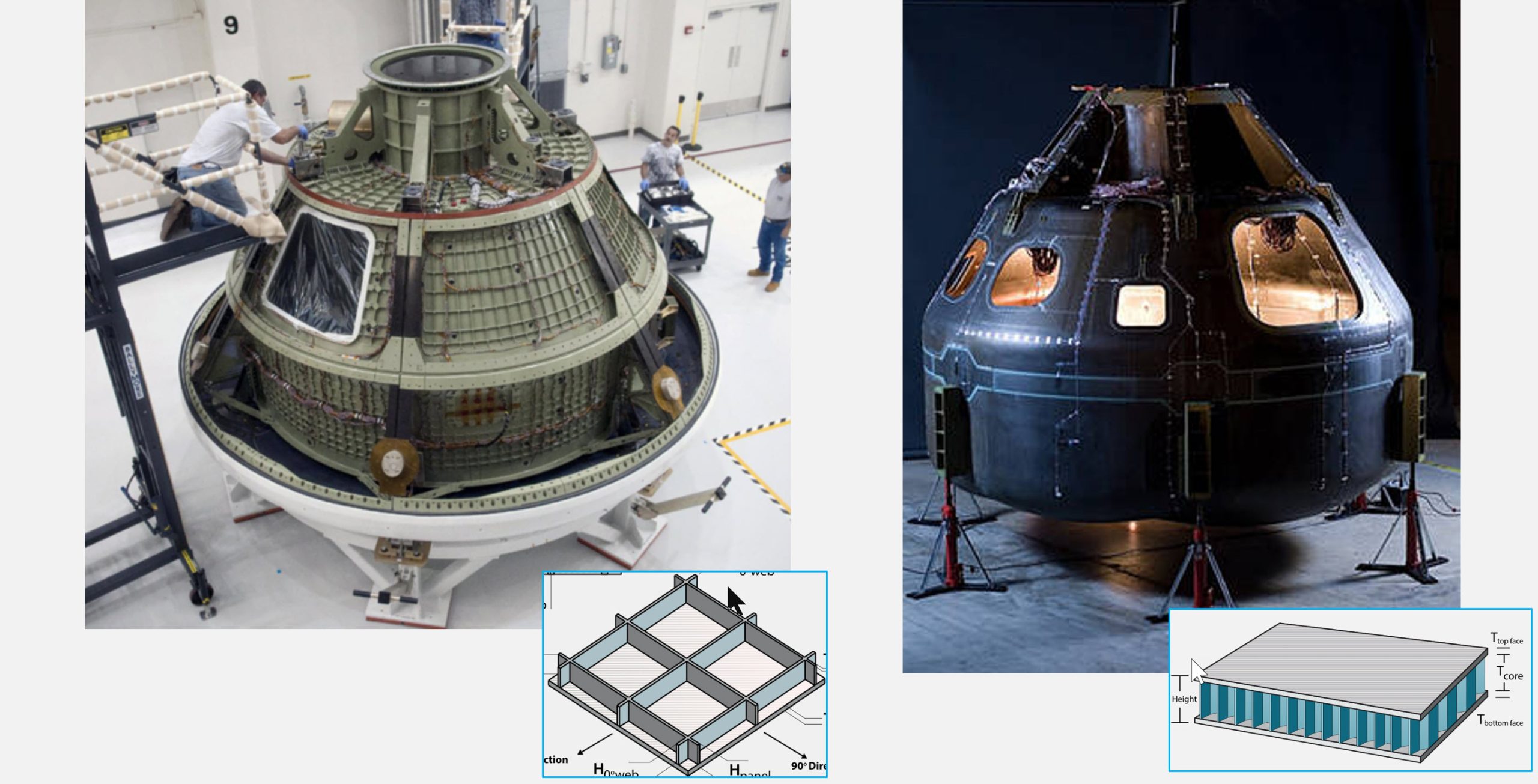
Machined metal stiffened orthogrid panel design (left) vs. composite sandwich design (right).
Designers are, as they say, spoiled for choice. In fact, the sheer number of materials available can be a bit daunting. Materials that are stiffness-driven, or dominated by the load in one direction are generally better candidates for carbon fiber composites. Structures that are loaded in two or more directions at the same time are probably better candidates for metal. Generally. Probably.
“You can’t really always know beforehand what material system is best for your application,” admits Craig Collier of Collier Research. “It has a lot to do with shape, and the loading of the structure.”
Your preconceived notions, he says, may be wrong: “We’ve seen that composites do bring down weight in many applications, but not in all applications.” He offers as an example his firm’s case study of the Orion spacecraft heat shield (images below) for the NASA Engineering Safety Council. When Collier’s HyperSizer software was used to explore the different material types, titanium turned out to be substantially lighter than carbon graphite composites.
See Relevant News Article: Digital Engineering – Lightweight material champions
Panel Concept Trades
- Uniaxial stiffened open Tee shape or closed section hat/omega shape
- Height and all cross-sectional dimensions of the shape
- Composite solid Laminate or honeycomb core sandwich
- Ply layup
- Metal integrally machined grid stiffened orthogrid or isogrid
- The spacing pattern and heights of the webs, pocket size of the skin, gauge thicknesses
Composite
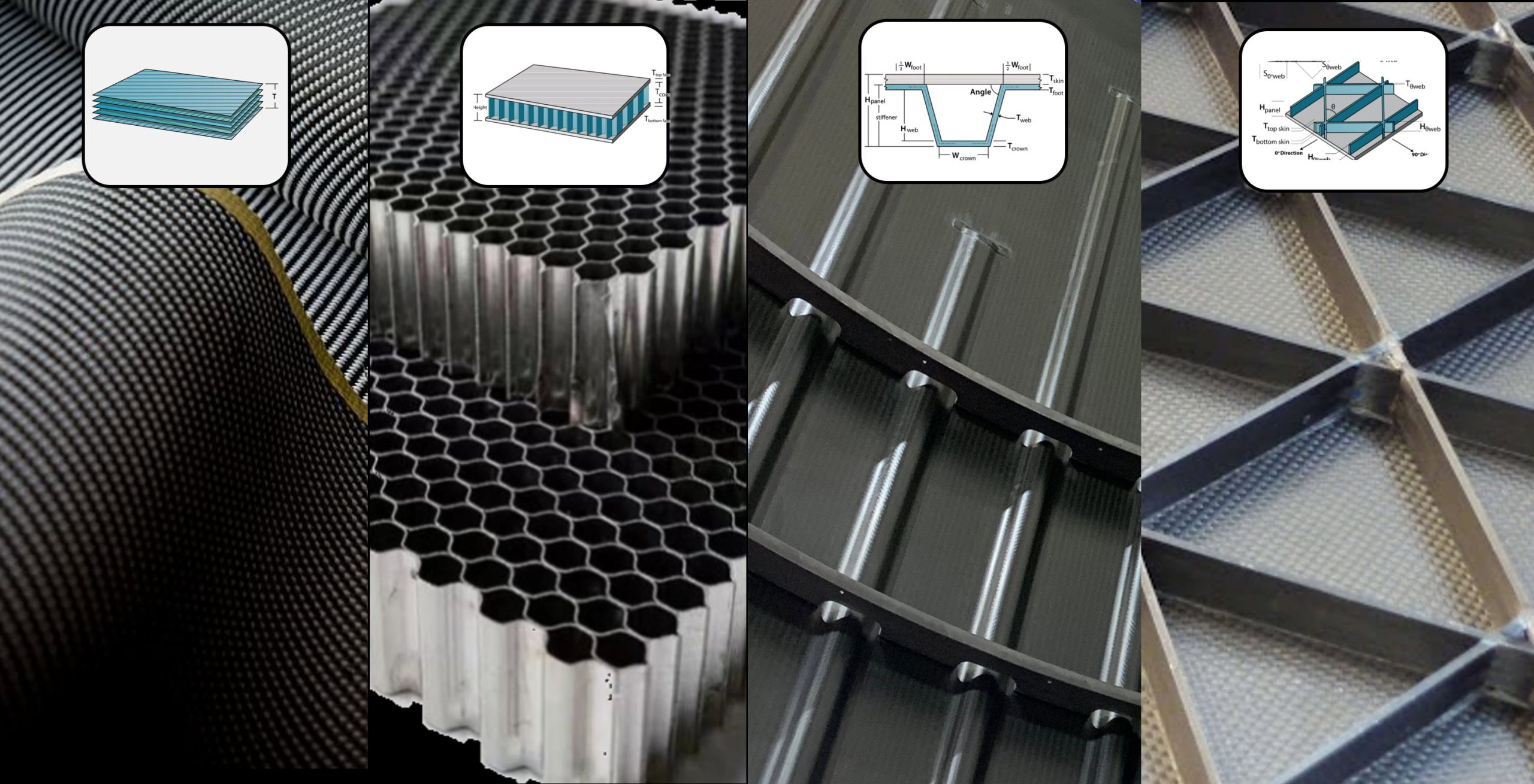
Metal Machined Grid Stiffened
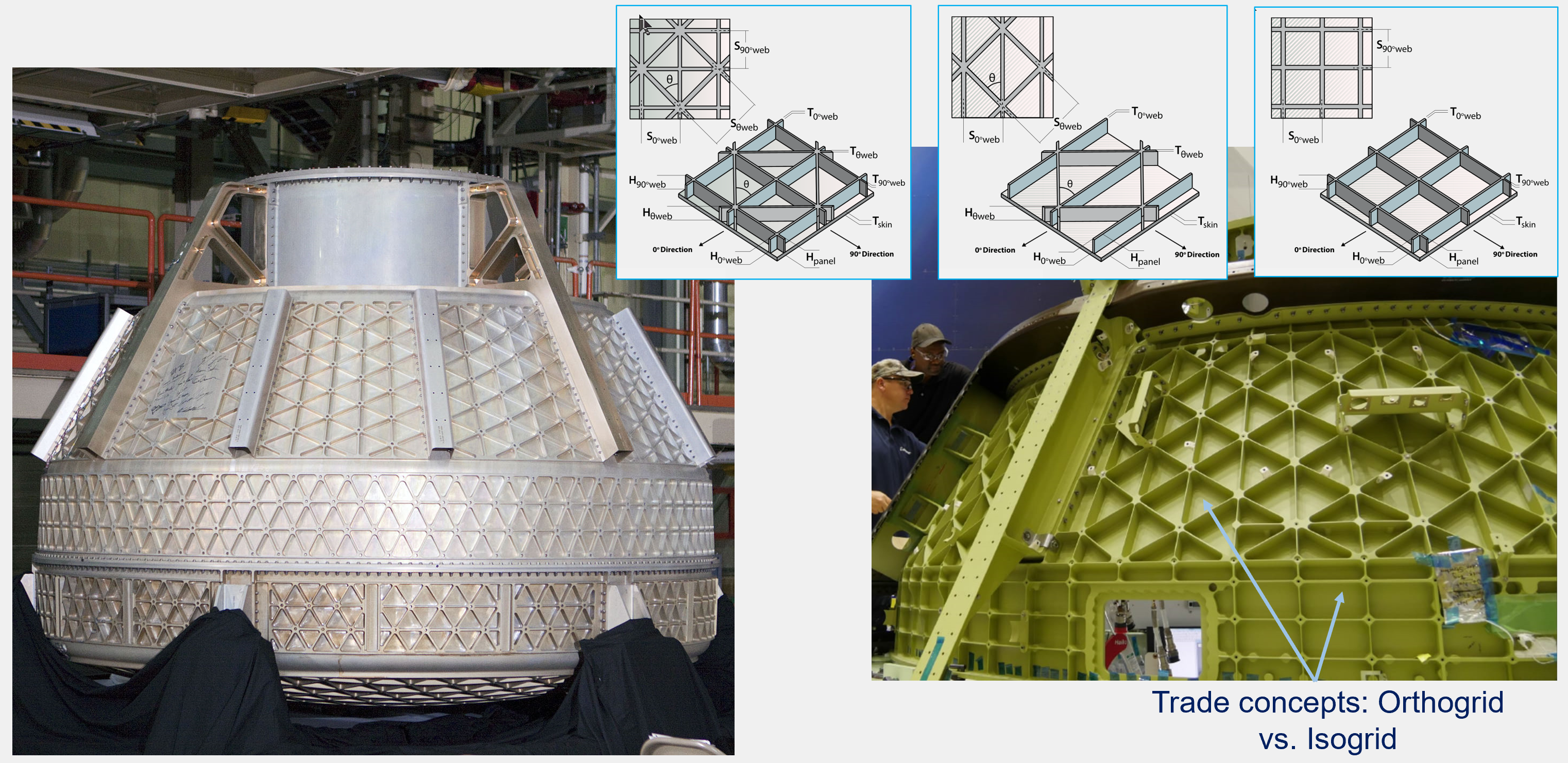
After conceptual design, there remains a multitude of more design decisions to make. A design decision should not be made independently as its choice will affect the performance of other design possibilities. A factorial combination of your chosen possibilities needs to be first established, and then using HyperX you are able to execute complete project evaluations of each unique combination rapidly without having to remesh your FEM. Performing these types of trades below is quickly and conveniently accomplished in the preliminary design phase.
Structural Layout Trades
- Wing rib spacing and fuselage frame spacing
- If stiffened panel: stiffener spacing
- If sandwich panel: core ramp and edge band
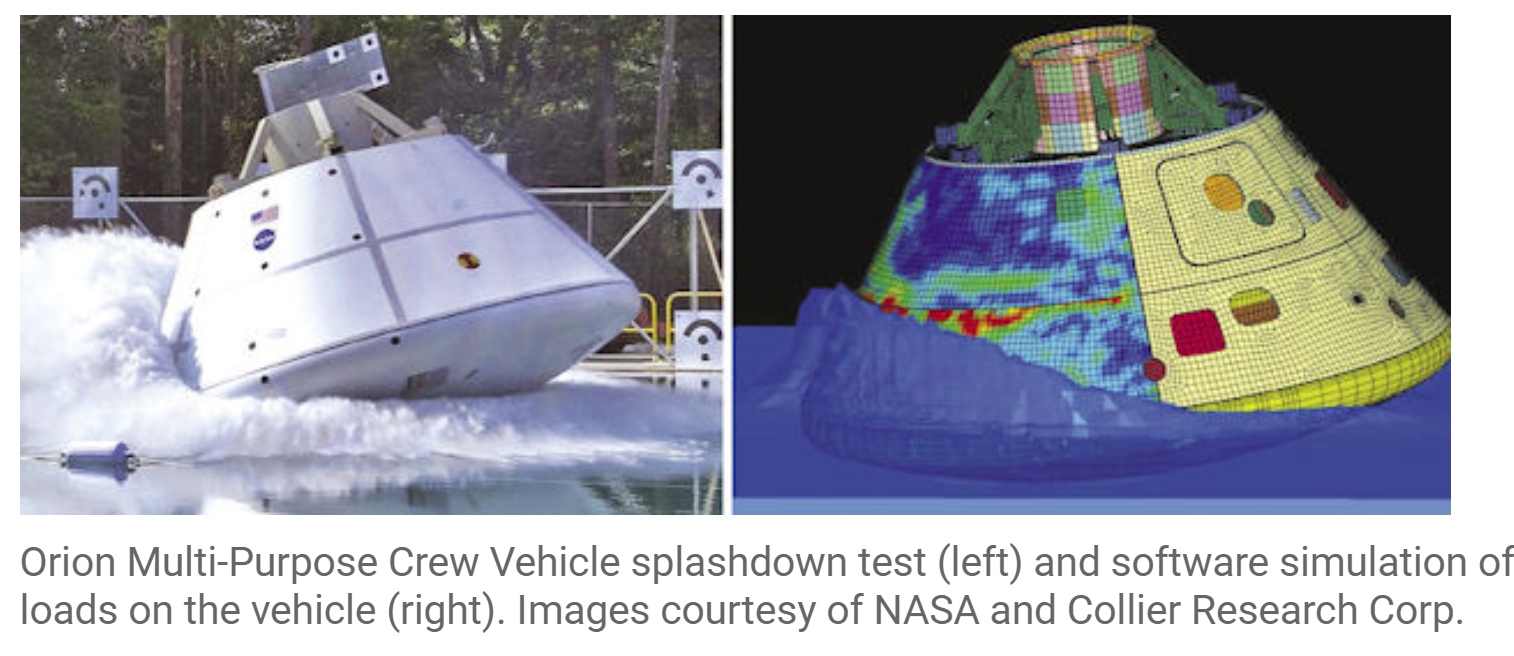
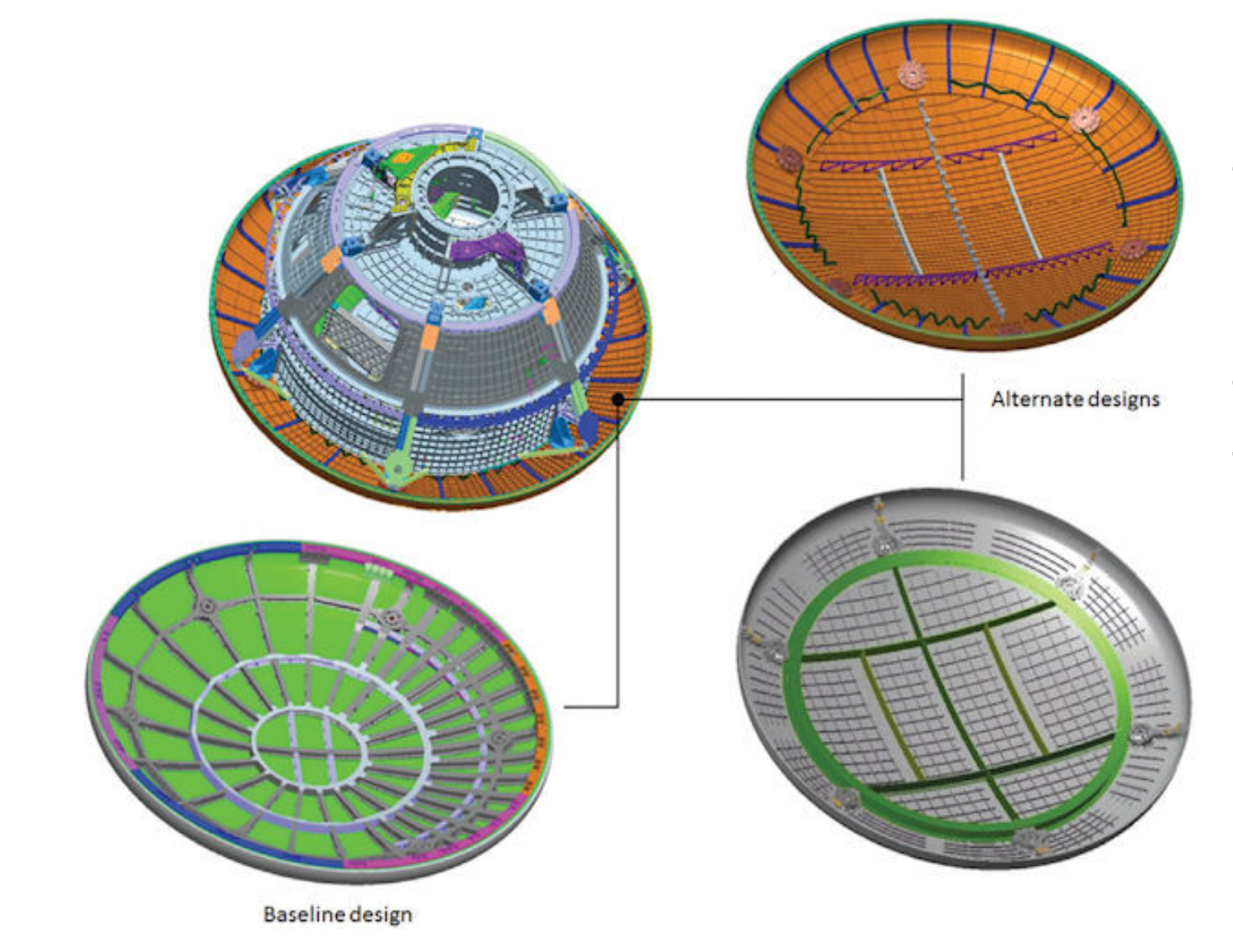
HyperSizer evaluated different structural, metal grid stiffened designs concepts for the NASA Orion outer aeroshell carrier structure to withstand water landing impact. Image courtesy of NASA and Collier Aerospace.
There are three fundamental approaches to generate variant conceptual structural designs.
1st is to repeat the process of generating new CAD surfaces to reflect the geometry of your structure; and from these surfaces, mesh a FEM and apply updated external loads.
This is implemented by importing the new FEM into HyperX .
Though this is referred to as a ‘fresh’ FEM import, the database’s materials, design properties and analysis properties can quickly be reapplied to the new mesh.
The 2nd is to reuse your existing FEM by morphing the mesh and keeping the external applied loads the same.
This is implemented by reimporting the modified FEM into HyperX. HyperX setup stays intact.
A typical use case is an airframe wing trade study of different wing shape designs that vary the chord to camber with an overall increase or decrease in wetted areas. Though these variants have different geometry, the geometry changes can be handled by lofting the existing nodal grids to the new surface. The morphed mesh maintains the original property definitions and is handled with either of our FEM reimport capabilities.
See page FEM Workflow: FEM reimport.
The 3rd is to not use FEA but rather calculate internal forces closed form.
This is usually implemented with spreadsheets that pass data using the HyperX API.
In early launch vehicle studies the rocket’s diameter, length, and placement and sizes of tanks for LOX, Hydrogen, other fuels are traded, as well as lengths of interstages, intertanks, etc. Additionally the internal ullage pressure of the fuel is traded against the weight savings of buckling stable tank walls vs extra weight of turbo pumps.
These multitude of possibilities can be defined in a spreadsheet. Simple closed form equations calculate internal loads such as hoop (Ny) transverse tension from internal pressure as a function of diameter, axial compression from launch F=MA. Being able to call HyperX from the spreadsheet is enabled via scripts using the software’s API.
As a conceptual design example, the NASA Engineering Safety Council (NESC) was tasked to design alternative crew module architectures. While maintaining structural safety, light weight is also paramount.
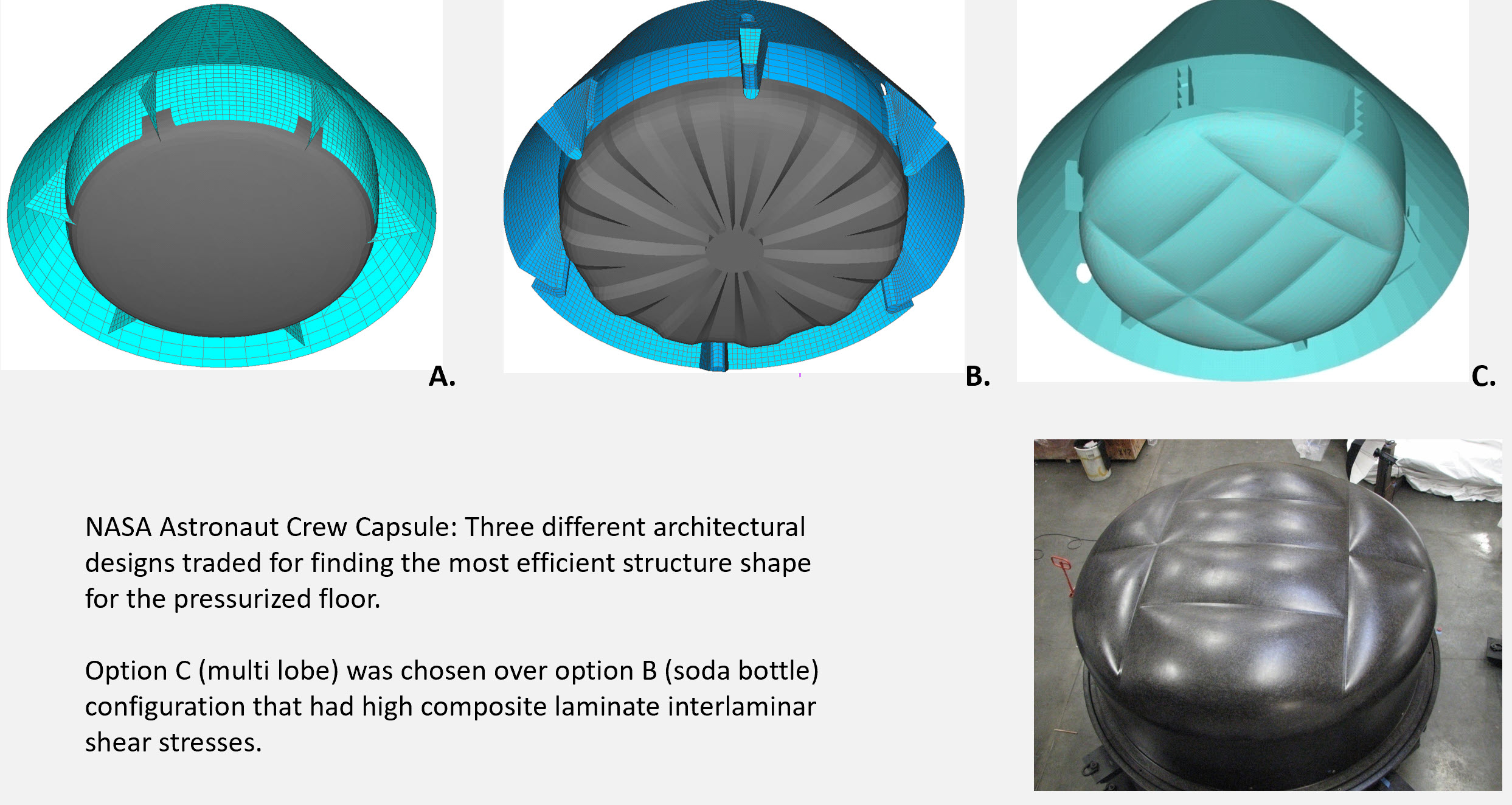
Three different OML shapes were evaluated. Since the driving load case was internal pressure, the mesh was morphed into different shapes without having to recompute external applied loads. The objective was to determine the shape most efficient at supporting the internal load paths. The 2nd approach described above was appropriate and HyperSizer (HyperX) was able to quickly and accurately quantify the weights and structural integrity of the three variants.
Manufacturing Trades
- Large unitized parts vs smaller joined parts
- Integrally machined plate vs riveted sheet metal
- Autoclave vs out of autoclave
Joint Trades
- Single, double, or triple shear joints
- If mechanically fastened: Fastener types, diameters, spacings, rows
- If adhesively bonded: Overlap or stepped, tapers, adhesive material and thickness, bond line lengths
Contact Us
This site is protected by reCAPTCHA and the Google Privacy Policy and Terms of Service apply.